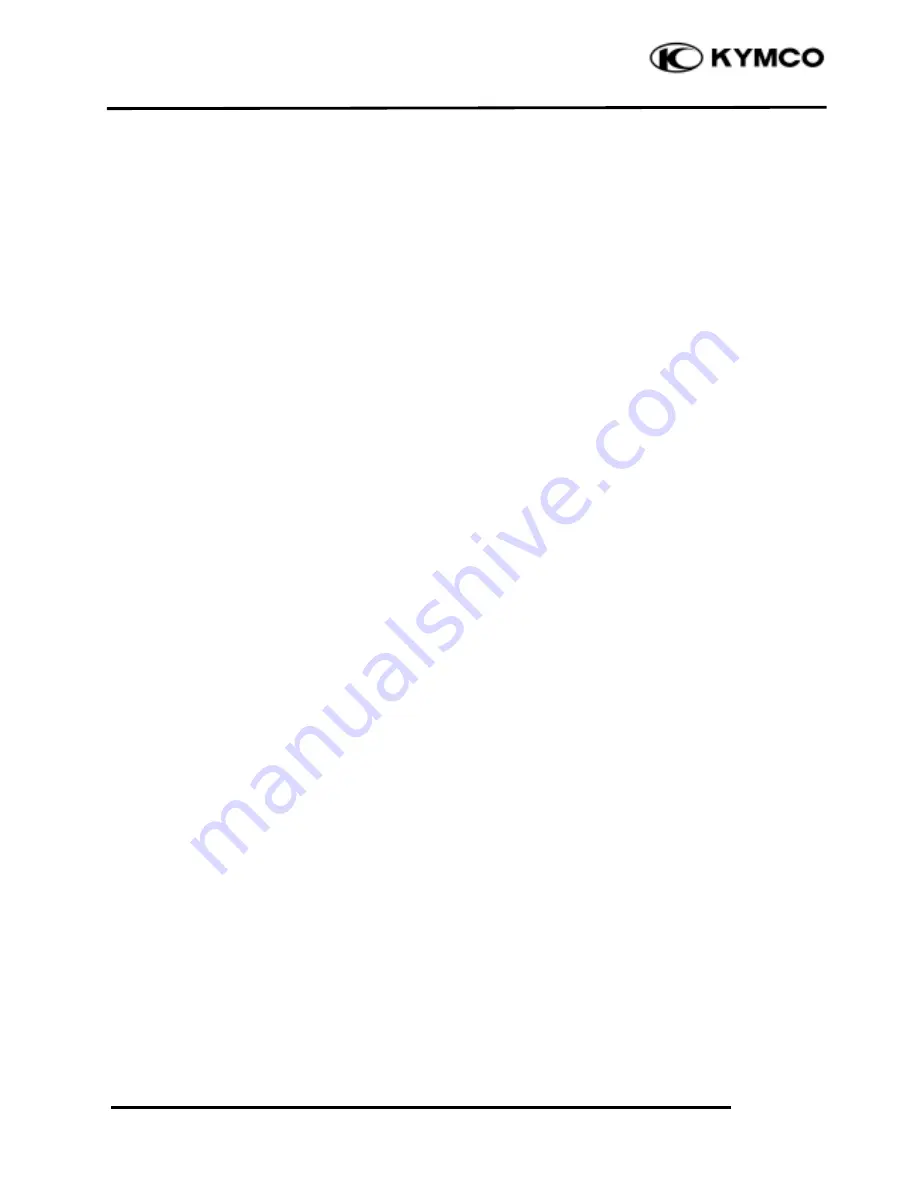
19
. SWITCHES/HORN/FUEL UNIT/THERMOSTATIC SWITCH
/TEMPERATURE GAUGE/INSTRUMENTS/LIGHTS
19-2
PEOPLE 250
SERVICE INFORMATION
GENERAL INSTRUCTIONS
•
After installation of each switch, a continuity check must be performed. A continuity check can
usually be made without removing the part from the motorcycle.
TESTING INSTRUMENT
Electric tester
TROUBLESHOOTING
Lights do not come on when ignition
Temperature gauge does not register
switch is “ON”
correctly
•
Burned bulb
•
Faulty temperature gauge
•
Faulty switch
•
Faulty thermosensor
•
Poorly connected, broken or shorted wire
•
Broken or shorted wire between
temperature gauge and thermosensor
Fuel gauge pointer does not move or
register correctly
•
Faulty fuel gauge
•
Faulty fuel unit
•
Poorly connected wire between fuel
gauge and fuel unit
•
Fuse burned out
SPECIFICATIONS
Fuse
10A,15A,30A
Headlight bulb
12V 35W/35W
Turn signal light bulb
12V 10W
Stoplight/taillight
12V 21/5W
License plate light
12V 5W
Position light
12V 5W
Turn signal indicator light
12V 3W
Summary of Contents for People S 250
Page 21: ...1 GENERAL INFORMATION 1 18 PEOPLE 250 WIRING DIAGRAM ...
Page 34: ...2 EXHAUST MUFFLER FRAME COVERS 2 1 PEOPLE 250 SCHEMATIC DRAWING ...
Page 71: ...6 CYLINDER HEAD VALVES 6 1 PEOPLE 250 SCHEMATIC DRAWING ...
Page 83: ...7 CYLINDER PISTON 7 1 PEOPLE 250 SCHEMATIC DRAWING ...
Page 92: ...8 DRIVE AND DRIVEN PULLEYS V BELT 8 1 PEOPLE 250 SCHEMATIC DRAWING ...
Page 106: ...8 DRIVE AND DRIVEN PULLEYS V BELT 8 15 PEOPLE 250 Install the left crankcase cover 8 3 ...
Page 108: ...9 FINAL REDUCTION 9 1 PEOPLE 250 SCHEMATIC DRAWING ...
Page 117: ...10 A C GENERATOR STARTER CLUTCH 10 1 PEOPLE 250 SCHEMATIC DRAWING ...
Page 127: ...11 CRANKCASE CRANKSHAFT 11 1 PEOPLE 250 SCHEMATIC DRAWING ...
Page 134: ...12 COOLING SYSTEM 12 1 PEOPLE 250 SCHEMATIC DRAWING ...
Page 151: ...13 FUEL SYSTEM CARBURETOR FUEL PUMP FUEL TANK 13 1 PEOPLE 250 FUEL SYSTEM ...
Page 152: ...13 FUEL SYSTEM CARBURETOR FUEL PUMP FUEL TANK 13 2 PEOPLE 250 SCHEMATIC DRAWING ...
Page 191: ...15 REAR BRAKE REAR FORK REAR WHEEL REAR SHOCK ABSORBER 15 1 PEOPLE 250 SCHEMATIC DRAWING ...