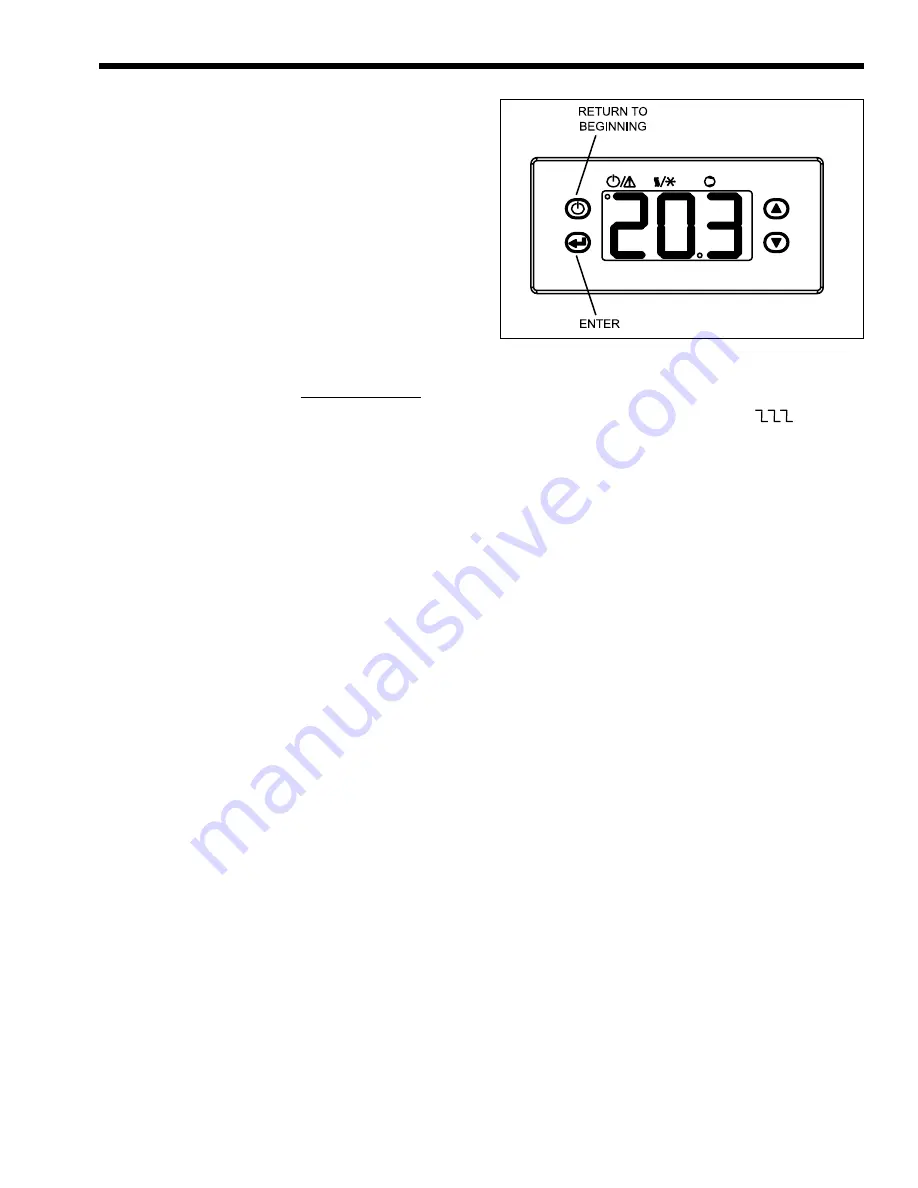
Pennant Pool Heater
Page 13
Figure 6). The LCD screen will display the pool loop
return temperature during normal operation. When the
control is first powered up, it displays
. It then
displays the temperature at the pool loop sensor. After
the temperature is displayed, the current settings
(parameters) may be viewed. To scroll through the
parameters, press the down arrow button to advance to
the next parameter.
5.3.2 Programming Control Parameters
There are thirteen (13) control parameters. Only
three (3) of those should be set, LSP, dLS and Pd. The
remaining parameters are factory set and should not be
changed.
The pool loop temperature (desired pool
temperature) is set by changing the LSP parameter.
After scrolling through the parameters until LSP is
displayed, press the enter button. The setpoint will be
displayed. Press the up arrow or down arrow buttons
until the desired setpoint is displayed. Press the enter
button and the setpoint will be activated. The display
will return to indicating the present pool loop
temperature.
In addition to the ability to set the pool loop
temperature, the differential associated with that
setting may also be adjusted. The differential is set by
changing the dLS parameter. After scrolling through
the parameters until dLS is displayed, press the enter
button. The setpoint will be displayed. Press the up
arrow or down arrow buttons until the desired setpoint
is displayed. Press the enter button and the setpoint
will be activated. The display will return to indicating
the present pool loop temperature.
The last parameter that may be adjusted is Pd,
the pump off delay. After again scrolling through the
parameters until Pd is displayed, press the enter
button. The pump delay time will be displayed. The
pump off delay may be set between 0.1 and 10
minutes. Press the up arrow or down arrow buttons
until the desired setpoint is displayed. Press the enter
button and the setpoint will be activated. The display
will again return to indicating the present pool loop
temperature.
Figure 6. Pool Heater Controller.
5.1 Main Power
Pennant appliances are fitted with pigtail leads
for main power connection. Connect a fused 15-
ampere, 120-volt supply to the black wire. Neutral leg
is connected directly to the white wire. Ground wire is
connected to the green wire.
Wiring diagrams are shown in Section 10 in
Figures 12 through 15. Field wiring is shown in
Section 10 in Figures 16 and 17.
IMPORTANT NOTE: If the backwash operation is
manual the heater must be shut off manually during
backwashing.
Auxiliary Time Clock Wiring:
If a time clock is used to control the pool filter
pump operation, a separate switch or relay must be
used to shut off heater at least 15 minutes before the
filter pump is shut off. Wire the switch or relay to the
field-wiring board’s “Other Ints” terminals. Wire the
switch or relay to the field-wiring board’s “Other Ints”
terminals, after removing the factory-installed jumper.
All field-installed electrical safety devices and
field-installed controllers can be connected in series to
the Pennant’s “Other Ints” terminals on the field-
wiring board (remove the factory-installed jumper).
5.2 Temperature (Operating) Control
The Pennant temperature control operates by
measuring the pool loop return temperature, before the
heater inlet piping. It is adjustable to a maximum of
104° F and will prevent heater operation at return
temperatures above 104° F. It also controls the pool
heater pump and the temperature of the water entering
the heat exchanger. It also controls the Pennant pump
operation and the mixing system, which tempers the
water entering the heat exchanger to prevent damage
from condensation. The sensors for the control are
installed as shown in Figure 5 and Section 4.3, Sensor
Locations. The automatic mixing system sensor,
already installed, is shown in Figure 4. During
operation, the automatic mixing system diverts water
from the outlet to the inlet to “pre warm” the water to
a minimum inlet temperature of 120°F. This prevents
condensation from forming, which can damage the
heater.
5.3 Programming the Temperature
Control
5.3.1 Temperature Control Overview
The digital display on the control has the
following uses:
•
To display the actual pool loop temperature
during normal operating mode.
•
To allow the user to view and adjust the
control settings.
Figure 6 identifies the control buttons.
The Pool Heater Temperature Control face
contains an LCD screen and four (4) buttons (see
Summary of Contents for Pennant PNCP
Page 27: ...Pennant Pool Heater Page 27 Figure 9 Sheet Metal Components...
Page 31: ...Pennant Pool Heater Page 31 Figure 13 Pennant 1250 2000 Ladder Diagram...
Page 32: ...LAARS Heating Systems Page 32 Figure 14 Pennant 500 1000 Wiring Schematic...
Page 33: ...Pennant Pool Heater Page 33 Figure 15 Pennant 1250 2000 Wiring Schematic...
Page 34: ...LAARS Heating Systems Page 34 Figure 16 Field Wiring PNCP 500 1000...
Page 35: ...Pennant Pool Heater Page 35...