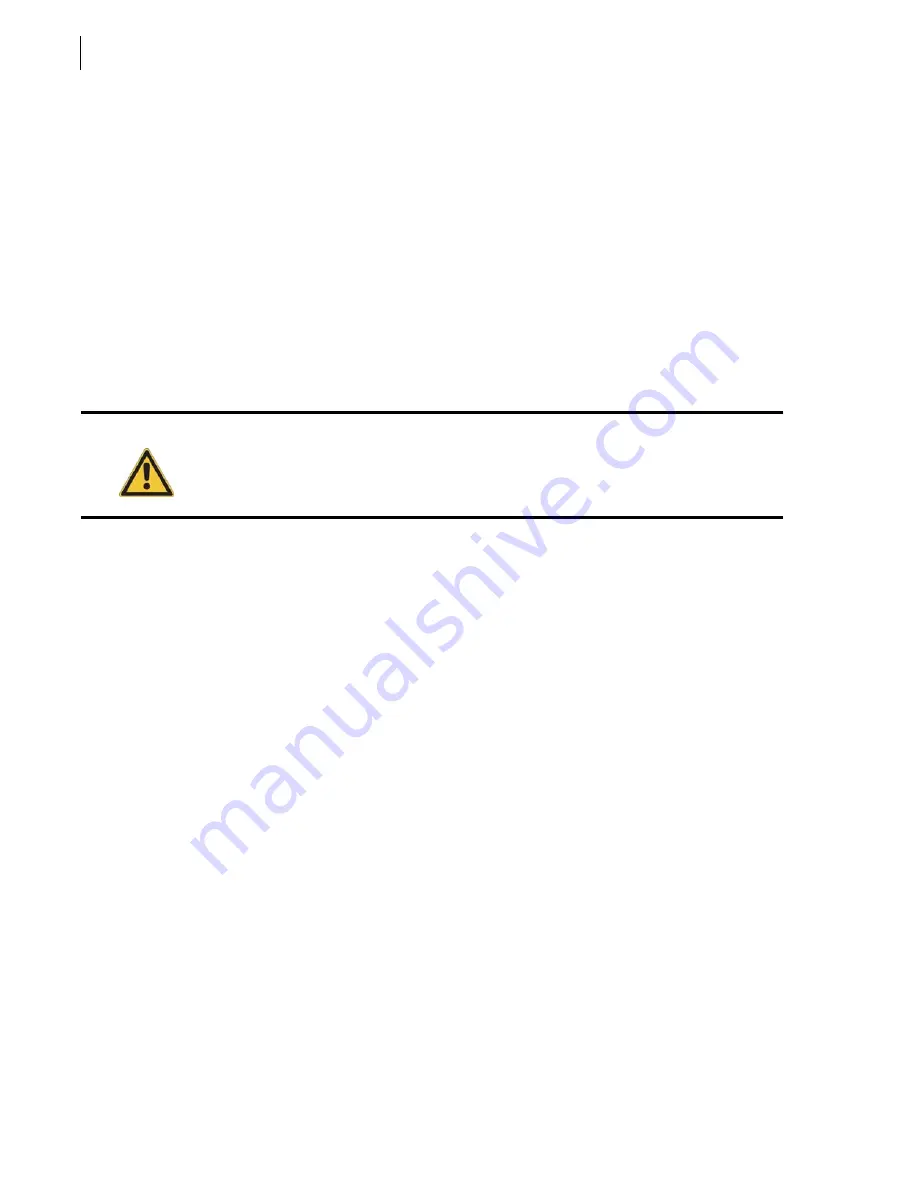
38
General Maintenance
To adjust a proximity switch:
1.
Loosen the proximity switch nuts.
2.
Adjust the proximity switch so that there is a gap of approximetely 3/16
of an inch (4.8
mm)
between the plate (target) and the switch.
3.
Tighten up the nuts.
4.
Test the operation.
The proximity switch light should turn on when the target is detected; if not, repeat the adjustment
procedure.
In the following sections, you will learn how to adjust limit/proximity switches based on the function
for which they are used.
Adjusting Packer Extend Limit/Proximity Switch
Packer limit/proximity switches were adjusted at the factory for optimal packer operation. If the area
behind the packer is not properly cleaned
daily,
limit/proximity switches may no longer stop the
packer or may prevent automatic cycles from working properly.
Furthermore, over time, misalignment of the components may occur due to the frequent back and
forth motion of the packer. An adjustment might be necessary to prevent cylinders from completely
extending and retracting to the end of their strokes.
On some units, the packer range of motion is controlled by two limit switches and on other units, it is
controlled by a set of one limit switch and one proximity switch. The limit/proximity switch that
stops the packer during extension (packer extend) is located near the hopper floor, on the curbside,
just under the automated arm housing (see Figure 3-22). The limit switch that stops the packer
during retraction (packer retract) is located on front right-hand side hopper corner, behind the cab
(see Figure 3-23).
Danger!
Always lock out and tag out the vehicle when inspecting it or performing maintenance
on it (see
Locking Out and Tagging Out the Vehicle
.
Summary of Contents for MINIMAX
Page 1: ...MINIMAX TM MAINTENANCE MANUAL...
Page 2: ......
Page 3: ...MINIMAX MAINTENANCE MANUAL...
Page 8: ...vi Table of Contents Adjusting Arm Speed 164...
Page 30: ...22 Safety Figure 2 17 Drain valve on air tank...
Page 72: ...64 Lubrication Figure 4 10 Lubrication chart Helping Hand arm...
Page 80: ...72 Lubrication...
Page 90: ...82 Hydraulic System Figure 5 8 Oil temp level gauge Figure 5 9 Steel hydraulic tank...
Page 102: ...94 Hydraulic System Figure 5 21 Strainer assembly Strainer...
Page 106: ...98 Hydraulic System Figure 5 25 Detecting cylinder internal leaks 1 2 3 4 5 A A A...
Page 108: ...100 Hydraulic System...
Page 113: ...Electrical System 105 Electrical Schematics Cab Adaptation...
Page 114: ...106 Electrical System Cab Console Controls...
Page 115: ...Electrical System 107 Cab Controller...
Page 116: ...108 Electrical System Chassis...
Page 117: ...Electrical System 109 Body Module rear side...
Page 118: ...110 Electrical System Body Module front side...
Page 119: ...Electrical System 111 Tailgate Lighting...
Page 120: ...112 Electrical System Panic Bars Crusher Panel Tipper Interlocks...
Page 121: ...Electrical System 113 Cameras Switchpack Details Interlocks AUTO 10 SEC INHIBIT AUTO N AUTO ON...
Page 122: ...114 Electrical System...
Page 127: ...Troubleshooting 119 Figure 8 4 Ball end hex wrench metric and SAE...
Page 134: ...126 Troubleshooting Figure 8 6 Tailgate locking mechanism...
Page 156: ...148 Multiplexing...
Page 162: ...154 Multiplexing...
Page 164: ...156 Lifting Arm Figure 10 1 Mounting bolts Figure 10 2 Helping Hand gripper Figure 10 3 Hoses...