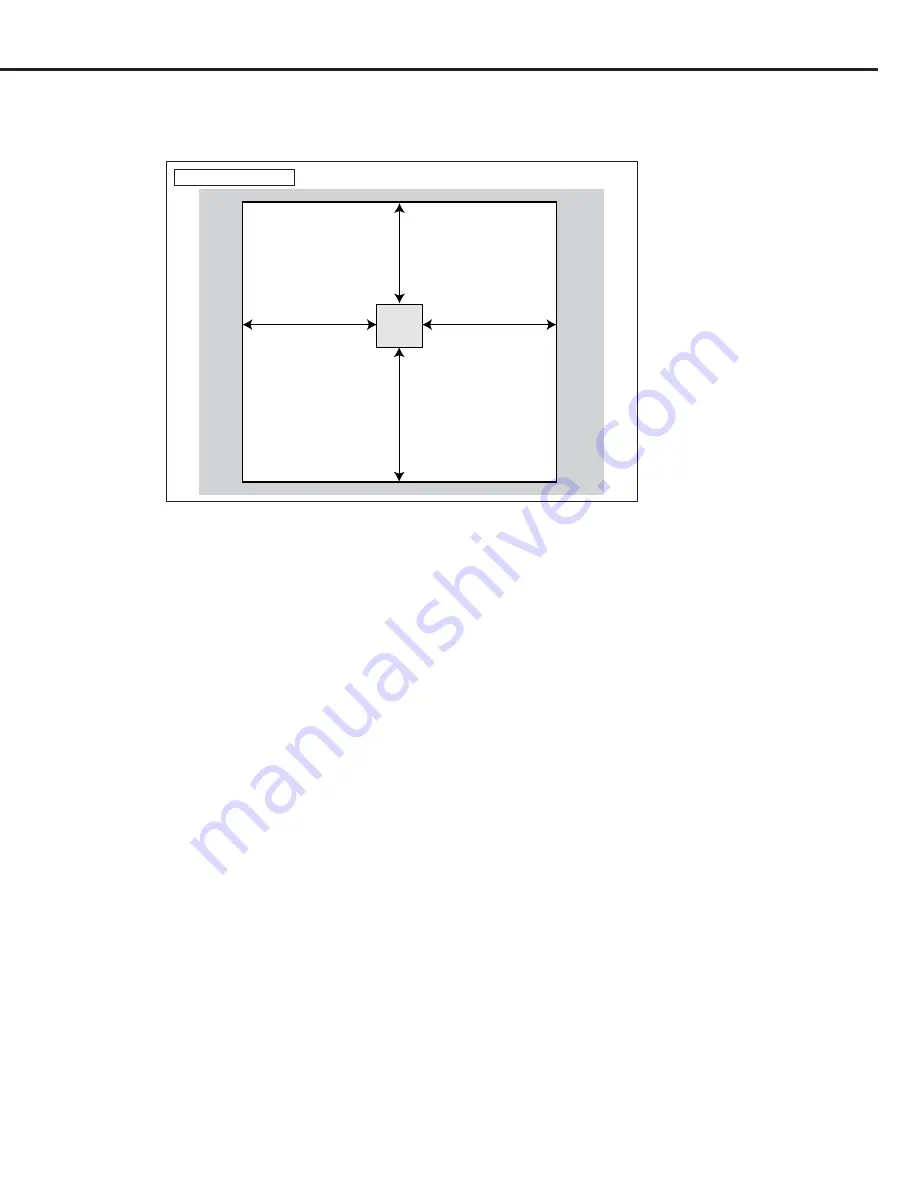
Ch.1 Pre-installation Information
< 21 >
DRYPRO Vstage MODEL 793 Installation Manual Ver.1.00 2004.11
Checking Power Supply Conditions
Check to ensure that a power outlet meeting the requirements below is available at
the place of installation.
- Voltage : AC120V (UL), AC220V-240V (CE)
- Frequency : 60Hz (UL), 50/60Hz (CE)
- Maximum current consumption: 9A(UL), 4.5A(CE)
- Ground : Type D
Checking the Place of Unpacking
Check to ensure that a space of 2.5m or more is allowed at the front (the side where
the locking screws are located) of the palette.
When unpacking DRYPRO 793, be sure to unload the unit from the front of the
palette.
Checking the Route of Transportation
Check to ensure that the route from the place of unpacking and the place of
installation meets the following requirements.
- Ensure that there are no steep gradients or steps that are likely to expose
DRYPRO 793 to shocks during transport.
- Ensure that entrances into and exits from any rooms through which DRYPRO 793
will be transported are of adequate dimensions to allow safe passage.
- Ensure that the floors on the rout of transportation are capable of supporting the
weight of DRYPRO 793 (approximate weight: 255kg (without sorter), 285kg (with
sorter) without warping or buckling.
Checking the Area where Power and Ethernet Cables will be Laid
The person responsible for laying cables must check the following items.
- The location of the hub to which DRYPRO 793 will be connected, the route along
which the Ethernet cable will be laid and the required cable length.
- The location of the power outlet (3P) to which DRYPRO 793 will be connected, the
route along which the power cable will be laid and the required cable length.
Check also to ensure that cables will be laid along a safe route, not, for example,
crossing corridors.
Checking Maintenance Space
Check to ensure that the place of installation allows for the maintenance space
dimensions shown below.
1000mm minimum
1000mm minimum
1000mm minimum
800mm minimum
DRYPRO
793
Front of
Main Body
Maintenance Space