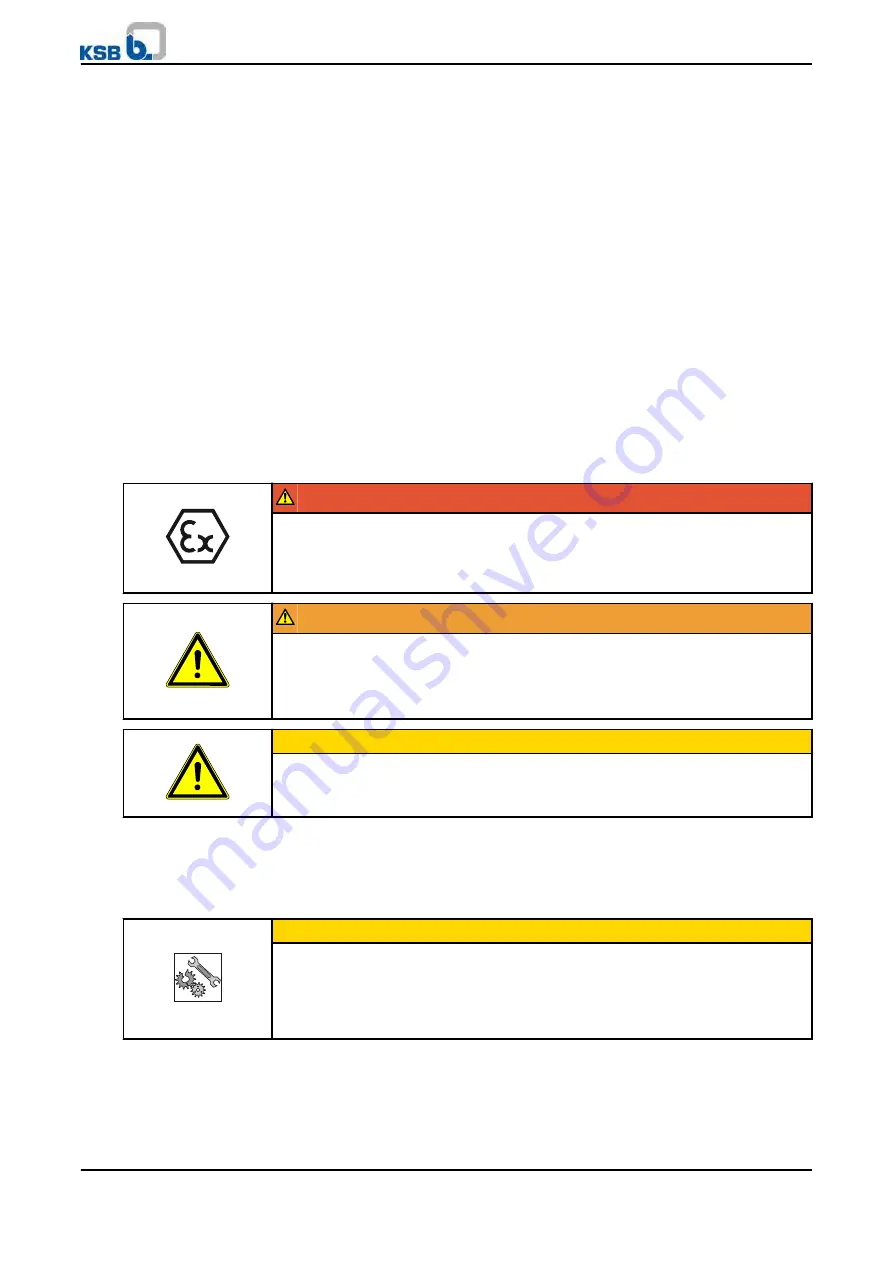
On pump sets with reinforced bearings (
Section 4.4 Page 16) the pump-end rolling
element bearings can be re-lubricated. Relubricate these bearings as part of the
maintenance work.
7.2.2.2.1 Grease quality
The following greases can be used to lubricate the rolling element bearings:
▪
Lithium soap grease suitable for high temperatures
▪
ESSO UNIREX N3
▪
FAG ARCANOL L40
▪
TEXACO HYTEX EP3/DEA Pragon
7.2.2.2.2 Grease quantity
Use 60g grease to lubricate the rolling element bearings.
7.2.2.2.3 Re-lubrication
An encapsulated water-tight lubricating nipple allows re-lubrication of the angular
contact ball bearings without opening the pump.
DANGER
Dry running
Risk of explosion!
▷
Re-lubricate explosion-proof pump sets outside potentially explosive
atmospheres.
WARNING
Hands or objects inside the pump casing
Risk of injuries, damage to the pump!
▷
Never insert your hands or any other objects into the pump.
▷
Check that the inside of the pump is free from any foreign objects.
CAUTION
Incomplete re-lubrication
Bearing damage!
▷
Always re-lubricate the bearings with the pump set in operation.
✓
The pump set has been positioned on a level surface.
✓
The pump set is secured against tipping over.
1. Remove screwed plug 903.46 and joint ring 411.46.
2. Connect the pump set to the power supply. (
CAUTION
Pump set running dry
Increased vibrations!
Damage to mechanical seals and bearings!
▷
Never operate the pump set for more than 60 seconds outside the fluid to be
handled.
3. Start up the pump set.
4. Fill in grease via lubricating nipple 636.02
5. Disconnect the pump set from the power supply again and make sure it cannot
be switched on accidentally.
Grease quality
Recommended
commercially available
brands
Pump sets with reinforced
7 Servicing/Maintenance
42 of 74
Amarex KRT
Goodnal STP ST041 Sewage Delivery (Amarex KRT Submersible Motor Pump) Vendor Manual
Q-Pulse Id VM362
Active 29/10/2013
Page 44 of 96