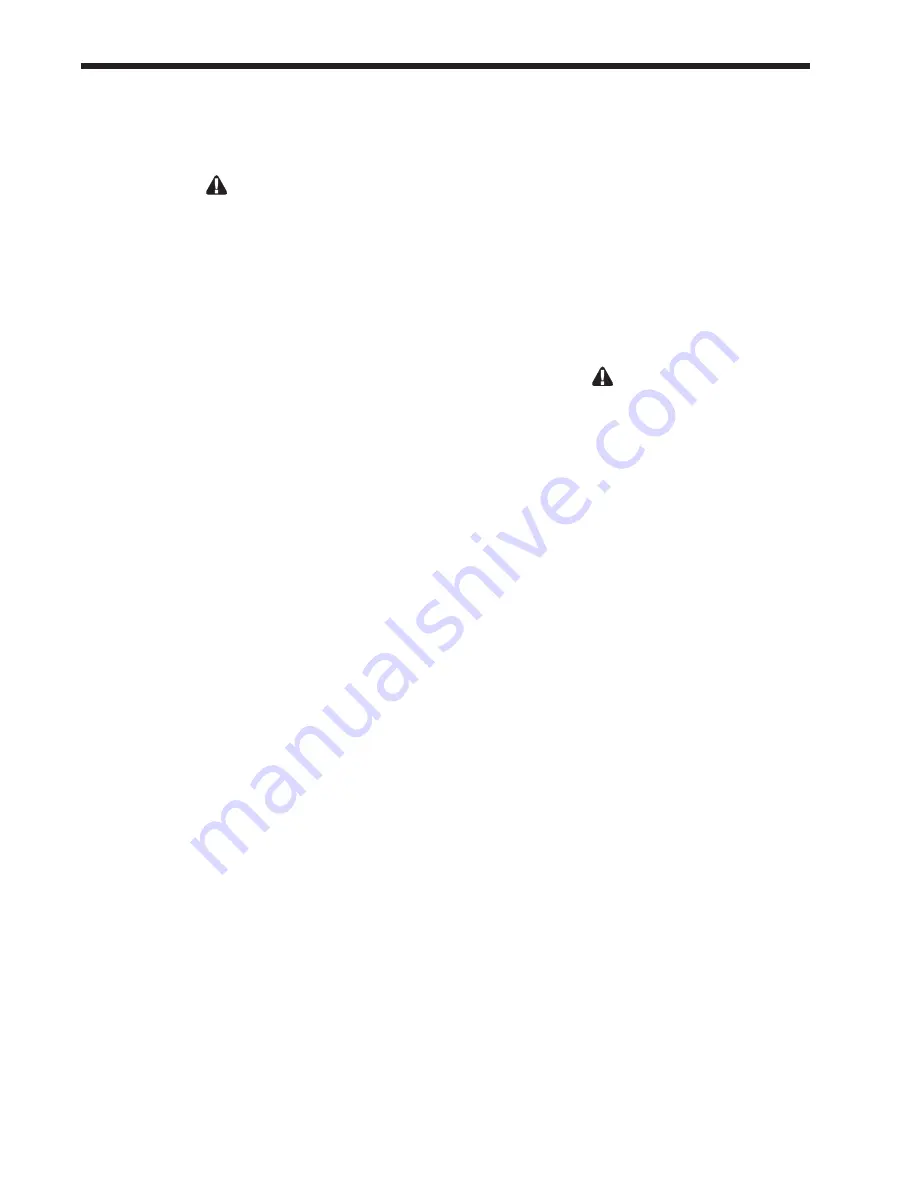
LAARS Heating Systems
Page 94
Section 11
maIntenanCe
WarnInG
Disconnect all power to the unit before attempting
any service procedures. Contact with electricity
can result in severe injury or death.
11.1 System maintenance
Do the following once a year:
1. Lubricate the System pump, if required, per the
instructions on the pump.
2. Inspect the venting system for obstruction or
leakage. Periodically clean the screens in the
vent terminal and combustion air terminal
(when used).
3. Keep the area around the unit clear and free
of combustible materials, gasoline, or other
flammable vapors or liquids.
4. If the unit is not going to be used for extended
periods in locations where freezing normally
occurs, it should be isolated from the system
and completely drained of all water.
5. Low water cutoffs, if installed, should be
checked every year. Float type low water
cutoffs should be flushed periodically.
6. Inspect and clean the condensate collection,
float switch and disposal system yearly.
7. When a means is provided to neutralize
condensate, ensure that the condensate is being
neutralized properly.
8. Inspect the flue passages, and clean them using
brushes or vacuums, if necessary. Sooting in
flue passages indicates improper combustion.
Determine the cause of the problem and correct
it.
9. Inspect the vent system and air intake system,
and ensure that all joints are sealed properly.
If any joints need to be resealed, completely
remove the existing sealing material, and clean
with alcohol. Apply new sealing material, and
reassemble.
10. Once a year, the items listed below should be
inspected by a qualified service technician:
a. Appliance control
f. Flow switch
b. Automatic gas valve
g. Low water cutoff
c. Pressure switches
h. Burner
d. Blower
i. Heat exchanger
e. Pump
Do the following once every six months:
1. If a strainer is employed in a pressure reducing
valve or the piping, clean it every six months.
11.2 maintenance notes
Use only genuine LAARS replacement parts.
Caution
When servicing the controls, label all wires before
disconnecting them. Wiring errors can cause improp-
er and dangerous operation. Verify proper operation
after servicing.
The gas and electric controls in the NeoTherm
unit are engineered for long life and dependable
operation, but the safety of the equipment depends
on their proper functioning.
11.2.1 Burner
Check the burner for debris. Remove the blower
arm assembly to access the burner. Remove the 4
bolts connecting the blower to the arm. (See Figure
34). Remove the 5 bolts which hold the burner
arm in place. Pull the burner up and out. Clean the
burner, if necessary, by blowing compressed air
from the outside of the burner into the center of the
burner, and wipe the inside of the burner clean with
glass cleaner. A dirty burner may be an indication
of improper combustion or dirty combustion air.
Determine the cause of the problem, and correct
it. If the burner gasket is damaged, replace it when
replacing the burner.
note -
When installing the burner, make sure the
flange is aligned with the mating surface, as each is
keyed to control fit
.
11.2.2 modulating Gas Valve/ Venturi
The modulating gas valve consists of a valve body
that incorporates the On/Off gas flow control and
a negative pressure regulator. It provides the air/
gas ratio control in combination with the Venturi to
the unit. It is designed to operate with gas supply
pressure between 4 and 13 inches w.c.. To remove
the gas valve and or Venturi, shut off the 120 Volt
Summary of Contents for NTV1000
Page 2: ......
Page 35: ...NeoTherm Boilers and Water Heaters Page 31 Fig 20 Ladder Diagram...
Page 36: ...LAARS Heating Systems Page 32 Fig 21 Wiring Diagram...
Page 37: ...NeoTherm Boilers and Water Heaters Page 33...
Page 51: ...NeoTherm Boilers and Water Heaters Page 47 Fig 52 Connection Terminals...
Page 130: ...LAARS Heating Systems Page 126 Fig 140 Machine Frame and Rear Panel 13 3 PARTS ILLUSTRATIONS...
Page 131: ...NeoTherm Boilers and Water Heaters Page 127 Fig 141 Front Panel and Covers...
Page 132: ...LAARS Heating Systems Page 128 Fig 142 Burners and Combustion Chambers...
Page 134: ...LAARS Heating Systems Page 130 Fig 145 Electronic Components...
Page 135: ...NeoTherm Boilers and Water Heaters Page 131 Fig 146 Condensate Trap Fig 147 Control Bezel...
Page 136: ...LAARS Heating Systems Page 132 Fig 148 Flow Switch...
Page 137: ...NeoTherm Boilers and Water Heaters Page 133 This page intentionally left blank...