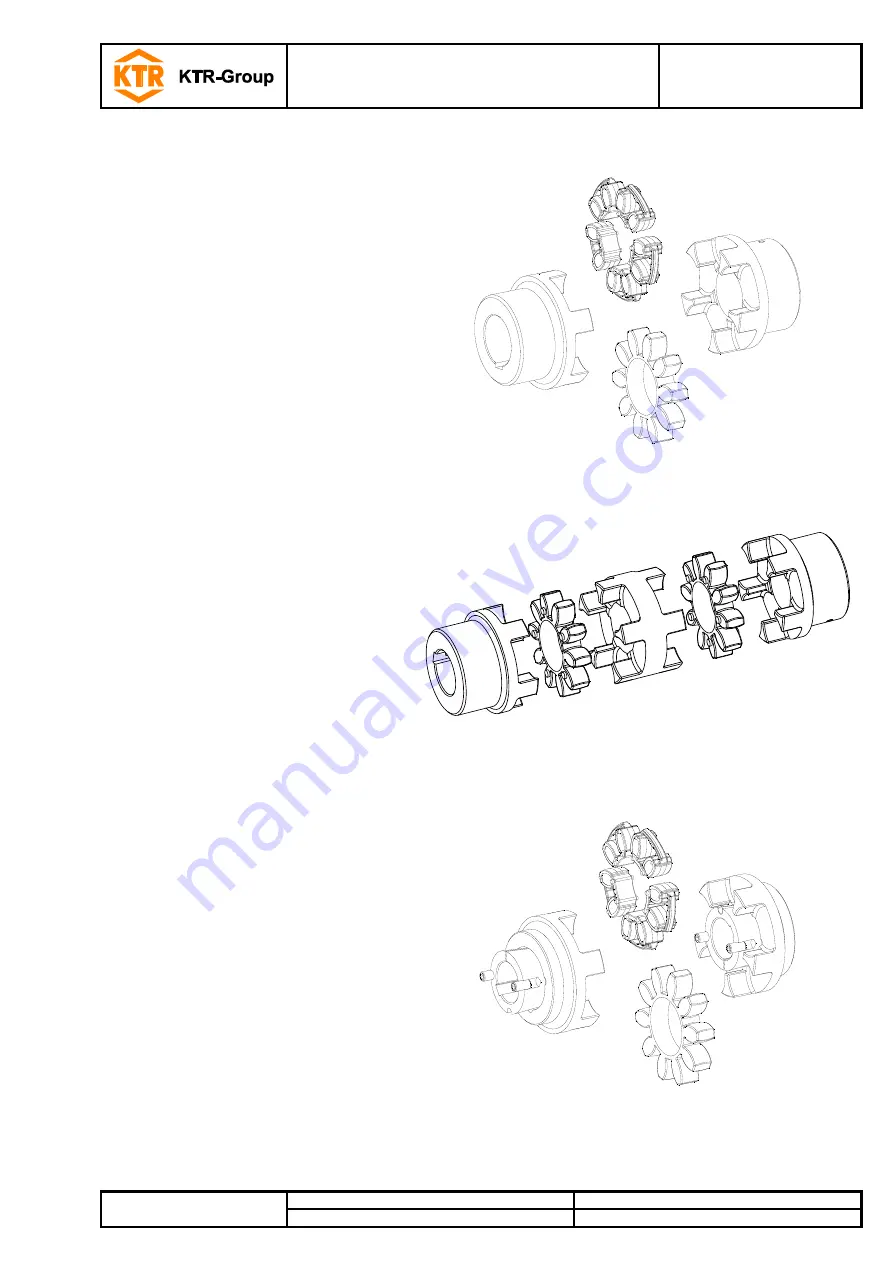
ROTEX
®
Operating/Assembly instructions
KTR-N
Sheet:
Edition:
40210 EN
1 of 22
22
Please observe protection
note ISO 16016.
Drawn:
2017-09-06 Pz/Bru
Replacing:
KTR-N dated 2017-01-02
Verified:
2017-09-06 Pz
Replaced by:
ROTEX
®
Torsionally flexible jaw-type couplings
No. 001
– shaft coupling,
No. 018
– DKM,
with taper clamping sleeve
and their combinations
according to directive 2014/34/EU
for finish bored, pilot bored and
unbored couplings
Type No. 001
– shaft coupling
Type No. 018
– DKM
double-cardanic coupling
Type with taper clamping sleeve