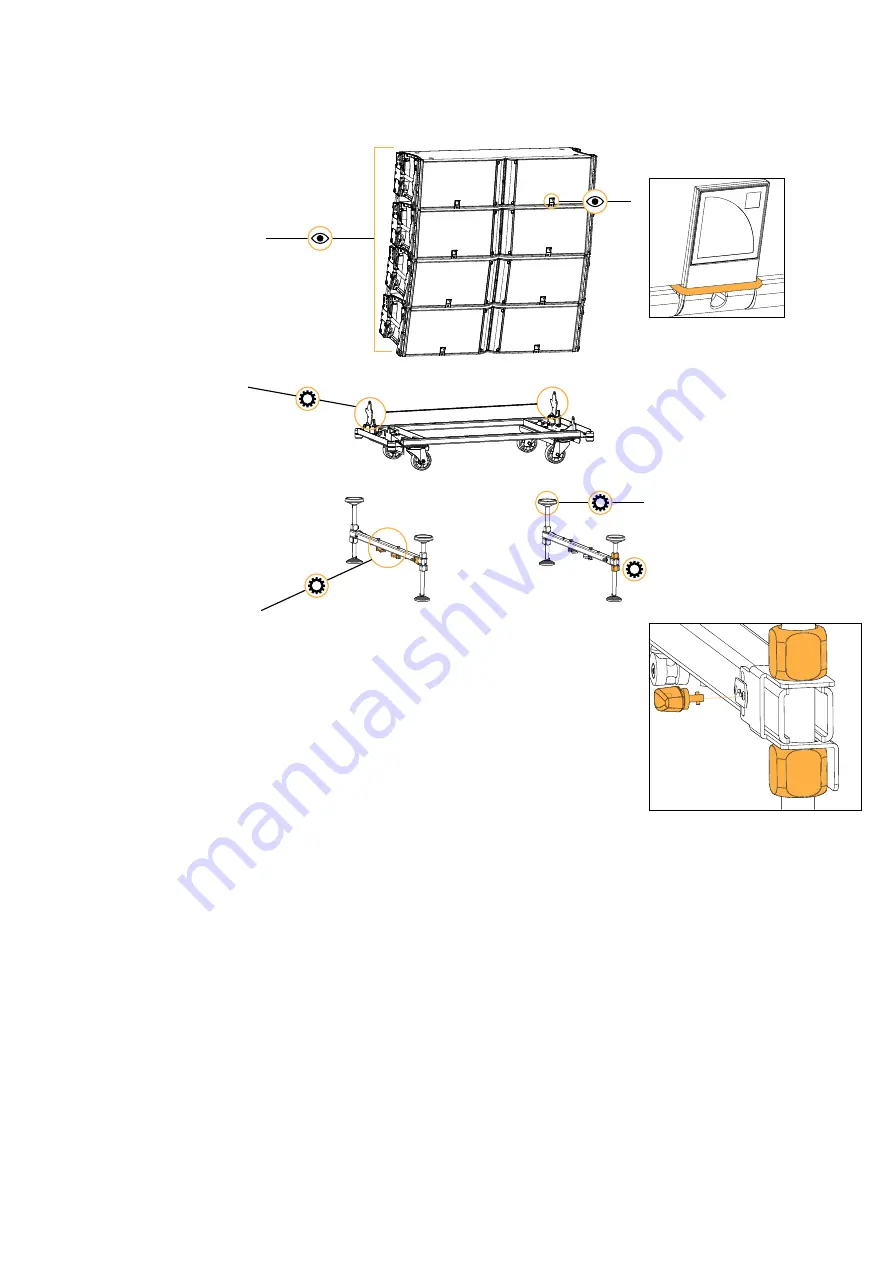
Inspection and preventive maintenance
K2 array with K2-CHARIOT and K2-JACK
(p.49).
(p.49)
(p.54)
(p.53)
rear rigging arms rotate
correctly
the locking handles can be
tightened and loosened by
hand
turn the hand wheels:
the central part is raised
(clockwise) or lowered
(counter-clockwise)
check the integrity of the
quarter-turn locking system
46
K2 owner's manual (EN) version 1.1
Summary of Contents for K2
Page 1: ...K2 owner s manual EN ...
Page 82: ...Rigging procedures 5 Pin the arms 82 K2 owner s manual EN version 1 1 ...
Page 142: ...Corrective maintenance 3 Remove the HF driver assembly 142 K2 owner s manual EN version 1 1 ...
Page 147: ...Corrective maintenance K2 owner s manual EN version 1 1 147 ...
Page 182: ...Pickup points guidelines 182 K2 owner s manual EN version 1 1 ...