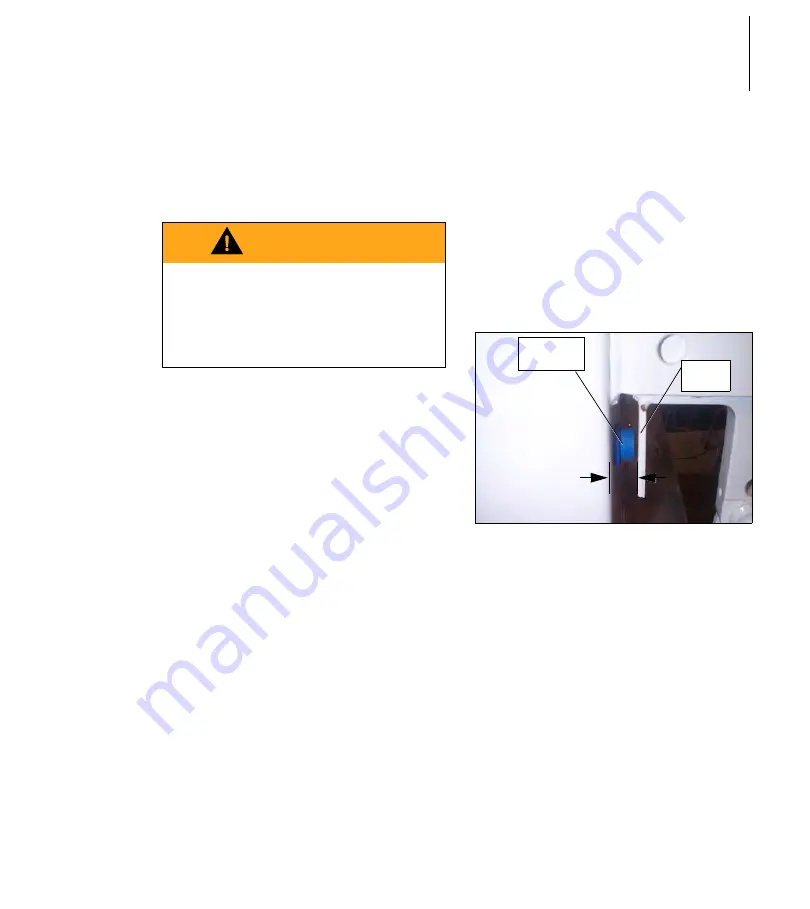
85
Expert(t) 2000
TM
Maintenance Manual
“click”, as the cylinder head is
moving down (Figure 138. “Body
raised limit switch” & Figure 139.
“Left-hand side tailgate
cylinder”).
Optional Limit Switch
and Proximity Switch
An optional limit switch is also
available to warn the operator that the
tailgate is fully open. This limit switch is
located next to the left-hand side
tailgate hinge. When the tailgate
reaches its fully open position, the
optional fully open switch will trigger a
red light on the console.
A proximity switch may instead be
used to trigger the backup alarm and
warning buzzer in the cab (Tailgate
unlocked).
Note:The location and the
procedure to adjust the
proximity switch may differ
from the standard limit switch.
The proximity switch will be located
behind the left-hand side tailgate
locking mechanism. This proximity
switch requires no other maintenance
than checking the distance between
the metal target and the face of the
proximity switch. The proximity switch
must be tighten at 3/16” of an inch from
the metal plate (Figure 140. “Proximity
switch side-view” & Figure 141.
“Proximity switch front-view”).
Figure 140. Proximity switch
side-view
WARNING
M
AKE
SURE
NO
ONE
IS
STANDING
BEHIND
OR
NEAR
THE
TAILGATE
WHEN
ADJUSTMENT
PROCEDURE
IS
CARRIED
OUT
.
Proximity
Switch
Metal
Target
3/16”
3/16”
Summary of Contents for expert 2000
Page 1: ......
Page 2: ......
Page 3: ...MAINTENANCE MANUAL 12 14 2006 Part 55379 ...
Page 4: ......
Page 10: ...viii Table of Contents ...
Page 96: ...86 CHAPTER 3 Maintenance Figure 141 Proximity switch front view ...
Page 118: ...108 CHAPTER 3 Maintenance Figure 170 Ball valve in closed position ...
Page 140: ...130 CHAPTER 4 Lubrication PACKER ...
Page 141: ...131 Expert t 2000TM Maintenance Manual BODY CHASSIS HINGES ...
Page 142: ...132 CHAPTER 4 Lubrication HOPPER SECTION STANDARD VERSION ...
Page 143: ...133 Expert t 2000TM Maintenance Manual CRUSHER PANEL ...
Page 144: ...134 CHAPTER 4 Lubrication FULL WIDTH TAILGATE ...
Page 154: ...144 CHAPTER 5 Troubleshooting ...
Page 156: ...146 Appendix CONNECTORS Commonly used Electrical Connectors Deutsch AMP ...
Page 168: ...158 Appendix ...
Page 170: ...160 Appendix ...
Page 171: ......
Page 172: ......