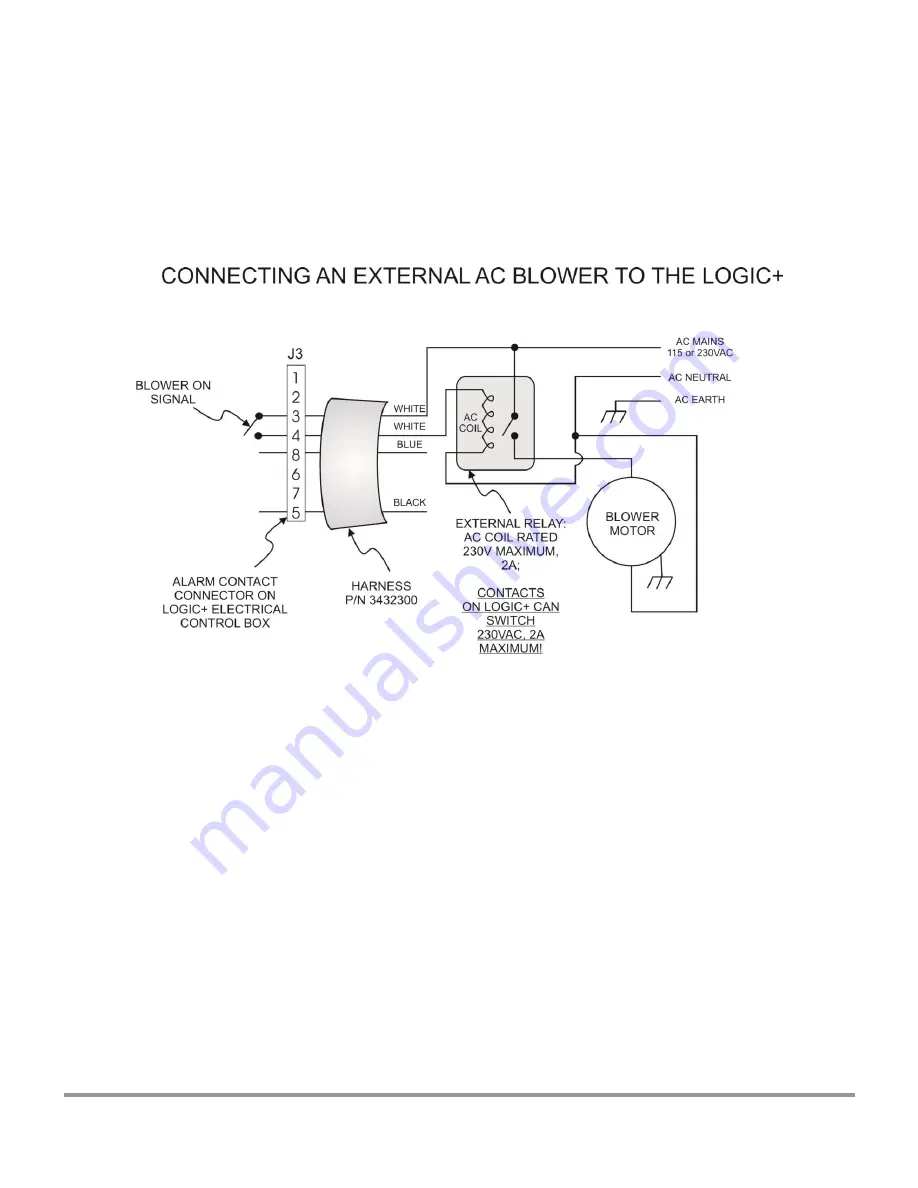
Product Service 1-800-522-7658
165
The next diagram shows an example of using an AC powered coil, so the +12V supply
from the Logic+ is not used. The Hasco HAT 903 relay series offers a 120VAC coil that
requires only 16mA AC current as well as a 230VAC coil that draws only 9mA. The
alternate circuit that uses an AC mains rated coil voltage is shown below – it does not
utilize the FUSED+12V and CIRCUIT COMMON from the Labconco Logic+.
Note: A W199 Magnacraft Series relay can switch up to 300Vac @ 40 Amps……….it’s coil
is rated for 12 Vdc, 171mA, or approx. 2 watt coil…………..
Also an Omron G7Z has a 12VDC coil rated 3.7 watts, and can switch 440VAC at 25
amps…