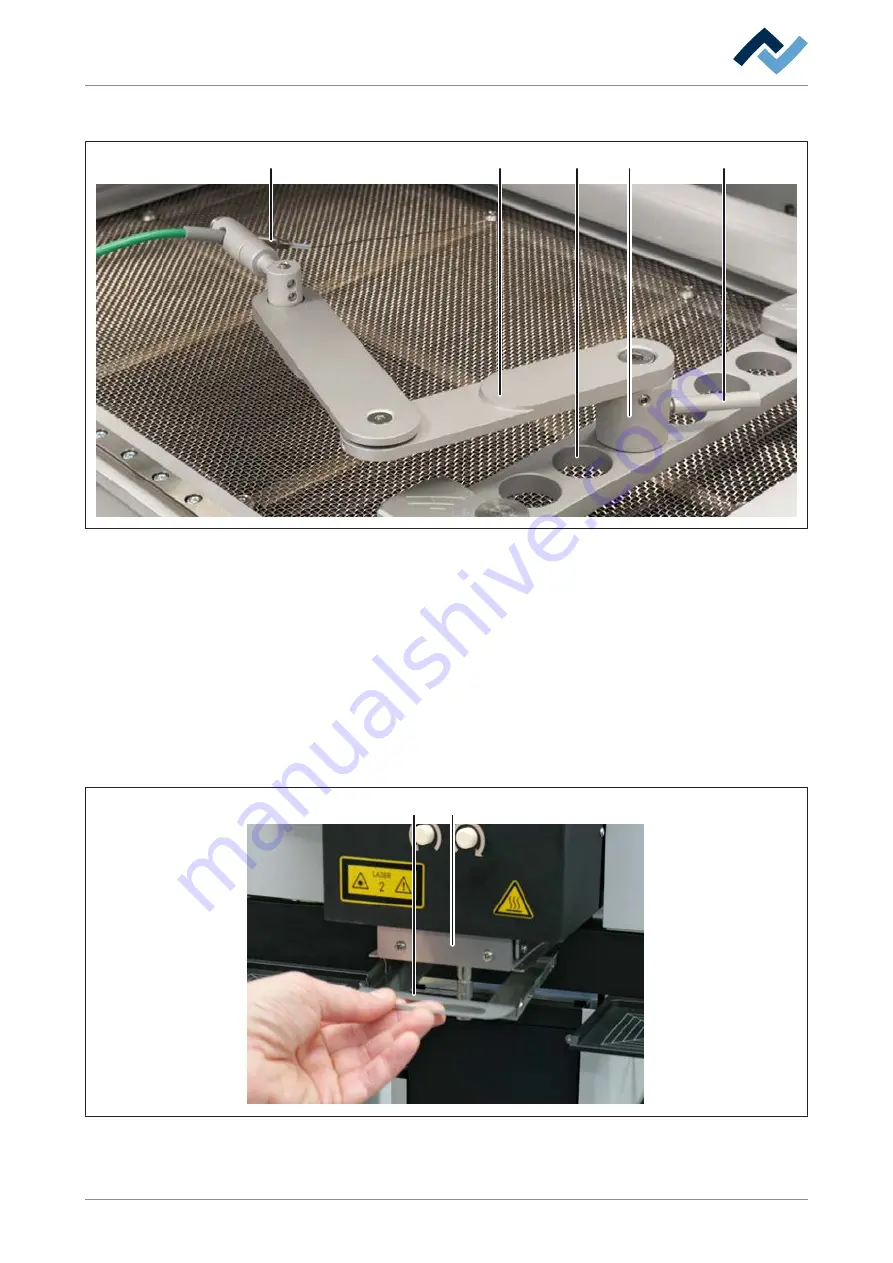
4 | Transport, installation, storage, disposal
Assembling an Accu-TC holder and an air baffle
4.12 Assembling an Accu-TC holder and an air baffle
2
5
1
3
4
Fig. 13:
AccuTC mount
ü
To assemble an Accu-TC holder:
a) You can fit the holder into any of the four bores (4) in the PCB holder. To do so,
insert the cylinder (5) into a bore and tighten with the lever (2).
b) Connect the AccuTC thermocouple without fixture (item 0IR6500-37) (3) to the
socket [TC1].
c) Mount the thermocouple (3) as shown.
Depending on their opening size, air baffles can reduce the heated surface as well
as the thermal load around the soldering area.
To avoid material damage when installing air baffles, make sure that the air baffle
does not touch the pipette and the soldering nozzle.
2
1
a) Select an air baffle.
Ersa GmbH
Operating instructions HR 550 XL EN 3BA00247-01 | Rev. 1
46 / 157