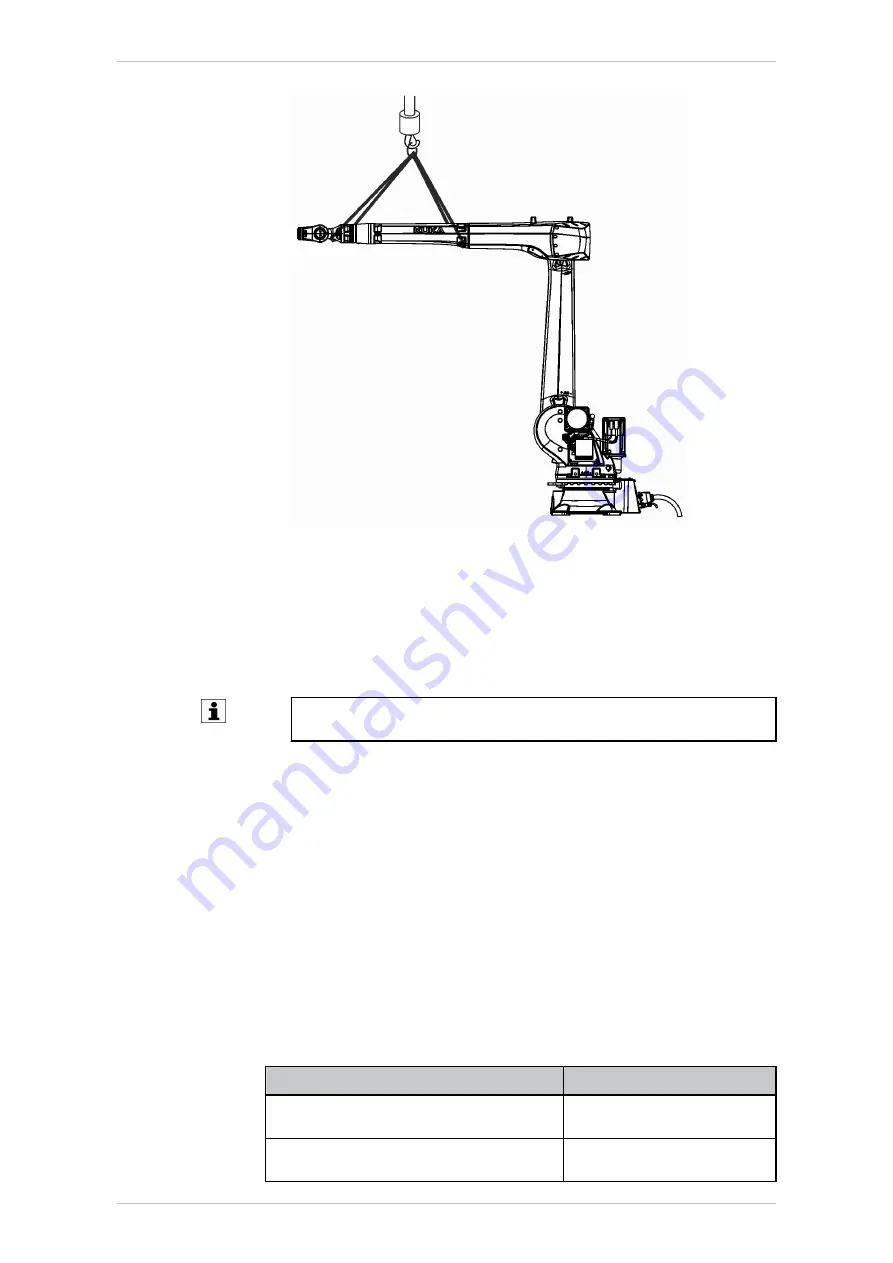
Fig. 9-25: Securing robot arm
9.5.1.7
Concluding work
The following concluding work must be carried out:
• Move A4, A5 and A6 of the robot and look out for irregularities.
• Carry out mastering of A4, A5 and A6.
Detailed information about mastering is contained in the operating
and programming instructions for end users or system integrators.
• Test the program in Manual Reduced Velocity mode (T1).
9.5.2
Exchanging motor A5
Description
The following instructions describe the exchange of the motor. This de-
scription applies to floor-mounted robots. If the robot is installed in an in-
clined or suspended position, the procedure is to be applied analogously.
During removal of the motor, the robot can independently move about this
axis. Mechanical auxiliary equipment (e.g. support, crane) or a stable end
position (e.g. buffer) can be used to secure against motions.
Equipment
The following equipment is required:
Designation
Article number
Lifting tackle / rope sling with sufficient
load-bearing capacity
-
Crane with sufficient load-bearing capaci-
ty
-
KR IONTEC
264/344 |
www.kuka.com
MA KR IONTEC V4 | Issued: 11.05.2021
Repair
Summary of Contents for IONTEC KR 20 R3100
Page 14: ...KR IONTEC 14 344 www kuka com MA KR IONTEC V4 Issued 11 05 2021 Introduction...
Page 166: ...KR IONTEC 166 344 www kuka com MA KR IONTEC V4 Issued 11 05 2021 Planning...
Page 188: ...KR IONTEC 188 344 www kuka com MA KR IONTEC V4 Issued 11 05 2021 Start up and recommissioning...
Page 310: ...KR IONTEC 310 344 www kuka com MA KR IONTEC V4 Issued 11 05 2021 Repair...
Page 340: ...KR IONTEC 340 344 www kuka com MA KR IONTEC V4 Issued 11 05 2021 KUKA Service...