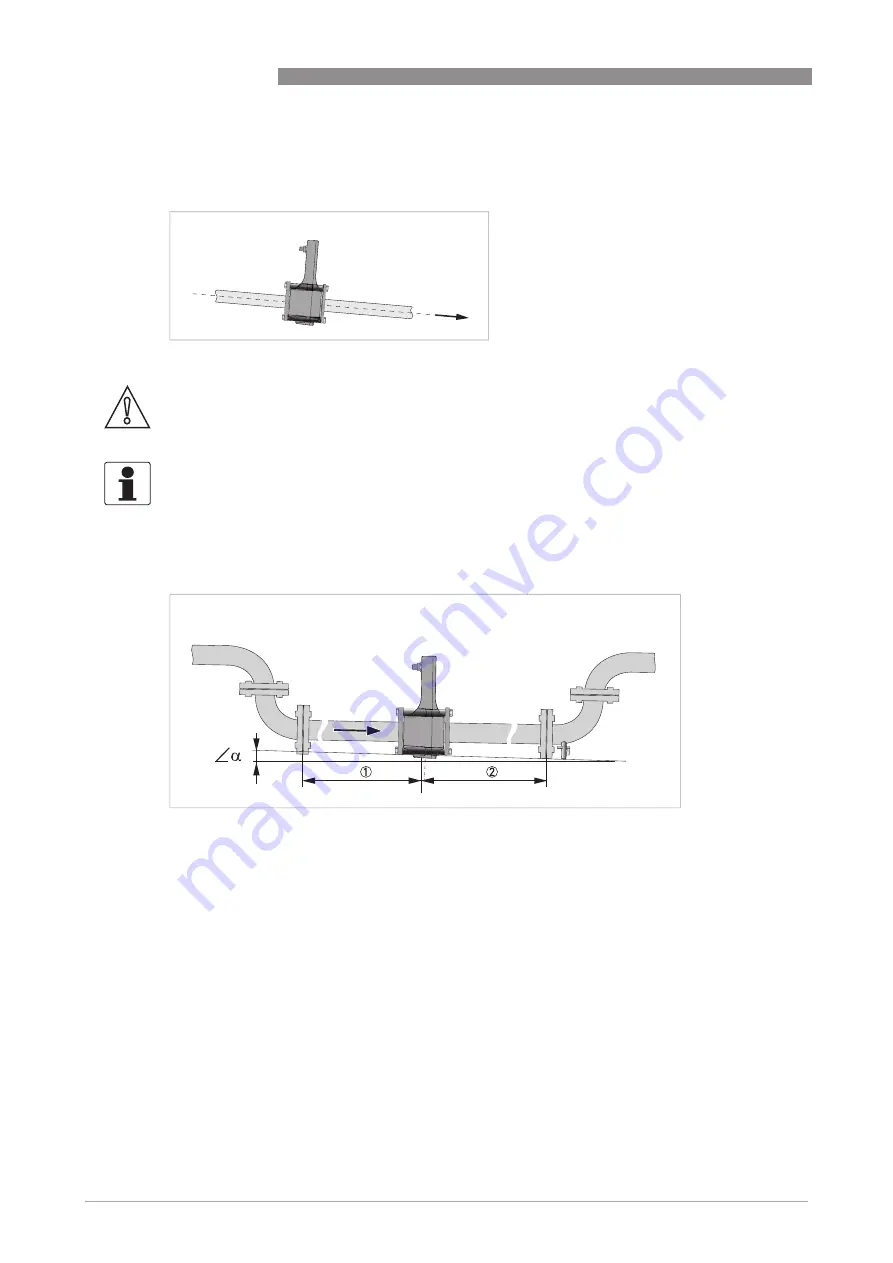
2
INSTALLATION
8
BATCHFLUX 3100 C
www.krohne.com
09/2020 - 4008472601 - QS BATCHFLUX 3100 - R01 en
2.7 Installation conditions
2.7.1 Inlet and outlet
D
> 25
°
Figure 2-6: Horizontal piperun
CAUTION!
Install in a slightly descending pipe section , to prevent air from collecting and to avoid faulty
measurements (meter can drain).
INFORMATION!
Support the pipeline on both side of the flowmeter. Make sure the M12 connector is on the flow
inlet side.
Figure 2-7: Inlet and outlet section
1
Refer to chapter "Bends in 2 or 3 dimensions"
2
t
2 DN
3
Drain valve (to empty pipeline)
3
Summary of Contents for BATCHFLUX 3100
Page 21: ...NOTES 5 21 BATCHFLUX 3100 C www krohne com 09 2020 4008472601 QS BATCHFLUX 3100 R01 en...
Page 22: ...5 NOTES 22 BATCHFLUX 3100 C www krohne com 09 2020 4008472601 QS BATCHFLUX 3100 R01 en...
Page 23: ...NOTES 5 23 BATCHFLUX 3100 C www krohne com 09 2020 4008472601 QS BATCHFLUX 3100 R01 en...