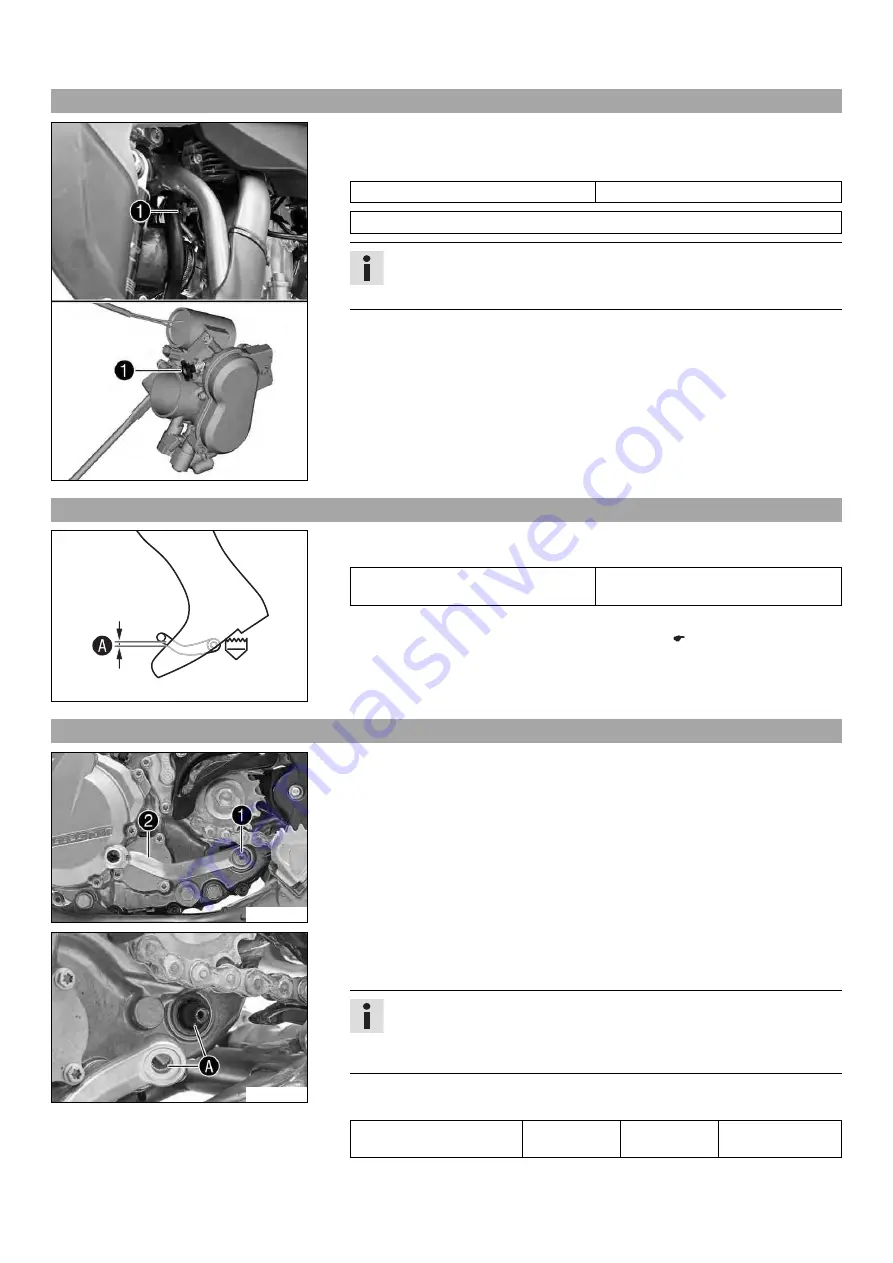
16
TUNING THE ENGINE
72
16.3
Adjusting the idle speed
x
L01268-10
–
Run the engine until warm.
–
Set the desired idle speed by turning the idle speed adjusting screw
1
.
Guideline
Idle speed
2,250… 2,350 rpm
Tachometer (45129075000)
Info
Turn counterclockwise to decrease the idle speed.
Turn clockwise to increase the idle speed.
16.4
Checking the basic position of the shift lever
400692-10
–
Sit on the vehicle in the riding position and determine the distance
A
between the
upper edge of your boot and the shift lever.
Distance between shift lever and upper
edge of boot
10… 20 mm (0.39… 0.79 in)
» If the distance does not meet specifications:
–
Adjust the basic position of the shift lever.
x
16.5
Adjusting the basic position of the shift lever
x
L01309-10
–
Remove screw
1
and take off shift lever
2
.
L01310-10
–
Clean gear teeth
A
of the shift lever and shift shaft.
–
Mount the shift lever on the shift shaft in the required position and engage the
gearing.
Info
The range of adjustment is limited.
The shift lever must not come into contact with any other vehicle compo-
nents during the shift procedure.
–
Mount and tighten the screw.
Guideline
Screw, shift lever
M6
14 Nm
(10.3 lbf ft)
Loctite
®
243™
Summary of Contents for 450 SMR
Page 1: ...OWNER S MANUAL 2014 450 SMR Art no 3213039en ...
Page 2: ......