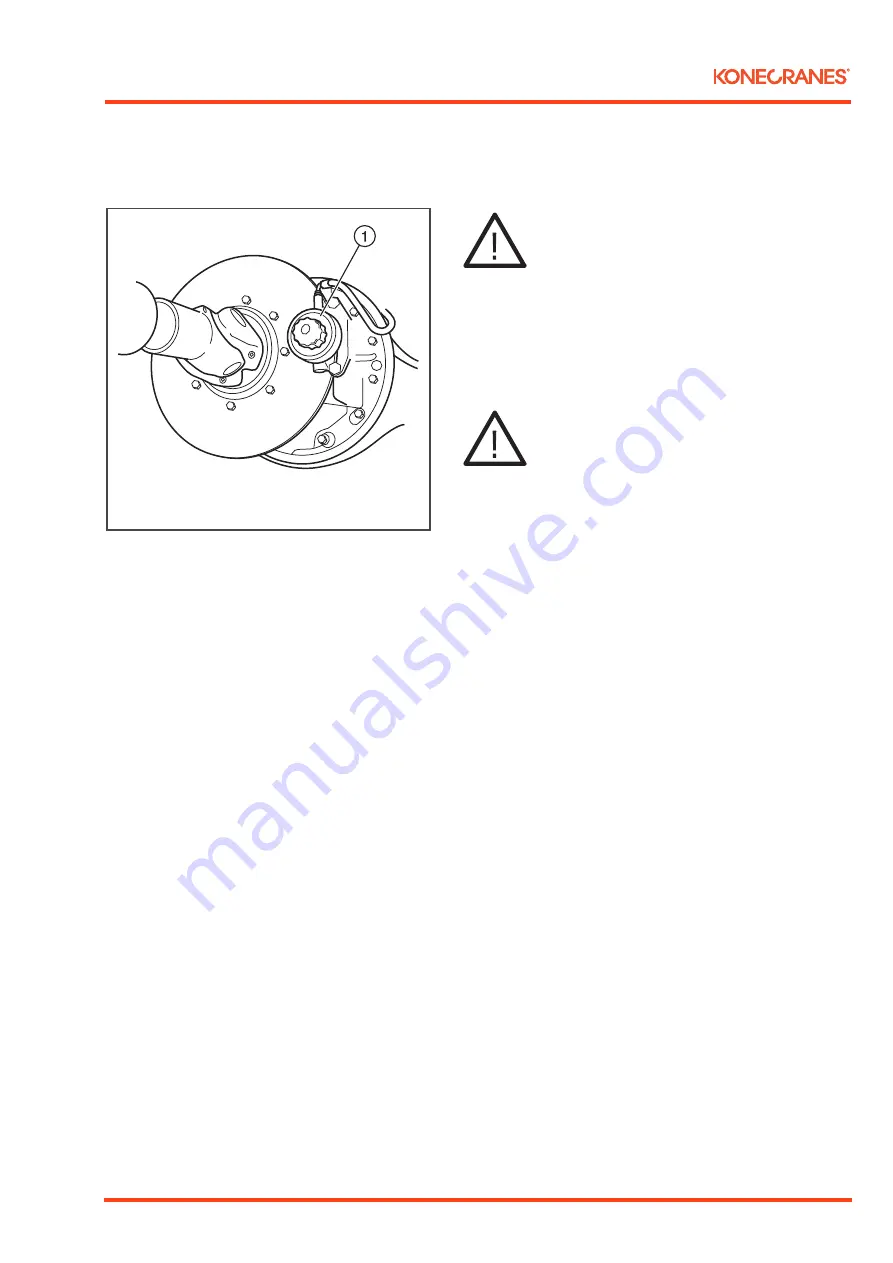
Instruction manual SMV 10 600B – 60 1500B Publ. no. 6196.082 1117, Version 02
37
Lifting and transporting the machine
LIFTING AND TRANSPORTING THE MACHINE
TOWING
BE CAREFUL
As the machine is equipped with a hydraulic brake
system, power assisted steering and a hydraulic
transmission, the engine must be idling when the
machine is being towed.
If this is not possible, the hydraulic parking brake (1) must be
manually released. See also "Releasing the parking brake" on page 95.
• When towing the machine longer distances, the prop shaft must
be removed.
H1764-A
WARNING
The machine will now not have any brakes and
must only be towing using a vehicle that has
sufficient braking capacity to stop both vehicles.
• Use the rear towing peg when fitting a sturdy towing pole on the
machine.
• Fix the other end of the pole to the towing vehicle.
• Place large blocks by the wheels.
• Release the parking brake by tightening the bolt (1).
• When towing, the prop shaft must be disassembled before
towing.
• Tow the machine with great care never exceeding 3-5 kph.
• It will still be possible to steer the machine even though it will
be very heavy due to the loss of power assisted steering.
• After repairs have been performed, the functioning of the brakes
must be inspected and the parking brake be adjusted.
• The prop shaft must be fitted and retightened.
Instruction manual SMV 10 600B – 60 1500B Publ. no. 6196.082 1117, Version 02