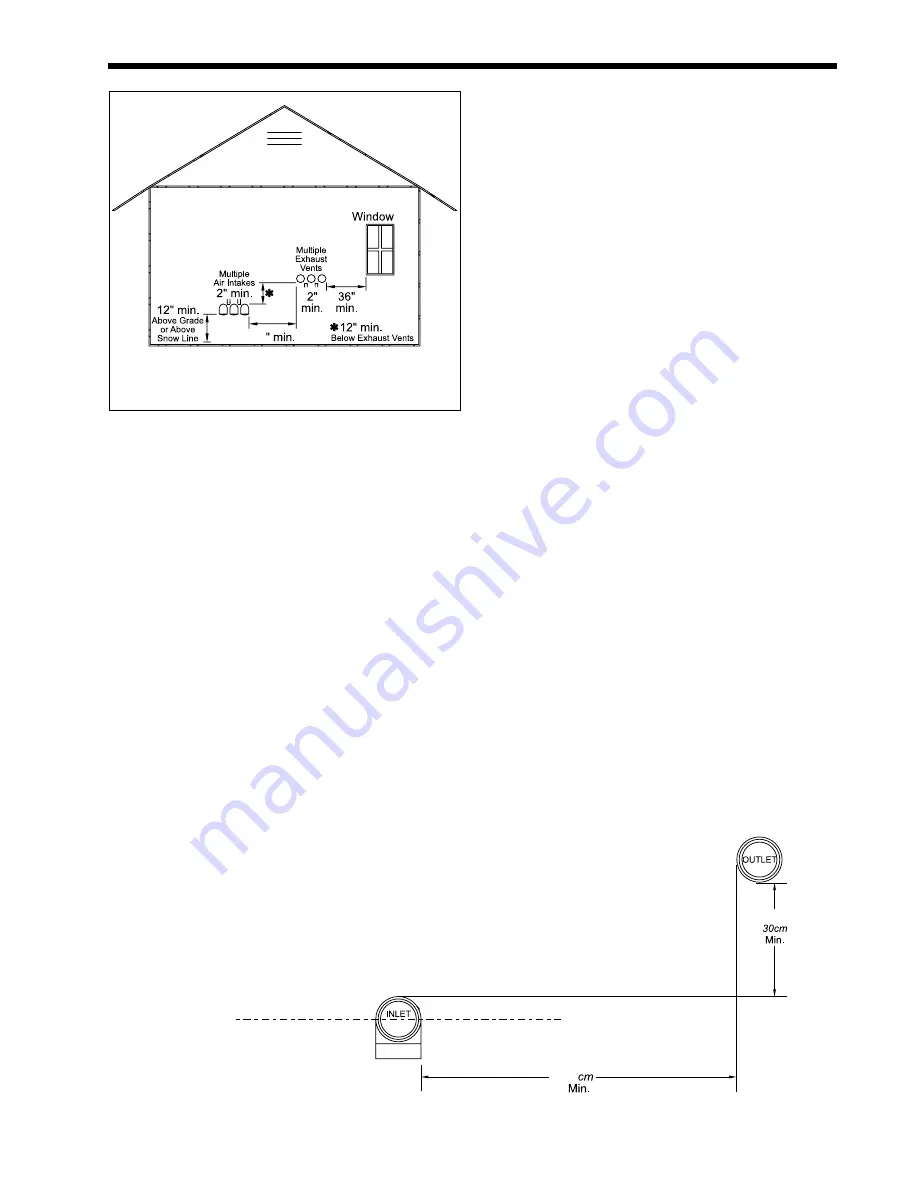
MagnaTherm Boilers and Water Heaters
Page 13
objects.
7. if the boiler or water heater uses ducted
combustion air from an intake terminal located
on the same wall, see See Figure 5 and Figure 4
for proper spacing and orientation.
in the U.S., if the vent termination is located in an
area exposed to high winds, an cPVc tee (the same
diameter as the vent pipe) may be used. The tee’d
vent termination offers greater protection from wind
related operating issues.
3.3.2 Side Wall Combustion air terminal
consider the following when installing the terminal.
1. Do not locate the air inlet terminal near a
source of corrosive chemical fumes (e.g.,
cleaning fluid, chlorine compounds, etc.).
2. Locate the terminal so that it will not be subject
to damage by accident or vandalism. it must be
at least 7 feet ( 2.1 m) above a public walkway.
3. Locate the combustion air terminal so that it
cannot be blocked by snow. The national Fuel
Gas code requires that it be at least 12 inches
(30 cm) above grade, but the installer may
determine it should be higher, depending upon
local conditions.
4. if the MagnaTherm is side-wall vented to the
same wall, use Figure 4 to determine the proper
mounting locations.
5. Multiple vent kits should be installed such that
the horizontal distance between outlet group
and inlet group is 84” (213 cm). (See Figure 5)
6. The vent outlet must be at least 12” above the top
of the air inlet, and must be at least 84” (213 cm)
horizontally from the air inlet. (See Figure 5).
84”
213
12”
figure 4. minimum Venting Distance
IMPORTANT: All terminals must be placed so that they remain at least 12”
above the expected snow line. Local codes may have more specific
requirements, and must be consulted. Refer to the NFPA54 National Fuel Gas
Code and your local codes for all required clearances for venting.
84
figure 5. multiple Side-Wall terminals, air and
Vent
1. Figure 4 shows the requirements for
mechanical vent terminal clearances for the
U.S. and canada.
2. Vent terminals for condensing appliances or
appliances with condensing vents are
not
permitted to terminate above a public walkway,
or over an area where condensate or vapor
could create a nuisance or hazard.
3. Locate the vent terminal so that vent gases
cannot be drawn into air conditioning system
inlets.
4. Locate the vent terminal so that vent gases
cannot enter the building through doors,
windows, gravity inlets or other openings.
whenever possible, avoid locations under
windows or near doors.
5.
Locate the vent terminal so that it cannot
be blocked by snow. The installer may
determine that a vent terminal must be
higher than the minimum shown in codes,
depending upon local conditions.
6. Locate the terminal so the vent exhaust does
not settle on building surfaces or other nearby
objects. Vent products may damage surfaces or