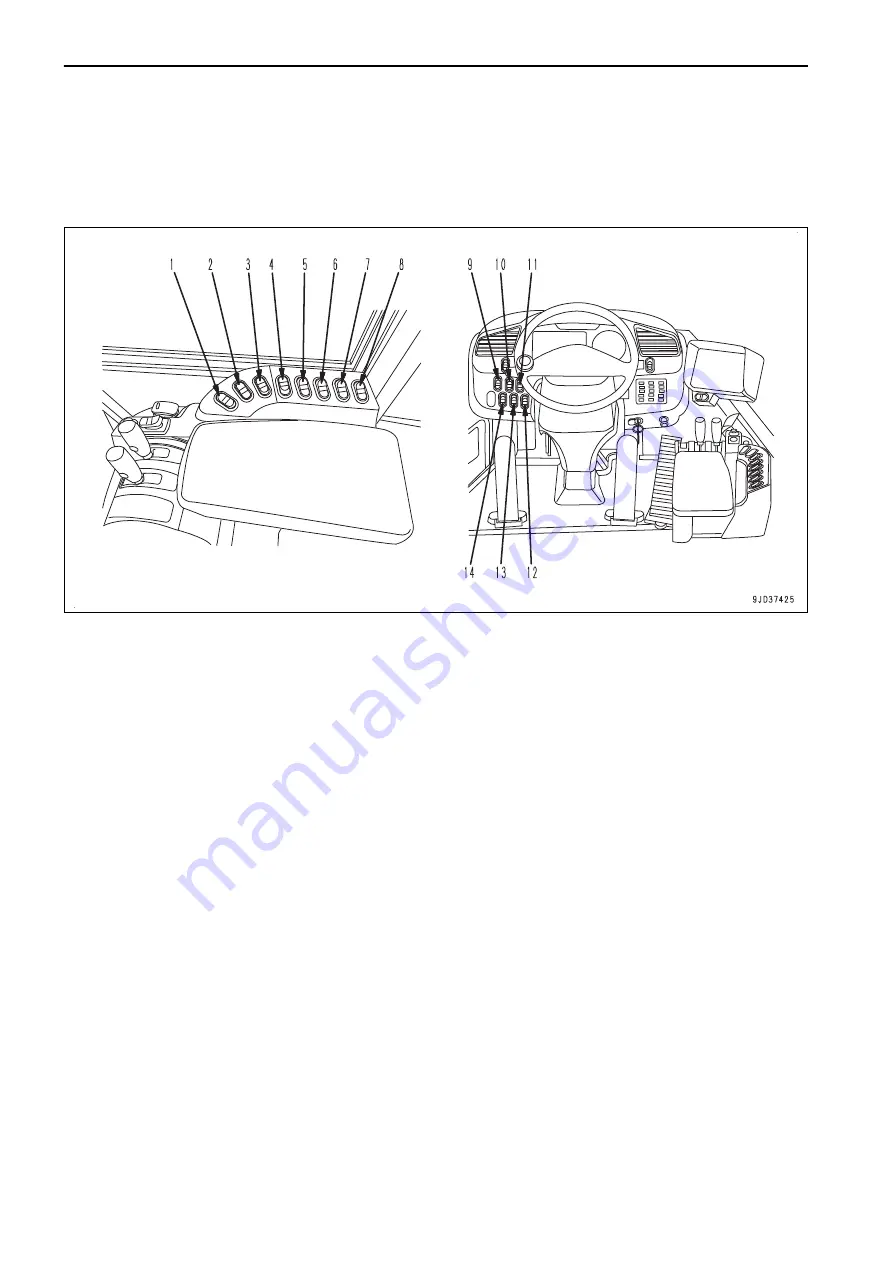
(25) Front wiper switch
(26) Rear wiper switch
(27) Steering tilt lock lever
(28) L.H. brake pedal
(29) Rear heated wire glass switch
(30) Room lamp switch
SWITCH PANEL
R.H. switch panel
(1) Transmission cut-off switch
(1) Transmission cut-off set switch
(2) Power mode selector switch
(3) Transmission shift mode selector switch
(4) Torque converter lockup switch
(5) Directional selector enable switch on R.H. switch
panel (if equipped)
(6) Remote positioner switch
(7) Auto-digging switch
(8) Secondary steering switch
Front switch panel
(9) Front working lamp switch
(10) Rear working lamp switch
(11) Beacon lamp switch (if equipped)
(12) Monitor brightness selector switch
(13) Auto-greasing switch
(14) ECSS switch
GENERAL VIEW
OPERATION
3-4
Summary of Contents for WA480-8
Page 2: ......
Page 19: ...Distributor name Address Phone Fax Service personnel FOREWORD PRODUCT INFORMATION 1 17...
Page 29: ...LOCATION OF SAFETY LABELS SAFETY SAFETY LABELS 2 3...
Page 159: ...SWITCHES 1 ECSS switch 2 Front working lamp switch OPERATION EXPLANATION OF COMPONENTS 3 91...
Page 302: ...Securing position Fixing angle A 61 B 53 C 33 D 38 TRANSPORTATION OPERATION 3 234...
Page 324: ......
Page 397: ...Viewed from the rear side of the machine MAINTENANCE MAINTENANCE PROCEDURE 4 73...
Page 402: ......
Page 403: ...SPECIFICATIONS 5 1...
Page 406: ......
Page 422: ......
Page 423: ...REPLACEMENT PARTS 7 1...
Page 439: ......