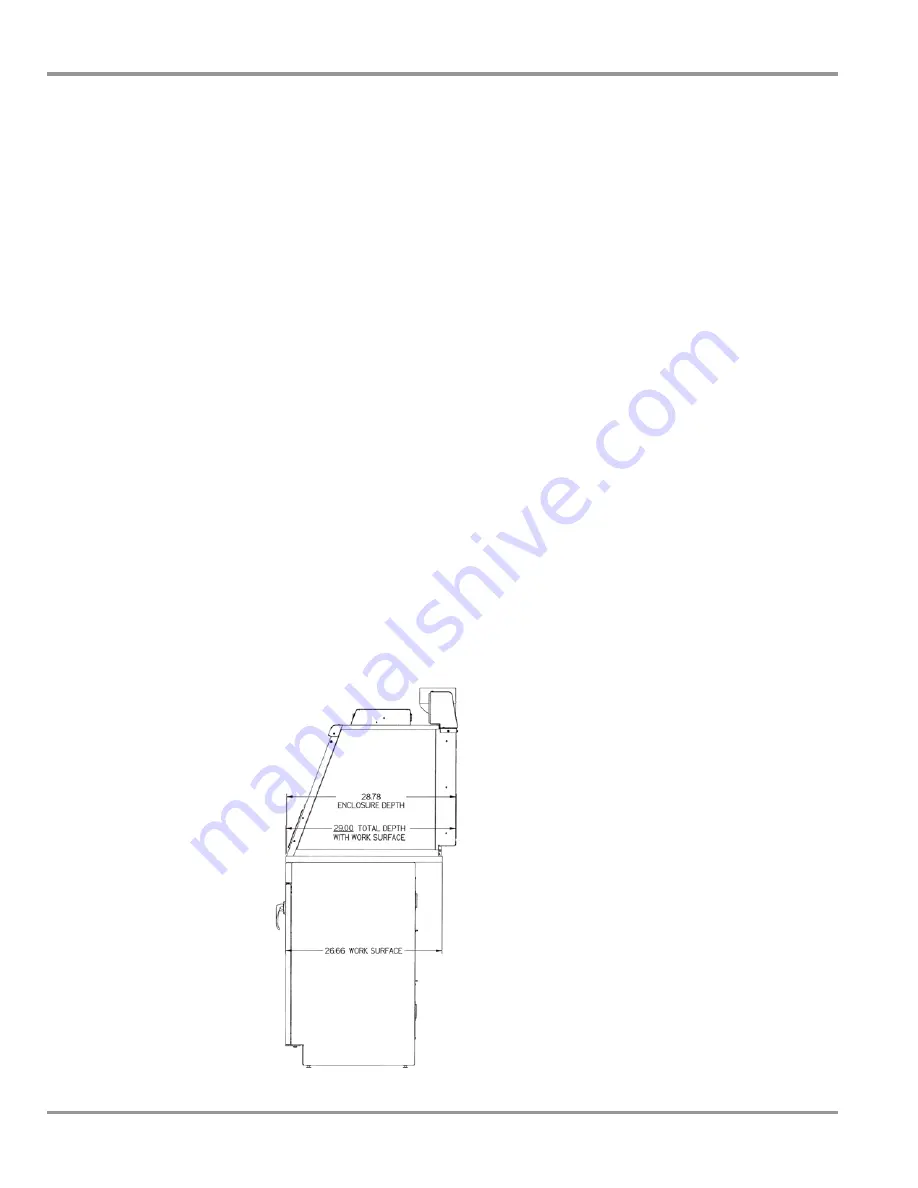
Chapter 3: Getting Started
Product Service 1-800-522-7658
12
Work Surface Specifications
The work surface should be smooth, rigid, and durable, such as a chemically
resistant epoxy resin or stainless steel. The surface should be non-porous and
resistant to the acids, solvents and chemicals used in conjunction with the
XPert or XVS enclosure. The work surface should also contain a dished
recessed area for containing primary spills.
Work Surface and Vented Enclosure Installation
1. Level the base cabinets and the work surface. Work surface should be
placed flush with the front of the base cabinet as shown in Figure 3-1.
2. Position the work surface in its intended location and with the front of
the work surface, (wide flange or spill trough), towards you.
3. Secure the work surface to the base cabinet with a structural adhesive
or silicone sealant.
4. Insert the supplied mounting screws in the four holes for epoxy work
surfaces. For stainless steel work surfaces use #10-24 x 3/8" hex
machine screws. (Labconco P/N 1885806). Allow a minimum of 1/8"
clearance under the head of the screw for positioning the enclosure.
5. Place the enclosure on the work surface and slide the rear flange and
front air foil flanges under the mounting screw heads.
6. Tighten the four screws to complete the installation.
Figure 3-1
Side View of Typical Installation
Summary of Contents for Protector XVS Series
Page 49: ...Chapter 7 Accessorizing your XPert or XVS Enclosure Product Service 1 800 522 7658 45...
Page 54: ...Appendix A Replacement Parts Product Service 1 800 522 7658 50...
Page 56: ...Appendix B Dimensions Product Service 1 800 522 7658 52 2 3 and 4 Units...
Page 57: ...Appendix B Dimensions Product Service 1 800 522 7658 53 2 3 and 4 Units...
Page 58: ...Appendix B Dimensions Product Service 1 800 522 7658 54...