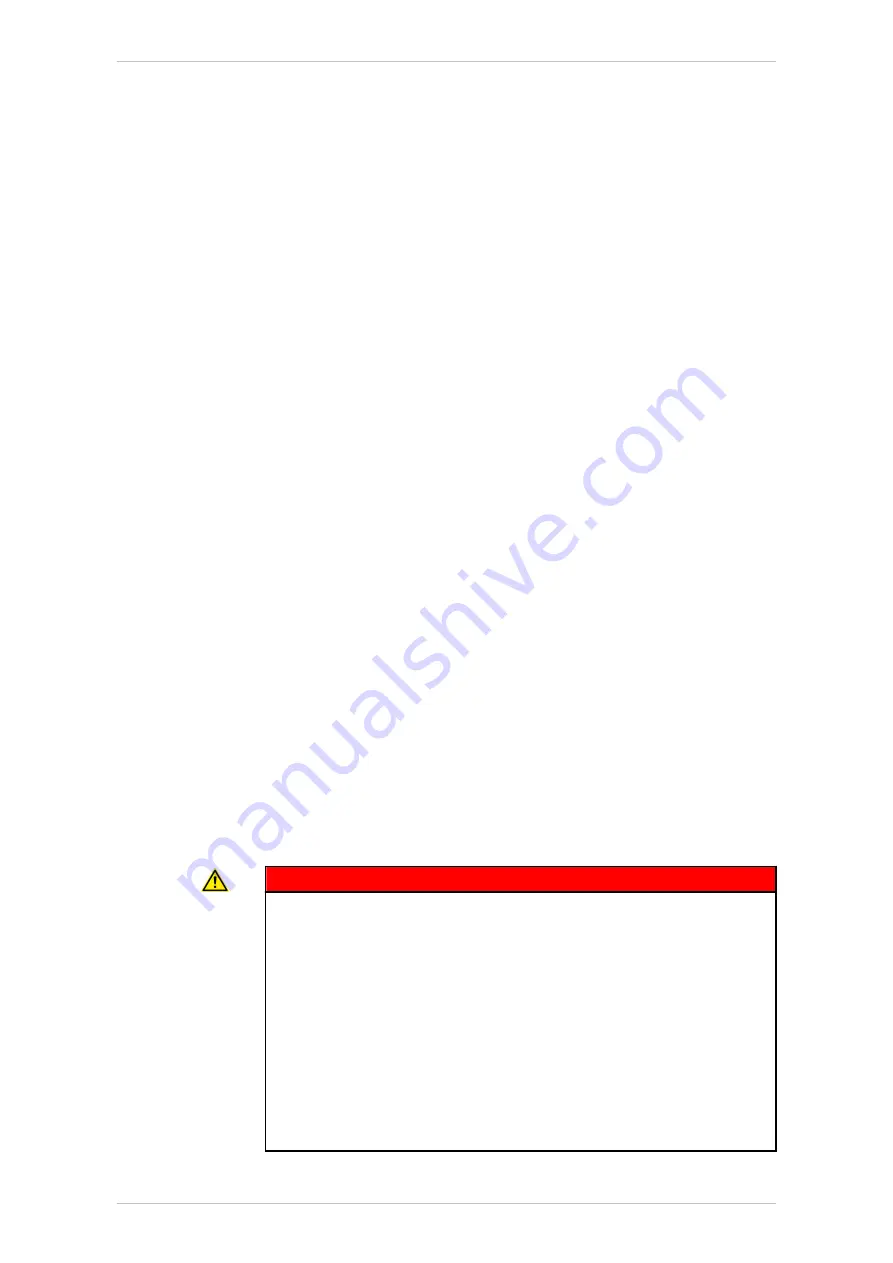
3.5.5
Automatic mode
Automatic mode is only permissible in compliance with the following safety
measures:
• All safety equipment and safeguards are present and operational.
• There are no persons in the system.
• The defined working procedures are adhered to.
If the manipulator or an external axis (optional) comes to a standstill for
no apparent reason, the danger zone must not be entered until an EMER-
GENCY STOP has been triggered.
3.5.6
Maintenance and repair
After maintenance and repair work, checks must be carried out to ensure
the required safety level. The valid national or regional work safety regula-
tions must be observed for this check. The correct functioning of all safety
functions must also be tested.
The purpose of maintenance and repair work is to ensure that the system
is kept operational or, in the event of a fault, to return the system to an
operational state. Repair work includes troubleshooting in addition to the
actual repair itself.
The following safety measures must be carried out when working on the
industrial robot:
• Carry out work outside the danger zone. If work inside the danger
zone is necessary, the user must define additional safety measures to
ensure the safe protection of personnel.
• Switch off the industrial robot and secure it (e.g. with a padlock) to
prevent it from being switched on again. If it is necessary to carry out
work with the robot controller switched on, the user must define addi-
tional safety measures to ensure the safe protection of personnel.
• If it is necessary to carry out work with the robot controller switched
on, this may only be done in operating mode T1.
• Label the system with a sign indicating that work is in progress. This
sign must remain in place, even during temporary interruptions to the
work.
• The EMERGENCY STOP devices must remain active. If safety func-
tions or safeguards are deactivated during maintenance or repair work,
they must be reactivated immediately after the work is completed.
DANGER
Danger to life and limb due to live parts
The robot system must be disconnected from the mains power supply
prior to work on live parts. It is not sufficient to trigger an EMERGENCY
STOP or safety stop, because parts remain live. Death or severe inju-
ries may result.
• Before commencing work on live parts, turn off the main switch and
secure it against being switched on again.
If the controller variant in question does not have a main switch
(e.g. KR C5 micro), turn off the device switch then disconnect the
power cable and secure it so it cannot be reconnected.
• Then check to ensure that the system is deenergized.
• Inform the individuals involved that the robot controller is switched
off. (e.g. by affixing a warning sign)
KR IONTEC
30/344 |
www.kuka.com
MA KR IONTEC V4 | Issued: 11.05.2021
Safety
Summary of Contents for IONTEC KR 20 R3100
Page 14: ...KR IONTEC 14 344 www kuka com MA KR IONTEC V4 Issued 11 05 2021 Introduction...
Page 166: ...KR IONTEC 166 344 www kuka com MA KR IONTEC V4 Issued 11 05 2021 Planning...
Page 188: ...KR IONTEC 188 344 www kuka com MA KR IONTEC V4 Issued 11 05 2021 Start up and recommissioning...
Page 310: ...KR IONTEC 310 344 www kuka com MA KR IONTEC V4 Issued 11 05 2021 Repair...
Page 340: ...KR IONTEC 340 344 www kuka com MA KR IONTEC V4 Issued 11 05 2021 KUKA Service...