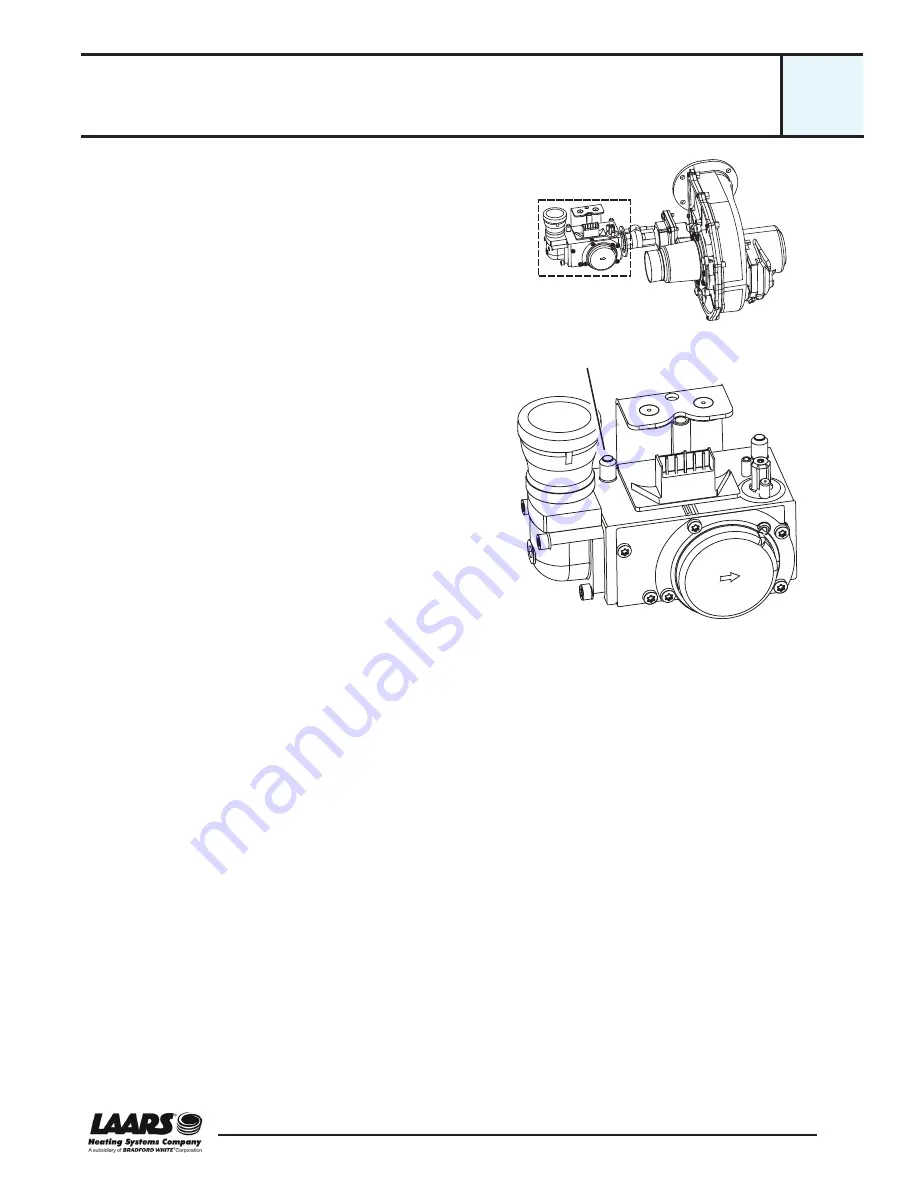
31
Service Manual - NeoTherm 500
Testing the Low Gas Pressure Switch
B14
In the gas train, this switch is located before the gas
control valve. Gas will reach this switch whenever the
gas shutoff valve to the unit is open.
Figure B14-1 shows the gas train. Connect a test gauge
to the inlet gas pressure tap.
The low pressure switch (Honeywell p/n C6097A) is
wired N.O. (normally open), and requires a manual re-
set. (You will need to reset this switch if you disconnect
an old switch or install a new switch.) The low pressure
switch is set to trip below 3” W.C. (water column).
Fig. B14-1 - Inlet gas pressure tap
Inlet gas
pressure
tap
Summary of Contents for NeoThem NTH
Page 2: ......
Page 10: ...Service Manual NeoTherm 500 viii ...
Page 68: ...58 Service Manual NeoTherm 500 ...
Page 115: ...105 Service Manual NeoTherm 500 Appendix 3 Wiring Diagram App3 ...
Page 116: ...106 Service Manual NeoTherm 500 ...
Page 117: ......