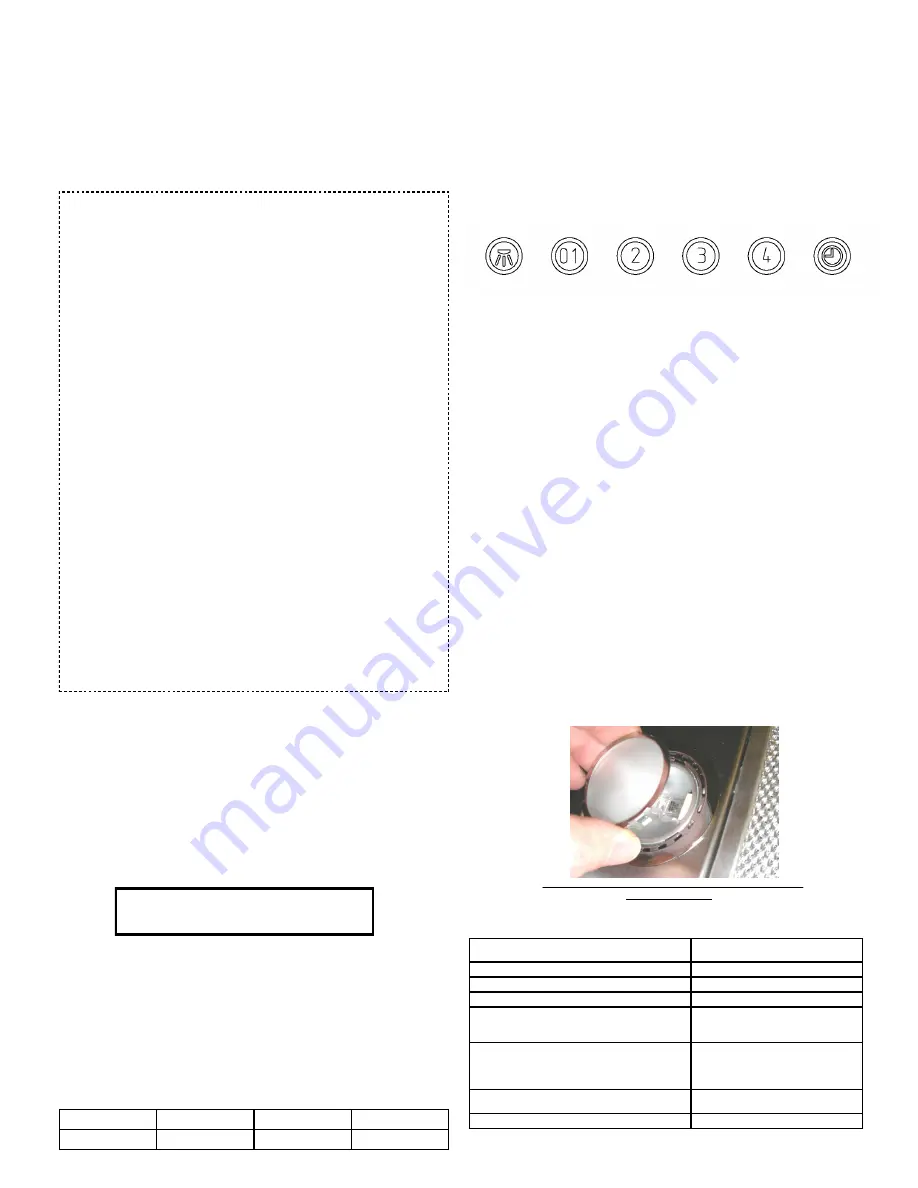
FMH Range Hoods
W1103 Revision: 14/10/2011
4
4.4 Fixing the Hood to the Wall
If you are fitting a splashback it should usually be fitted before the hood.
Note:
The chimney can be removed to ease handling of the hood.
The supporting wall must be of good quality, have an even surface and be
sturdy enough to support the extractor.
Fixings must be used which are suitable for the type of wall construction.
Fixing the hood to the wall requires
a minimum of 2 people.
No wall fixingsare provided.
Method
Note: Figures referenced in this section can be found on Page 3.
Mark a horizontal line (A) denoting the hood’s bottom edge - if you have
already fitted a splashback then the top edge of this will serve. A vertical
centre line up to the desired finished chimney height will also help you to
accurately position the hood and chimney bracket.
Remove the grease filters to gain access the internal fixing holes.
Mark the positions of the hood fixing hole centres, (see
Figure 2 “Example of
universal hood fixing detail”
. Note: This shows a typical hood installation and
is not intended to accurately represent the geometry of your hood.
Offer the hood up to the wall in the desired position and mark the wall
through the fixing holes in the hood rear. This is a 2 person job.
Mark and prepare a hole(s) suitable to accommodate 150mm diameter
ducting (160mm min). If using the rear exhaust spigot position then accu-
racy is critical - see Figure 1.
Secure the hood, using fixings suitable for the wall construction, in the
previously marked positions.
This is a 2 person job.
Tip: for rear exit you may have to connect the ducting prior to fixing the
hood to the wall - rigid ducting is strongly recommended.
Unscrew the chimney bracket from the inner chimney and mark the posi-
tions of the chimney bracket fixing holes - the central hole is for viewing
your centre line (see Figure 3).
Tip: the bracket finishes flush with the chimney top. You may find it easier
to slide the chimney up to the desired height and mark the position of the
top corners—you can then line the top of the chimney bracket up with
these marks.
Secure the chimney bracket, using fixings suitable for the wall construc-
tion, in the previously marked positions (see Figure 3).
Connect the ducting and electrical supply cord as described in section 4.5
and 4.6.
Slide the inner chimney over the bracket and secure using the screws
previously removed.
4.5 Connecting the Ducting
Connect ducting to extractor exhaust spigot. You may find this easier with
the chimney removed. The chimney is attached using M4 machine screws
which can be accessed through the filter opening(s). For rear exit exhaust
positions the duct should be attached prior to fixing the extractor to the wall.
When the extractor is in position, check that the duct has not been flattened
or kinked along its route.
Connect the ducting to the wall louvre or alternative outside termination.
Secure the louvre to the outside wall. Ensure that any air fins are directed
downwards.
Refit the grease filters.
4.6 Electrical Installation
The extractor is a stationary appliance designed to be connected by fixed
wiring to the electrical supply. A competent electrical technician must per-
form the electrical installation.
The extractor must be fed from a 220—240Vac single phase electrical sup-
ply using a switched spur fitted with a 3A fuse. The spur should be located
such that the supply can be disconnected from the extractor using the switch
after installation (adjacent to the extractor/cooker is best). The means of
disconnecting from the supply must have a minimum contact separation of
3mm in all poles. Alternatively a means of disconnection in the fixed wiring
according to the relevant wiring regulations must be fitted.
A supply cord for connecting the extractor to the spur is included.
The mains supply is connected to the free end of this cord as follows:
SECTION 5. OPERATING INSTRUCTIONS
Switch power on at the fused spur.
The extractor has 6 push-buttons which illuminate when selected.
Their functions are summarised below.
Note: 2200mm model has 3 sets of controls for independent control of each fan).
The extractor controller will automatically switch off the appliance if
there has been no operator action for 4 hours.
After 30 hours accumulated running GREASE FILTER SATURATION
will be signaled by all 6 indicators flashing. Reset by pressing Push-
button FAN OFF (delay).
SECTION 6. MAINTENANCE
Regular maintenance is essential to ensure good performance and
long-life.
To clean the stainless steel surfaces of the extractor use a proprie-
tary cleaning agent. Do not use abrasive cleaning materials or prod-
ucts.
Clean the grease filters in a dishwasher or by hand-washing in hot
water and detergent. Wash the filters at least every 2 months -
sooner if the extractor is used extensively.
To maintain the immaculate appearance of the extractor, and to min-
imise fire risk, ensure that grease deposits on the extractor surfaces
are kept to a minimum by regular cleaning.
Should you wish to clean the hood internally (accessed when the
filters are removed) then you must
first isolate (switch off) the
electrical supply to the hood
at the switched spur.
To access the halogen lamps for replacement prise off the chrome
ring immediately surrounding/retaining the frosted glass with a suita-
ble flat implement (eg. screwdriver), taking care not to scratch or
damage the light assembly (see picture below). Only replace with
bulbs of the same type and rating as originally supplied (12V 20W
G4 LV halogen capsule lamp).
Light Assembly
SECTION 7. SPECIFICATIONS
ELECTRICAL HAZARD
DISCONNECT ELECTRICAL SUPPLY
BEFORE PROCEEDING FURTHER
LIGHTS ON/
OFF
FAN ON
SPEED 1
FAN OFF
(Immediate)
FAN ON
SPEED 2
FAN ON
SPEED 3
FAN ON
SPEED 4
FAN OFF
Delayed for
10 Minutes
to clear
fumes
Nominal airflow free air (internal fan)
Nominal airflow in free air (EC310 wall fan)
1,000 m
3
/hr
3,000 m
3
/hr
Supply voltage:
220-240V~ 50Hz
Halogen lamp voltage:
12V
Blower power input:
250W per fan
Halogen lamp power:
2 x 20W Single Fan
4 x 20W Twin Fan
5 x 20W Triple Fan
Total power:
290W Single Internal Fan
580W Twin Internal Fan
850W Triple Internal Fan
EC310 Wall fan models 610W
Fuse size for electrical supply:
3A Single Internal Fan
5A All other variants
Blower spigot diameter:
150mm
Core
Live
Neutral
Protective Earth
Core Colour
Brown
Blue
Green/Yellow