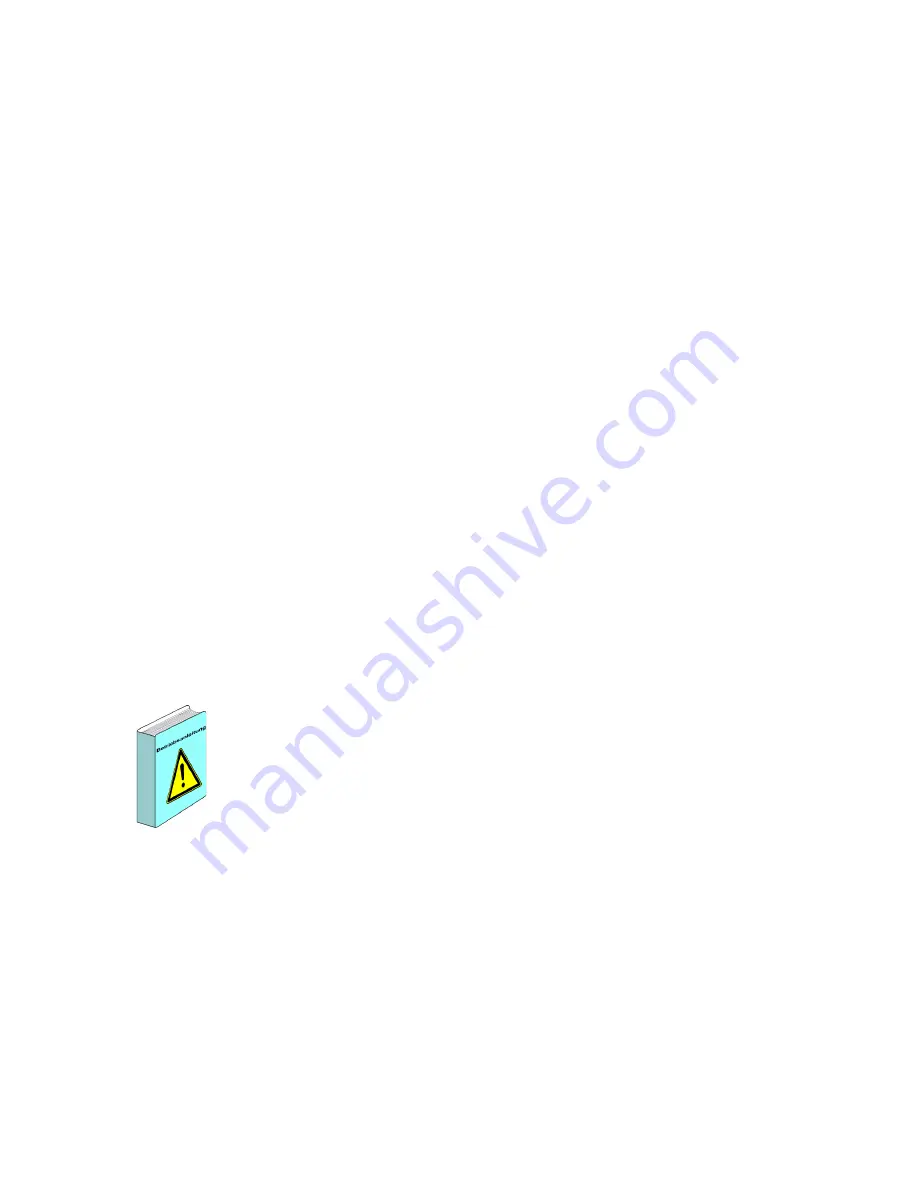
KT-70E / KT-90E / KT-70SE User Manual
Page 7 of 59
24 April 2018
1.2.
Foreword
Dear Customer,
Thank you for choosing the KT-70E / KT-90E / KT-70SE
This manual is an aid to successful and safe operation of the compressor.
These materials are only for information purposes. Changes may be made
without prior notice. Please refer to the manual for compliance to regulations,
for accident prevention and environmental protection.
Keep this manual available where the compressor is in use. Any person who
is authorized to work on the compressor must have read the operating instruc-
tions.
The compressor has been built according to state of the art and recognized
safety regulations. Nevertheless, it can be hazardous.
Read this manual before using the compressor is in operation. It helps you:
•
Prevent risks to the operator,
•
Become familiar with the compressor,
•
To avoid interference due to improper operation,
•
To increase the life of the compressor,
•
To avoid repair costs and downtime,
•
To effectively use the compressor.
1.3.
Documentation
To avoid operating errors and to ensure trouble-free operation of the com-
pressor, the user guide the operator must always be accessible.
All documents are protected within the meaning of the copyright law.
Violations are an offense and liable to compensation. All rights to exercise
intellectual property rights We reserve the right.
Summary of Contents for KT-70E
Page 49: ...KT 70E KT 90E KT 70SE User Manual Page 49 of 59 24 April 2018 Figure F First Stage Cylinder...
Page 51: ...KT 70E KT 90E KT 70SE User Manual Page 51 of 59 24 April 2018 Figure 8 Third Stage Cylinder...
Page 53: ...KT 70E KT 90E KT 70SE User Manual Page 53 of 59 24 April 2018 Figure 10 Filter Housing...
Page 54: ...KT 70E KT 90E KT 70SE User Manual Page 54 of 59 24 April 2018 Figure K Casing...