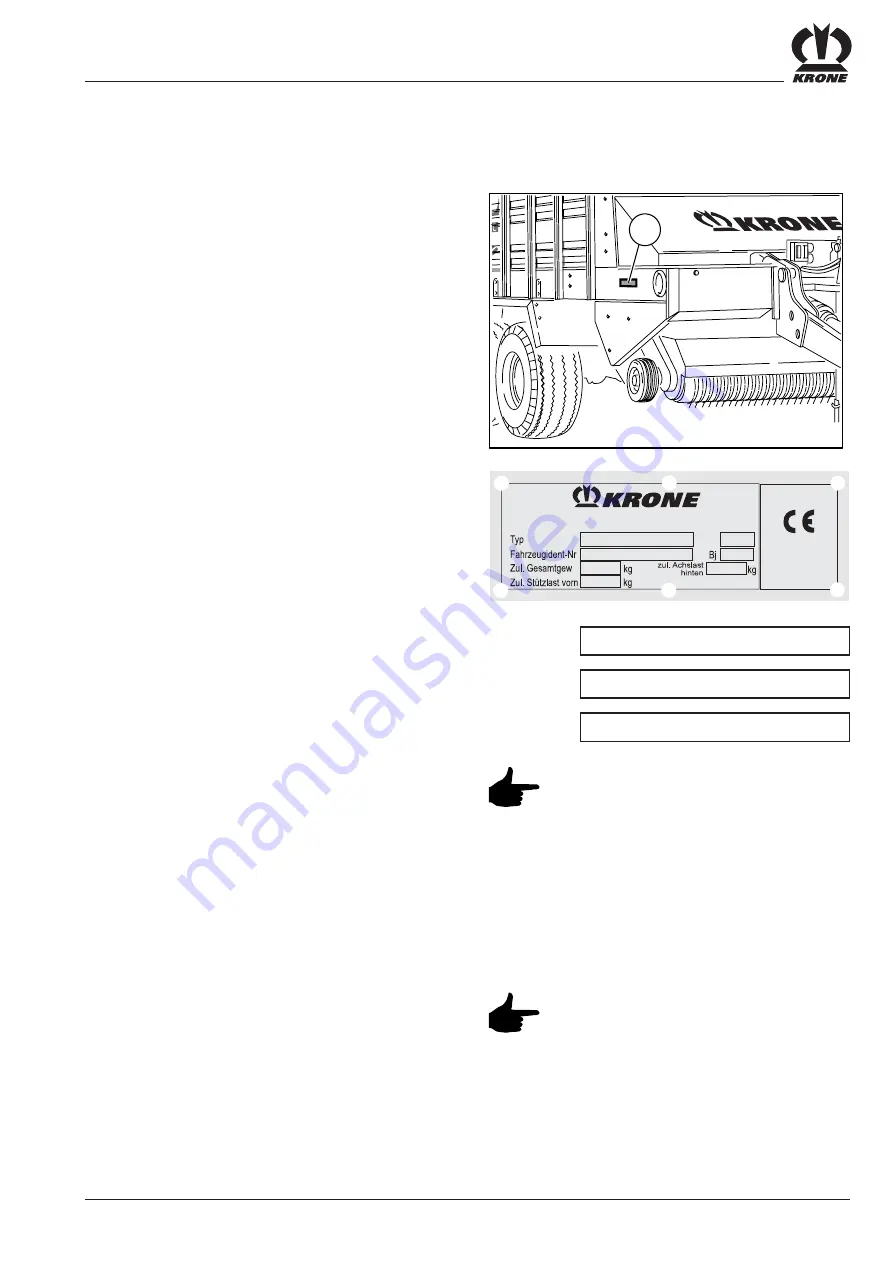
I - 1
General information
1
General information
1.1 Use
The short-cut feeder wagon is a feeder wagon with
metering rollers. It is designed for the collection,
transport and putting down of agricultural stalk material.
The variable cutter theoretically provides for cutting
lengths up to 40mm.
1.2 Information on the product
1.2.1 General information
These operating instruction apply to short-stalk loading
wagon Models XXL-RGD and 4XL-RGD from Machine
no. 515 000
1.2.2 Manufacturer’s address
Maschinenfabrik Bernard Krone GmbH
Heinrich-Krone-Strasse 10
D-48480 Spelle (Germany)
Telephone: 0 59 77/935-0
Facsimile 0 59 77/935-339
E-mail: info.ldm@krone.de
1.2.3 Certification
Declaration of conformance (requirements of EC
Directive 89/392/EEC; 3 and Directive amendment of
22.07.93 are complied with)
See inside title page
1.2.4 Identification label
M a s c h i n e n f a b r i k B e r n a r d K r o n e G m b H
Heinrich-Krone-Str. 10 D-48480 Spelle
M a d e i n
G e r m a n y
Model
Year of
manufacture
Vehicle-
ident-no.
The whole identification label has
documentation value and must not be
altered or made unrecognisable
1.2.5 Information for enquiries and
orders
When ordering spare parts, the model number, vehicle
identification number and the year of manufacture of
the corresponding machine must be quoted.
Spare parts form other manufacturers
may only be used after consultation
with the manufacturer of this
equipment. In the interest of safety,
only genuine parts and accessories
authorised by the manufacturer should
be used. No liability can be accepted
for consequences resulting from the
use of other parts.
KDW00050
1
Summary of Contents for 4XL-RGD
Page 4: ...Foreword ...
Page 10: ...I 4 General information ...
Page 15: ...II 5 Safety ...
Page 22: ...II 12 Safety ...
Page 64: ...VI 18 Maintenance ...
Page 66: ...VII 2 Overwintering ...
Page 68: ...VIII 2 Recommissioning ...
Page 70: ...IX 2 Faults causes and removal ...
Page 80: ...A 10 Appendix Operator friendlyoperation A2 Electrical circuit diagram ...
Page 81: ...A 11 Appendix ...
Page 82: ...A 12 Appendix ...
Page 83: ...A 13 Appendix ...