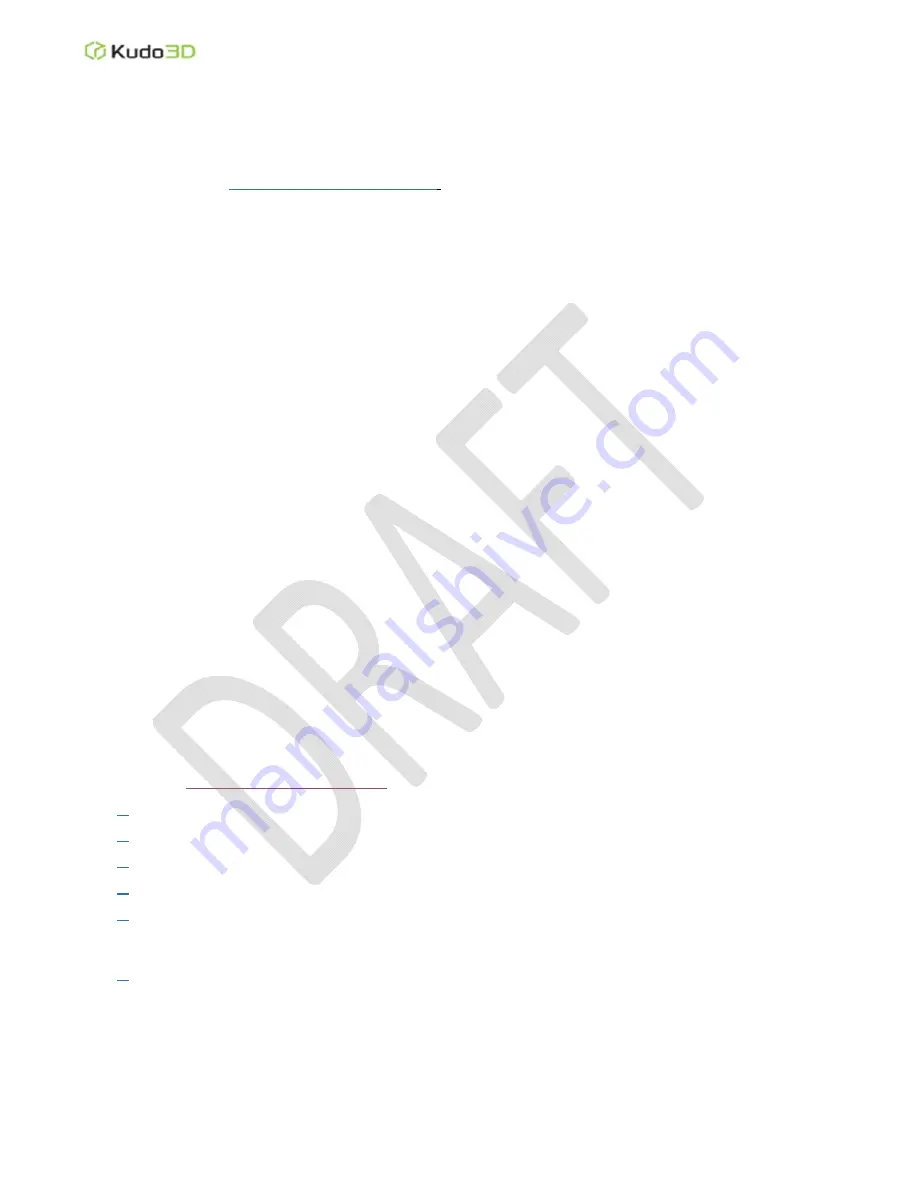
Kudo3D Bean User Manual
Ver. 1.0
8 of 14
VI. Linear Guide Calibration
If the carrier of the linear guide is loose, you would need to calibrate it to improve the surface quality.
Under this situation, you can swing the platform arm horizontally. Please follow the steps below and also
refer to the video
https://youtu.be/bQXxF9VVSp8
.
1. Remove the platform
2. Remove the arm/carrier assembly by rotating the linear screw manually so the assembly comes out from
the top of the linear screw.
3. Remove the anti-wobbling piece with the brass nut inside the arm by loosening the pivoting nut.
4. Loosen those two tiny set screws on the cylinder in the carrier and rotate the center cylinder piece with
those two screws. Rotate the cylinder to a position that the carrier is tight but not too tight. The carrier
must be tight enough so there is no horizontal swinging of the platform arm. The carrier cannot be too
tight so weight of the platform can pull the platform down. Tighten the set screws. This is a try-an-error
process. We spent quite a lot of time to calibrate the carrier.
5. Put only the arm back in the linear guide, it may or may not slide down. But when you lock the platform
on the arm, it has to move down freely by the gravity. There should be no horizontal movement at all.
6. If carrier is too tight or too loose, repeat step 4 and 5 until you find the proper tightness.
7. Put the anti-wobbling piece back. Adjust the nut so that the anti-wobbling piece can move freely and the
gap between the anti-wobbling piece and the holding arm is minimum. This is also very important to
minimize the horizontal movement of the arm. If the nut is too tight, the anti-wobbling piece is locked. If
the nut is too loose, there is a big gap between the anti-wobbling piece and the arm and may cause z
zero problem.
8.
Put the arm/carrier assembly back by rotating the linear screw below manually. You would need to align
the brass nut to the linear screw and press the arm downward with one hand while rotating the linear
screw with another hand.
VII. Teflon Film Replacement
Your printer comes with 12 screws and 12 tubes to help you replace the film. Please refer to the video for
the steps.
https://youtu.be/9OxvdgD-b0A
1. Place the Teflon film between the container and the securing ring
2. Insert 12 studs
3. Insert the 12 screws M3 x 8 and screw down one to two rotations
4. Press the securing ring into the trench
5. Follow the video and replace 12 tubes with 12 M3 x 6 screws. Make sure they pass through the holes of
the film and screw down only one to two rotation. You need to do two screws in the opposite position
at a time to maintain the balance. Do not run it randomly.
6.
Replace the 12 M3 x 8 screws with 12 M3 x 6 screws.
To save time, you need only 12 screws to secure the film. We leave a big design safety margin
because we can’t increase the number of screws after injection mold is made.
We are still investigating the impact of the film tightness on the print and vat sealing. If there is not
much difference, we will stretch the film less to simplify the film replacement process later.