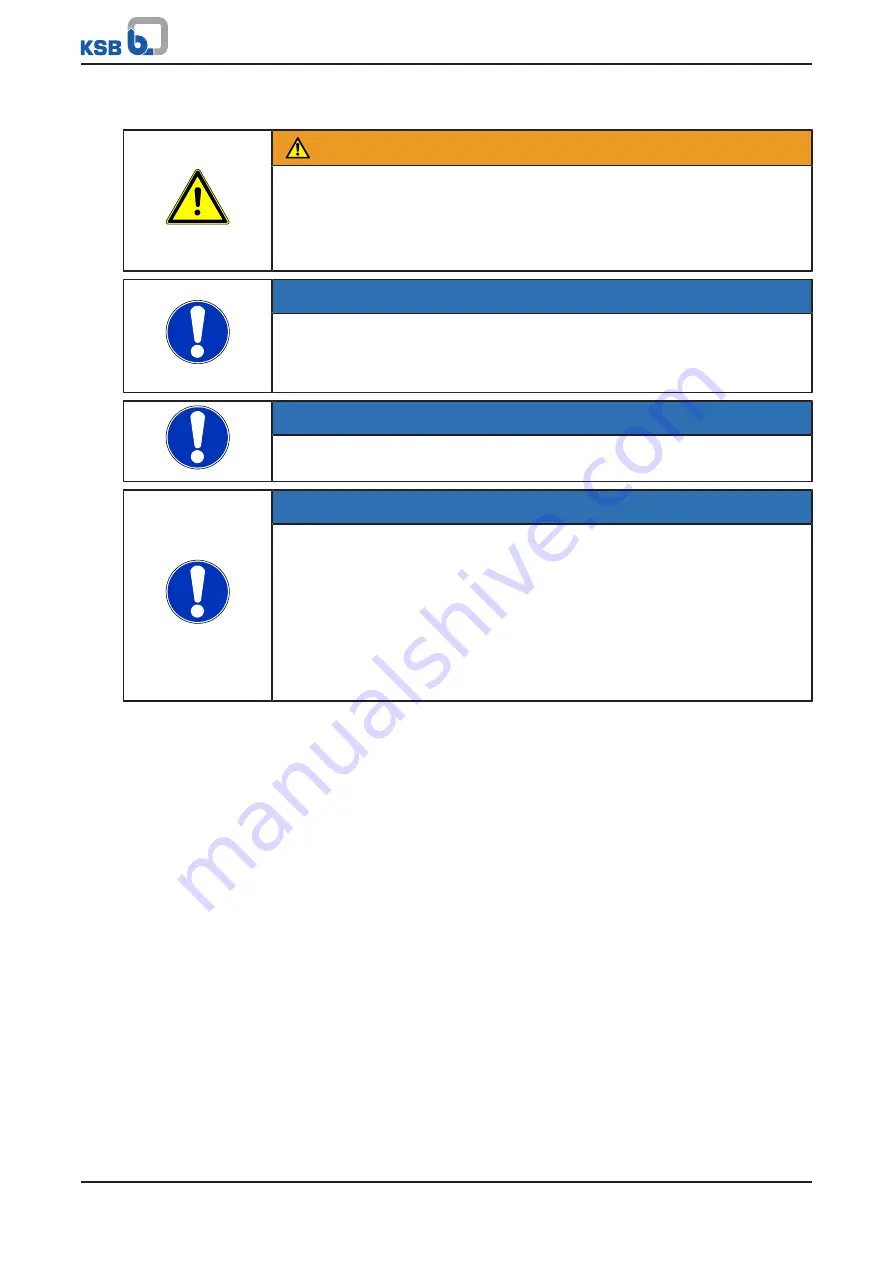
8 Trouble-shooting
22 of 32
4K / 4KD
8 Trouble-shooting
WARNING
Improper work to remedy faults
Risk of injury!
▷
For any work performed to remedy faults, observe the relevant information
given in this operating manual and/or in the product literature provided by the
accessories manufacturer.
NOTE
Prior to conducting any work on the mechanical seal during the warranty period
contact the manufacturer. KSB Service will be pleased to help you. Non-compliance
with this instruction will lead to forfeiture of any and all rights to claims for
damages.
NOTE
For any failures you cannot remedy or whose cause cannot be identified, contact
the responsible KSB service centre.
NOTE
Maintenance work, servicing work and installation work can be carried out by
KSB Service or authorised workshops.
KSB Service GmbH | Service Centre Pegnitz
E-mail: service-center.sued@ksb.com
KSB Service LLC | Service Centre Abu Dhabi
E-mail: ksb@ksb.ae
Contact for general queries:
E-mail: TSS_PE_Mechanical.Seals@ksb.com
Further contacts see:
What to do in the event of a failure
▪
Determine and document the nature of the fault/malfunction.
▪
Monitor the development of leakage quantity. Stop the pump if necessary.
Consistent, flowing leakage indicates a mechanical seal damage.
Summary of Contents for 4K Series
Page 1: ...KSB Mechanical Seal 4K 4KD For the KWP Type Series Installation Operating Manual ...
Page 30: ......
Page 31: ......