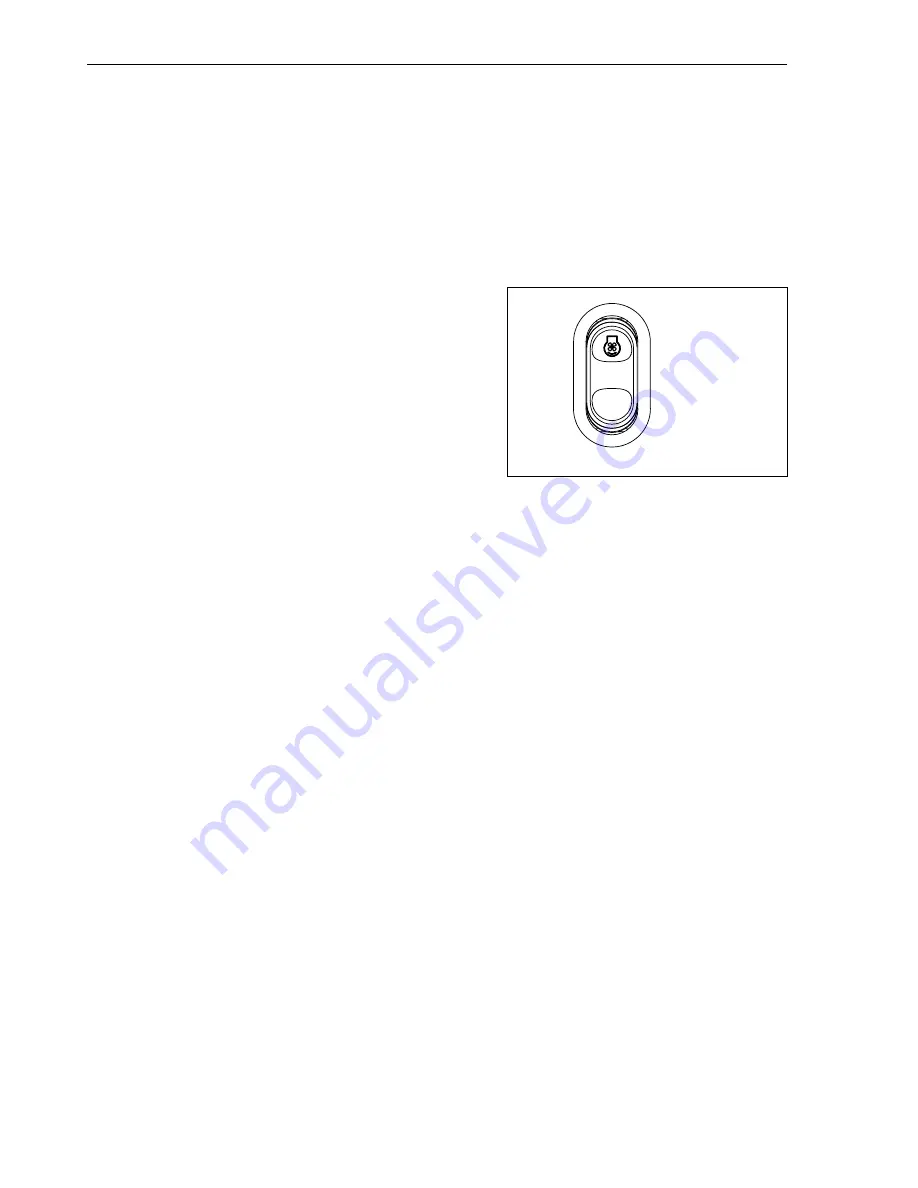
3.2 Explanation of components
Operation
3-62
WA500-6H – VEAM430100
Position (b):
Use this position when lowering the engine speed or when reset-
ting after canceling the RPM set ON/OFF switch.
z
When using the RPM set up/down selector switch
Keep portion (b) of the switch pressed for at least 0.5 sec to
lower the engine speed. When the engine reaches the
desired speed, release the switch. The new speed is
recorded to memory and the setting is made.
29. Cooling fan reverse rotation switch
This switch (29) is used to rotate the cooling fan in the reverse
direction when cleaning the radiator.
Position (a): ON
The pilot lamp inside the switch and the cooling fan reverse rota-
tion pilot lamp on the machine monitor light up. At the same
time, “COOLING FAN REVERSE“ is displayed on the character
display, and the fan is set to rotate in reverse.
Position (b): OFF
The cooling fan is set to rotate in the normal direction.
Stop the engine before operating the switch.
Switching normal rotation -> reverse rotation: With the engine
stopped, do as follows: Starting switch ON -> reverse rotation
switch ON -> check machine monitor -> starting switch START -
> fan reverse rotation
Switching reverse rotation -> normal rotation: Engine at low
speed -> starting switch OFF -> starting switch ON -> reverse
rotation switch OFF -> starting switch START -> fan normal rota-
tion
For details, see "Clean radiator fins with compressed air (4-40)".
REMARK
When the engine is running, even if the switch is pressed, the
direction of rotation of the fan does not change, but the cooling
fan reverse rotation pilot lamp on the machine monitor flashes.
Use the reverse rotation of the fan only for cleaning. For normal
operations, rotate the fan in the normal direction. If operations
are carried out with the fan rotating in the reverse direction, the
machine will not display its full function and will tend to overheat.
GK050069
a
b
Summary of Contents for WA500-6H
Page 2: ......
Page 3: ...Foreword WA500 6H VEAM430100 1 1 1 Foreword...
Page 26: ...1 7 CE Conforming equipment Foreword 1 24 WA500 6H VEAM430100...
Page 254: ...3 7 Troubleshooting Operation 3 188 WA500 6H VEAM430100...
Page 344: ...4 9 Service procedure Every 12000 hours service Maintenance 4 90 WA500 6H VEAM430100...
Page 345: ...Technical Data WA500 6H VEAM430100 5 1 5 Technical Data...
Page 347: ...Technical Data 5 1 Technical data WA500 6H VEAM430100 5 3 GK032301 A B H I G C E F D...
Page 352: ...5 4 Limit values for slopes Technical Data 5 8 WA500 6H VEAM430100...
Page 401: ...Index WA500 6H VEAM430100 7 1 7 Index...
Page 407: ...Notes WA500 6H VEAM430100 8 1 8 Notes...
Page 408: ...Notes 8 2 WA500 6H VEAM430100...
Page 409: ...Notes WA500 6H VEAM430100 8 3...
Page 410: ...Notes 8 4 WA500 6H VEAM430100...
Page 411: ...Notes WA500 6H VEAM430100 8 5...
Page 412: ...Notes 8 6 WA500 6H VEAM430100...