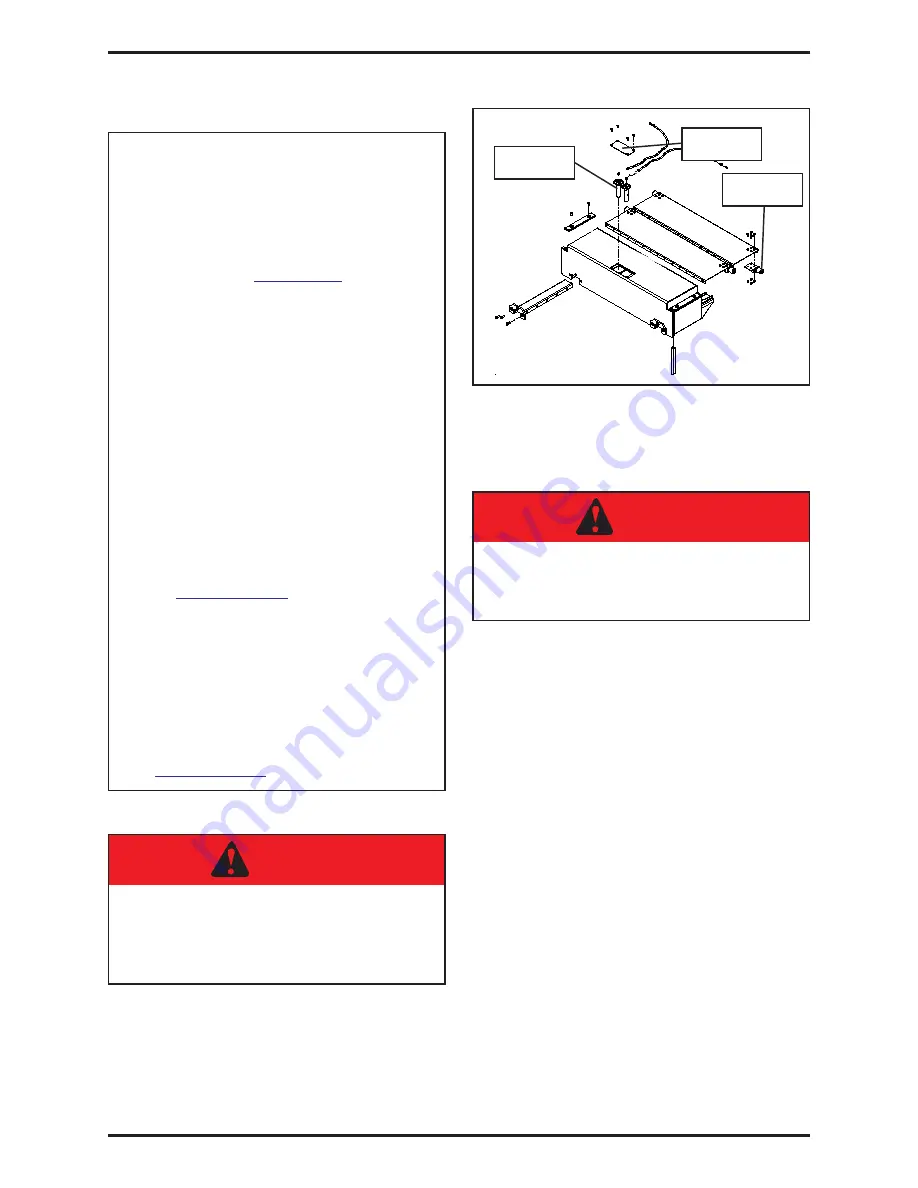
AUTOMIZER
VERSA HAND
TM
1-48
1.12.10 PACKER CYLINDER REPLACEMENT
PACKER CYLINDER
REPLACEMENT PROCEDURE
1.
Ensure that the parking brake is
applied and the vehicle is tagged
out for maintenance purposes
(refer to the
section 1.5
“Lockout/
Tagout procedure”).
2.
Start the engine, engage the
hydraulic pump.
3.
Then using the joystick, extend
the automated arm to give a better
access to the hopper area.
4.
Fully extend the packer.
5.
Disengage the pump and stop the
engine.
6.
Remove the floating panel (refer
to
section 1.12.9
).
7.
Open the access cover
(Figure #1.68), remove both
cylinder pins and retract the
packer.
8.
Remove the roller assemblies on
the follower panels (See
section 1.12.8
).
ACCESS
COVER
CYLINDER
PINS
FIGURE #1.68
ROLLER
ASSEMBLY
DANGER
SECURE THE AREA AROUND THE
PATH OF THE ARM WHEN
PERFORMING MAINTENANCE OR
REPAIR.
DANGER
DO NOT CLIMB INTO THE
HOPPER WHILE THE PACKER IS
MOVING.
Summary of Contents for Automizer Versa Hand
Page 2: ...AUTOMIZER VERSA HANDTM 1 2...
Page 4: ...AUTOMIZER VERSA HANDTM 1 4...
Page 8: ...AUTOMIZER VERSA HANDTM 1 8...
Page 58: ...AUTOMIZER VERSA HANDTM 1 58 FIGURE 1 81 INPUT OUTPUT COVER ELECTRICAL COILS...
Page 69: ...1 69 GENERAL MAINTENANCE FIGURE 1 89A Strainer Seal...
Page 77: ...1 77 GENERAL MAINTENANCE A B C BEHIN D D F MAIN RELIEF B E...
Page 105: ...1 105 GENERAL MAINTENANCE NOTES...