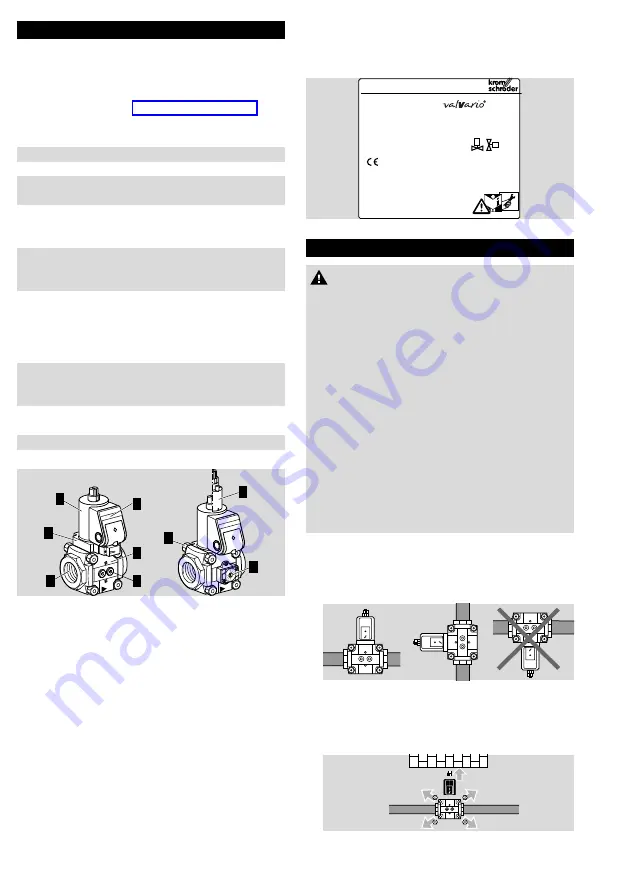
VAA · Edition 09.21
EN-2
CHeCKInG tHe UsAGe
The valVario solenoid valve for air VAA is used for the
staged control of industrial burners in cold air oper-
ating mode.
This function is only guaranteed when used within the
specified limits – see page 7 (Technical data). Any
other use is considered as non-compliant.
type code
VAA
Solenoid valve for air
1-3
Sizes
–
Without flange
15–65
Inlet and outlet flange nominal size
R
Rp internal thread
F
Flange to ISO 7005
n
NPT internal thread
/n
Quick opening, quick closing
/L
Slow opening, quick closing
/R
Slow opening, slow closing
W
Mains voltage 230 V AC, 50/60 Hz
Q
Mains voltage 120 V AC, 50/60 Hz
K
Mains voltage 24 V DC
P
Mains voltage 100 V AC, 50/60 Hz
Y
Mains voltage 200 V AC, 50/60 Hz
s
With PS and visual position indicator
G
With PS for 24 V and visual position
indicator
R
Viewing side: right
L
Viewing side: left
Part designations
2
8
6
9
4
1
7
5
3
1
Solenoid actuator
2
Flow body
3
Connection box
4
Connection flange
5
Position switch
6
Damping unit
7
Connection parts
8
Sealing plug
9
Variable bypass
type label
Mains voltage, electrical power consumption, ambient
temperature, enclosure, inlet pressure and installation
position: see type label.
Elster GmbH
Osnabrück, Germany
Vxx
.XXXX
InstALLAtIon
CAUtIon
Incorrect installation
Please observe the following to ensure that the
unit is not damaged during installation and oper-
ation:
– Sealing material and dirt, e.g. thread cuttings,
must not be allowed to get into the valve
housing.
– A filter must be installed upstream of every
system.
– Dropping the device can cause permanent
damage. In this event, replace the entire device
and associated modules before use.
– Do not clamp the unit in a vice. Only secure the
flange by holding the octagon with a suitable
spanner. Risk of external leakage.
– Solenoid valves with position switch VAA..S or
VAA..G: actuator cannot be rotated.
➔
Install the unit in the pipe free of mechanical stress.
➔
Installation position: black solenoid actuator in the
vertical upright position or tilted up to the horizontal,
not upside down. In humid environments: black
solenoid actuator in the vertical upright position only.
➔
The housing must not be in contact with masonry,
minimum clearance 20 mm (0.79").
➔
Ensure that there is sufficient space for installation,
adjustment and maintenance work. Minimum clear-
ance of 25 cm (9.8") above the black solenoid actuator.