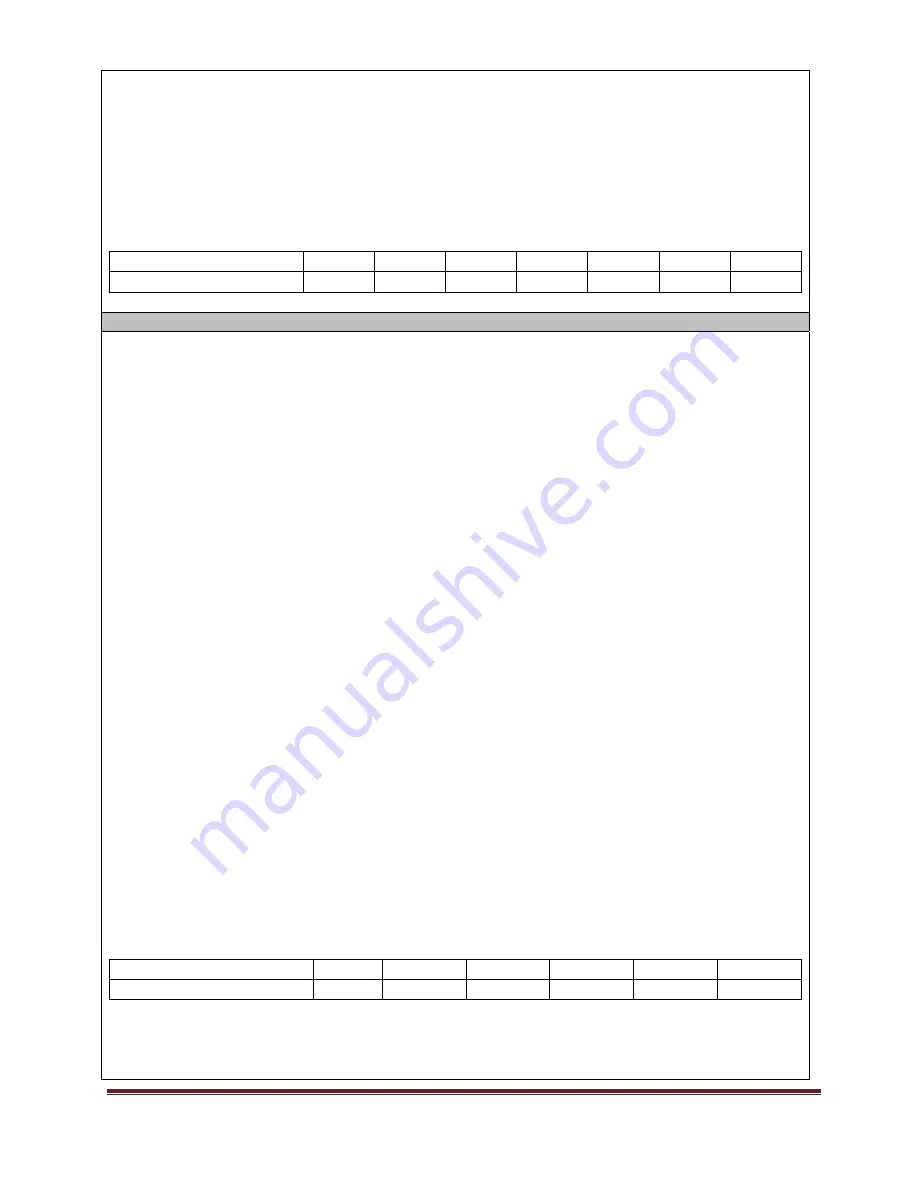
BEAR
IT
Page 24
automatically selected according to the water boiler temperature and the value of Boiler Thermostat Th24:
* Boiler water temperature ≤Th24–D08
the system goes to the maximum available power
* Th24–D08<boiler water temperature<Th24
the combustion power is chosen proportionally (the greater is
the difference between the water temperature and the thermostat Th24, higher will be the chosen power.
* boiler water temperature≥Th24
the system goes to Power 1 or, if enabled, at Modulation Power
The parameter d08 must be a multiple of the number of operating powers minus one.
Factory adjusted: A06=1, Modality=[A], Thermostat Boiler Th24=60 °C, Delta D08=6 °C, P03=6
Water Temperature (°C)
≤ 54
55 ÷ 56
56 ÷ 57
57 ÷ 58
58 ÷ 59
59 ÷ 60
≥ 60
Combustion Power
6
5
4
3
2
1
Mod
Heating Fan
In this product are assembled heating fan to heat room where the product is located.
‐ If exhaust temperature is greater than Thermostat
T07
at the end of
T69
, it goes at maximum power (99%)
‐ If the user set a power different from 0:
o
it will be On only if exhaust temperature is greater than
Th05
Thermostat (Default 80 degrease)
o
In Modulation for Room Thermostat or Chrono if
A11
=
0
the fan is Off, if
A11
=
1
the fan goes at Power 1
o
In Standby for Room Thermostat or Chrono if
A03
=
0
the fan is Off, if
A03
=
1
the fan goes at Power 1
o
In Ignition if
A08
=0
the fan is Off, if
A08
=
1
the fan goes at Power 1
o
In every state with
A01
=
5
,
for Room Thermostat if
A11
=0
the fan is Off, ,if
A11
=
1
the fan Power is 1
Optionally heating fan can be switched Automatically, OFF or adjusted manually from speed 1 (min) to
speed 6 (max) from control panel (see User Menu 2). Our suggestion is users to choice “Auto”. On this mode
factory adjustment for parameter
P06
is “2”. The heating fan is working proportional to the exhaust tempe‐
rature. If some user prefers different Automatically adjustment can use next procedure with following
functioning:
If the user chooses the automatic mode of heating, the system selects the power. By setting the parameter
P06
in the Default Settings, it is possible to manage the heating power:
P06=1 (Same as Combustion Power)
The Heating power is the same as Combustion power.
P06=2 (Proportional to exhaust temperature)
The system selects the heating power according to the value of exhaust temperature, of
Th05
Thermostat
and of parameter
D04
(
D04
has to be a multiple of the powers’ number less one).
Example
:
Th05
= 60°C,
D04
=100 °C,
P03
=5
Exhaust temperature <
Th05
Heating Fan is off.
Exhaust temperature >
Th05
+
D04
=160 °C the system goes to maximum Power, Power 5.
Th05
< Exhaust temperature <
Th05
+
D04
the system starting from 60°C, every 25 °C increases one
power of functioning:
Exhaust Temperature (°C)
≤ 60
60 ÷ 84
85 ÷ 109
110 ÷ 134
135 ÷ 159
≥ 160
Heating Power
Off
Power 1
Power 2
Power 3
Power 4
Power 5
P06=3 (Proportional to room temperature)
The system selects the heating power according to the value of room temperature, of
Th05
Thermostat and