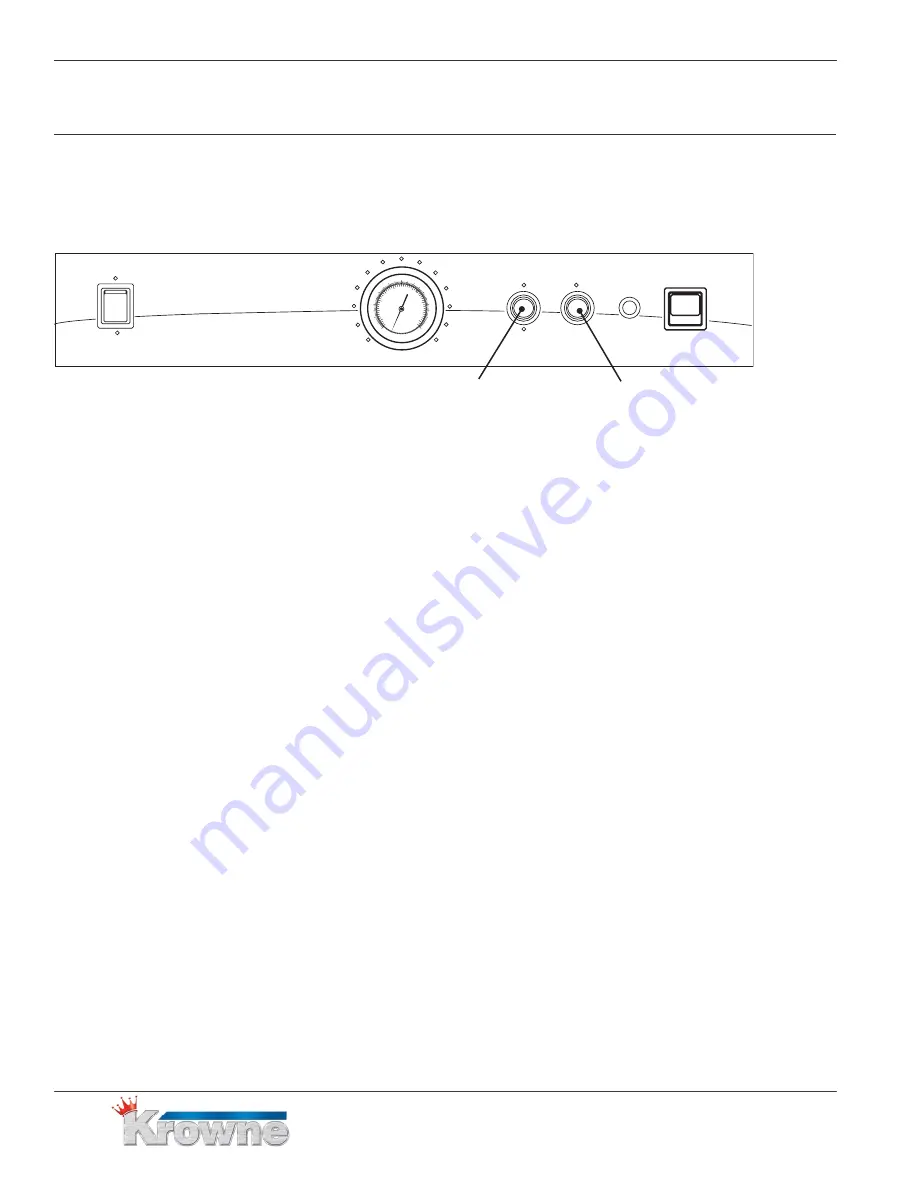
12
Krowne Metal Corporation
|
100 Haul Road
|
Wayne, NJ 07470
Phone: (800) 631-0442
|
Fax: (973) 872-1129
|
www.krowne.com
Chemical Dispensing Pumps
Initial Start-up
1.
There are two chemical dispenser prime push buttons on the glasswasher. The first is labeled
DET and SAN on the front control panel; the second is labeled R/A.
DET = Detergent
SAN = Sanitizer
R/A = Rinse-aid
2.
Make sure the chemical containers are full and the correct pick-up tubes are in their containers.
3.
Turn the glasswasher power switch ON. The switch will illuminate and the glasswasher will fill
with water.
4.
Open the glasswasher door, then push and hold the first prime push button UP to the
DET position until detergent enters the wash tank compartment.
Release the PRIME push button.
5.
Push and hold the prime push button DOWN to the SAN position until sanitizer
is observed entering the wash tank compartment. Release the Prime push button.
6.
Push and hold the second prime push button UP to the R/A position until rinse-aid
is observed entering the wash tank compartment. Release the Prime push button.
7.
Run three empty cycles to remove chemicals in the wash tank.
8.
Priming is complete.
Priming the Chemical Dispensing Pumps
R/A
DET
SAN
PRIME
START
TEMPERATURE
ON
I
O
POWER
OFF / DRAIN
0
20
40
60
80
100
120
140
160
180
200
220
100
80
60
40
20
Rinse-aid
Prime Switch
Detergent and Sanitizer
Prime Switch
Summary of Contents for GWD-24
Page 48: ......