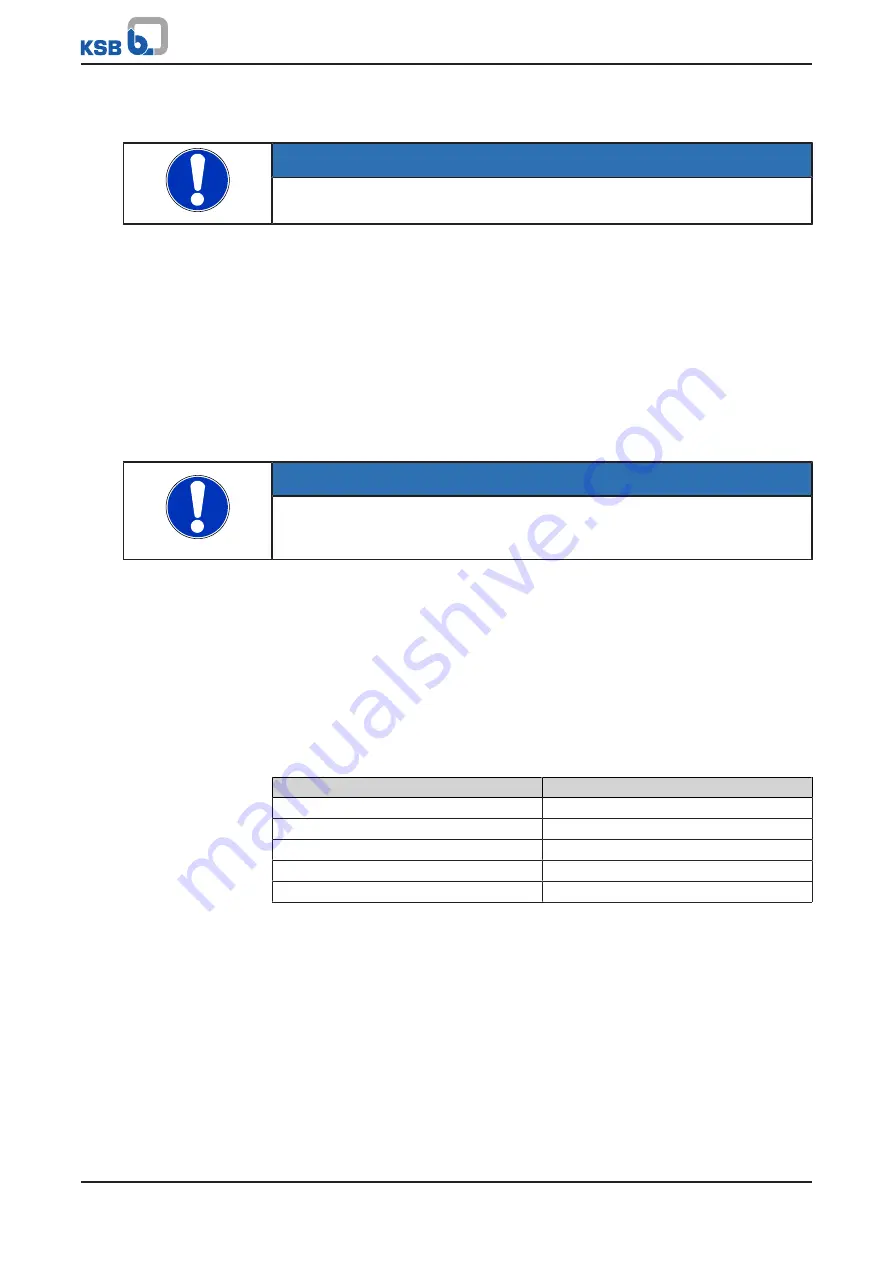
5 Installation/Dismantling
15 of 28
4EYS / 4EYT
1974.91/01-EN
11. Tighten the grub screws, observing the installation dimension and tightening
torques.
NOTE
Do not re-use cup point grub screws!
Used grub screws must be replaced by new cup point grub screws.
ð
Cup point grub screws must not be re-used. Repeated tightening can impair
the reliability of force transmission.
12. Carry out further installation instructions given in the pump’s operating manual.
5.4 Removing the mechanical seal
The rules of sound engineering practice and the pump manufacturer's general
provisions apply. Tidiness and cleanliness are essential for proper execution of the
installation work.
ü
The operating manual for the pump is on hand.
ü
The mechanical seal is accessible.
ü
The components have been placed down and secured in a horizontal position.
NOTE
If any dismantling instructions and/or a dismantling sequence are specified in the
product literature of the pump/machinery into which the mechanical seal is to be
installed, they must be observed.
1. Carefully remove mating ring carrier 476 including mating ring 475 and O-ring
412.52.
2. Loosen grub screws 904. Pull the rotating assembly of the mechanical seal off
the shaft.
3. Jointly remove O-ring 412.52 and mating ring 475 from mating ring carrier 476.
4. Carry out further dismantling instructions given in the operating manual of the
pump/machinery.
5.5 Tightening torques
Table 5:
Tightening torques
Thread
[Nm]
M5
4
M6
8
M8
15
M10
20
M12
25
Summary of Contents for 4EYS
Page 1: ...KSB Mechanical Seal 4EYS 4EYT Installation Operating Manual...
Page 26: ......
Page 27: ......