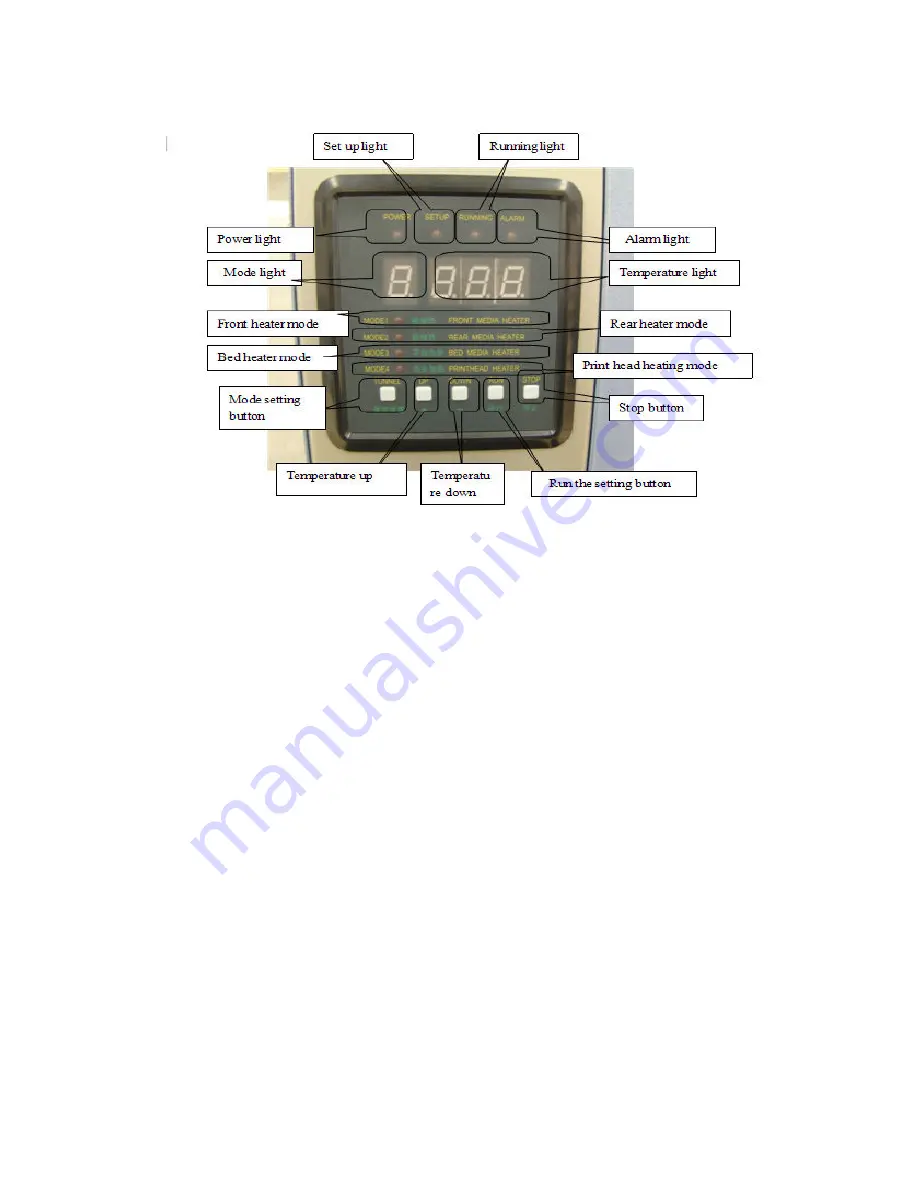
25
Power light:
When power is on, the indicator light on, if not on, the board has no power
to work.
Set light:
When the light is on, the setting mode starts, press the mode button to enter
The setting mode.
Running light:
The indicator light is on when the platform is under work (heating), if the
light is off, the current platform does not work, or the temperature has reached the set
temperature.
Alarm light:
Light is on when there is problem in current platform heating, the lack of
temperature sensors.
Mode light:
Displays the current mode, including the working and setting state. There are
four heating modes on the heating control panel: front heater, bed heater, rear heater and
print head heater. Mode light under working will continue to display four different modes
(1.2.3.4) Press mode button into the setting state, press the mode button to change the
mode channels.
Temperature light:
In the working state it displays the current temperature, in the
setting state, it shows the set temperature.
Front heater mode:
The heating for front printing platform, the light indicates the
current mode under working and shows front heater temperature.
Rear heater mode:
The heating for rear printing platform, the light indicates the current
mode under working and shows rear heater temperature.
Bed heater mode:
The heating for bed printing platform, the light indicates the current
mode under working and shows bed heater temperature.
Summary of Contents for KM1024
Page 1: ...1 Printer KONICA KM256 512 1024...
Page 21: ...17...
Page 22: ...18 5 2 KM256 512 1024 carriage board connection and factory writer KM512 1024...
Page 23: ...19...
Page 24: ...20 KM256...
Page 25: ...21 5 3 power outlet Main power Heater power Main power outlet Heater power outlet vacuum...