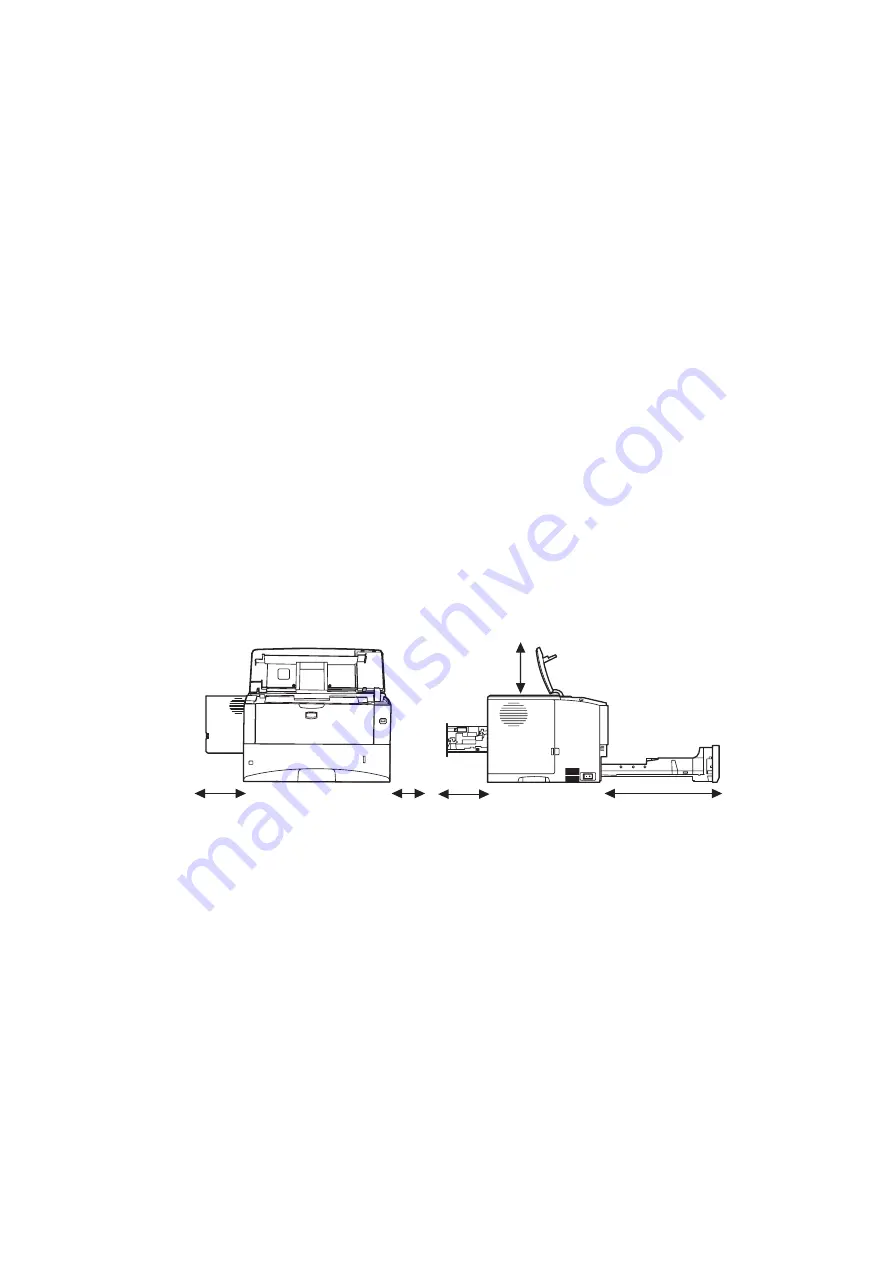
2J5
1-2-1
1-2 Installation
1-2-1 Drum unit
Note the following when handling or storing the drum (drum unit).
Note the following when handling or storing the drum unit.
1. When removing the drum unit, never expose the drum surface to strong direct light.
2. Avoid abrupt changes in temperature and humidity.
3. Avoid exposure to any substance which is harmful to or may affect the quality of the drum.
4. Do not touch the drum surface with any object. Should it be touched by hands or stained with oil, clean it.
1-2-2 Developer unit and toner container
Store the toner container in a cool, dark place.
Avoid direct light and high humidity.
1-2-3 Installation environment
1. Temperature: 10 to 32.5
°
C/50 to 90.5
°
F
2. Humidity: 15 - 80%RH
3. Power supply: 220 - 240 V AC, 5.0 A (Average)
4. Power source frequency: 50 Hz
±
0.3%/60 Hz
±
0.3%
5. Installation location
Avoid direct sunlight or bright lighting. Ensure that the photoconductor will not be exposed to direct sunlight or
other strong light when removing paper jams.
Avoid extremes of temperature and humidity, abrupt ambient temperature changes, and hot or cold air directed
onto the machine.
Avoid dust and vibration.
Choose a surface capable of supporting the weight of the machine.
Place the machine on a level surface (maximum allowance inclination: 1
°
).
Avoid air-borne substances that may adversely affect the machine or degrade the photoconductor, such as mer-
cury, acidic of alkaline vapors, inorganic gasses, NOx, SOx gases and chlorine-based organic solvents.
Select a room with good ventilation.
6. Allow sufficient access for proper operation and maintenance of the machine.
Figure 1-2-1
Left: 300 mm
(11
13/16
")
Top: 300 mm
(11
13/16
")
Right: 100 mm
(3
15/16
")
Rear: 200 mm
(7
7/8
")
400 mm (15
3/4
" )
when the optional
face up tray (PT-430)
is attached.
Front: 600 mm
(23
5/8
")
Summary of Contents for Ecosys FS-6970DN
Page 1: ...SERVICE MANUAL Published in March 2009 842J5110 2J5SM060 First Edition FS 6970DN...
Page 3: ...Revision history Revision Date Replaced pages Remarks...
Page 4: ...This page is intentionally left blank...
Page 10: ...This page is intentionally left blank...
Page 18: ...2J5 1 1 6 This page is intentionally left blank...
Page 24: ...2J5 1 2 6 This page is intentionally left blank...
Page 40: ...2J5 1 3 16 This page is intentionally left blank...
Page 120: ...2J5 2 3 8 This page is intentionally left blank...
Page 124: ...2J5 2 4 4 This page is intentionally left blank...
Page 125: ......
Page 126: ......