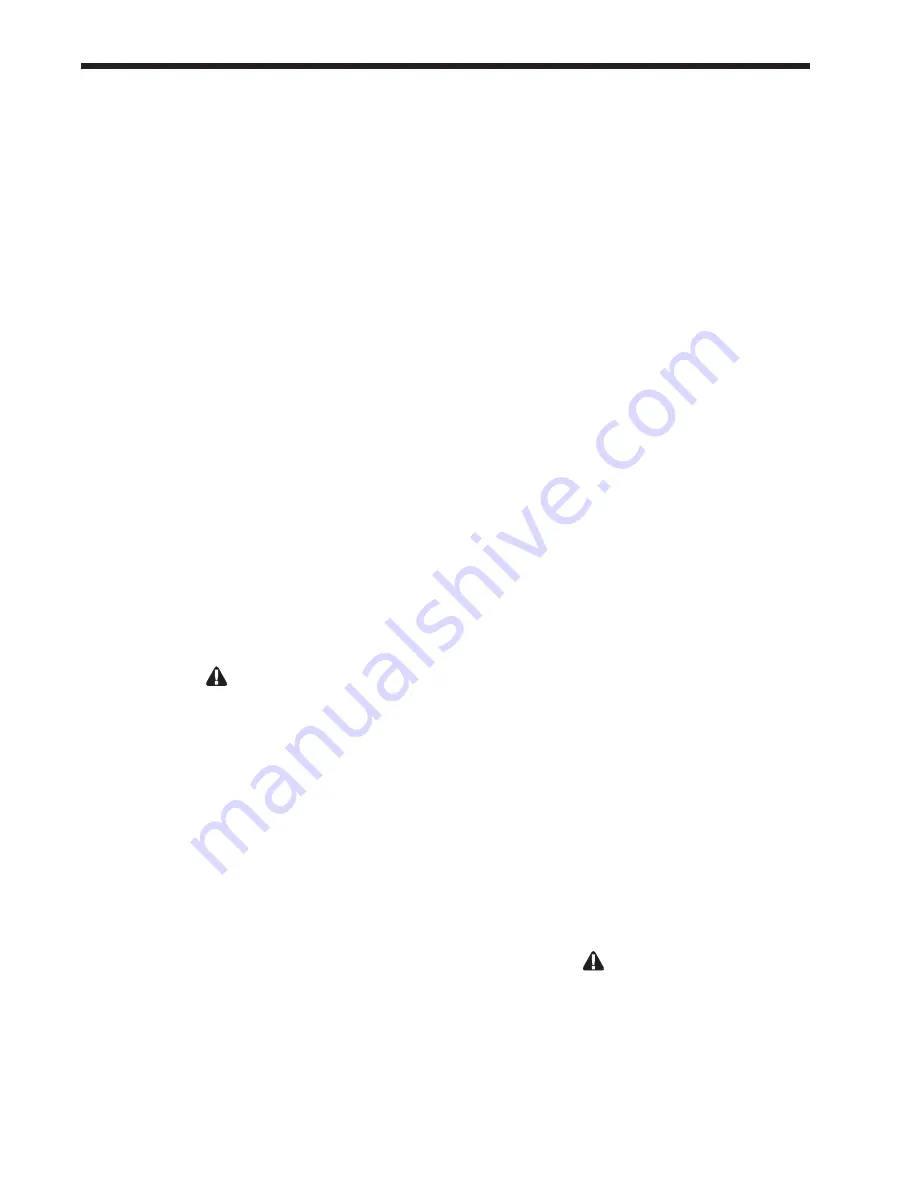
LAARS Heating Systems
Page 92
11. Shut down the entire system and vent all
radiation units and high points in the system
piping, as described in Step 4.
12. Close the make-up water valve. Check the
strainer in the pressure reducing valve for
sediment or debris from the make-up water
line. Reopen the make-up water valve.
13. Check the gauge for correct water pressure, and
also check the water level in the system. If the
height indicated above the boiler ensures that
water is at the highest point in the circulating
loop, then the system is ready for operation.
14. Refer to local codes and the make-up water
valve manufacturer’s instructions as to whether
the make-up water valve should be left open or
closed.
15. After placing the unit in operation, the ignition
system safety shutoff device must be tested.
First, shut off the manual gas valve, and call the
unit for heat. The main gas terminals will be
energized, attempting to light, for four seconds,
and then will de-energize. The unit will go into
lockout after the required number of trial for
ignition periods.
Second, turn the power off, press the manual
reset button on the boiler control, or the user
display, open the manual gas valve and allow
the unit to light. While the unit is operating,
close the manual gas valve and ensure that
power to the main gas valve has been cut.
16. Within three days of start-up, recheck all air
bleeders and the expansion tank as described in
Steps 4 and 8 above.
note -
The installer is responsible for identifying to
the owner/operator the location of all emergency
shutoff devices.
WarnInG
Do not use this appliance if any part has been
under water. Immediately call a qualified service
technician to inspect the appliance and to replace
any part of the control system and any gas control
that may have been under water.
Section 10
oPeratInG InStrUCtIonS
10.1 filling the Boiler System
1. Ensure the system is fully connected. Close all
bleeding devices and open the make-up water
valve. Allow the system to fill slowly.
2. If a make-up water pump is employed, adjust
the pressure switch on pumping system to
provide a minimum of 12 psi (81.8 kPa) at the
highest point in the heating loop.
3. If a water pressure regulator is provided on
the make-up water line, adjust the pressure
regulator to provide at least 12 psi (81.8 kPa) at
the highest point in the heating loop.
4. Open any bleeding devices on all radiation
units at the high points in the piping throughout
the system, unless automatic air bleeders are
provided at those points.
note
- There is an air bleed located on the right side
of the NeoTherm unit, on top of the water manifold.
5. To remove all air from the heat exchanger,
cycle the boiler pump on and off 10 times, 10
seconds on and 10 seconds off. Then run the
System and Boiler pumps for a minimum of 30
minutes with the gas shut off.
WarnInG
Failure to remove all air from the heat exchanger
could lead to property damage, severe injury or
death.
6. Open all strainers in the circulating system,
check the operation of the flow switch (if
equipped), and check for debris. If debris is
present, clean out the strainers to ensure proper
circulation.
7. Recheck all air bleeders as described in Step 4.
8. Check the liquid level in the expansion tank.
With the system full of water and under normal
operating pressure, the level of water in the
expansion tank should not exceed ¼ of the
total, with the balance filled with air.
9. Start up the boiler following the procedure
in this manual. Operate the entire system,
including the pump, boiler, and radiation units
for one hour.
10. Recheck the water level in the expansion tank.
If the water level exceeds ¼ of the volume of
the expansion tank, open the tank drain, and
drain to that level.
Summary of Contents for NTV1000
Page 2: ......
Page 35: ...NeoTherm Boilers and Water Heaters Page 31 Fig 20 Ladder Diagram...
Page 36: ...LAARS Heating Systems Page 32 Fig 21 Wiring Diagram...
Page 37: ...NeoTherm Boilers and Water Heaters Page 33...
Page 51: ...NeoTherm Boilers and Water Heaters Page 47 Fig 52 Connection Terminals...
Page 130: ...LAARS Heating Systems Page 126 Fig 140 Machine Frame and Rear Panel 13 3 PARTS ILLUSTRATIONS...
Page 131: ...NeoTherm Boilers and Water Heaters Page 127 Fig 141 Front Panel and Covers...
Page 132: ...LAARS Heating Systems Page 128 Fig 142 Burners and Combustion Chambers...
Page 134: ...LAARS Heating Systems Page 130 Fig 145 Electronic Components...
Page 135: ...NeoTherm Boilers and Water Heaters Page 131 Fig 146 Condensate Trap Fig 147 Control Bezel...
Page 136: ...LAARS Heating Systems Page 132 Fig 148 Flow Switch...
Page 137: ...NeoTherm Boilers and Water Heaters Page 133 This page intentionally left blank...