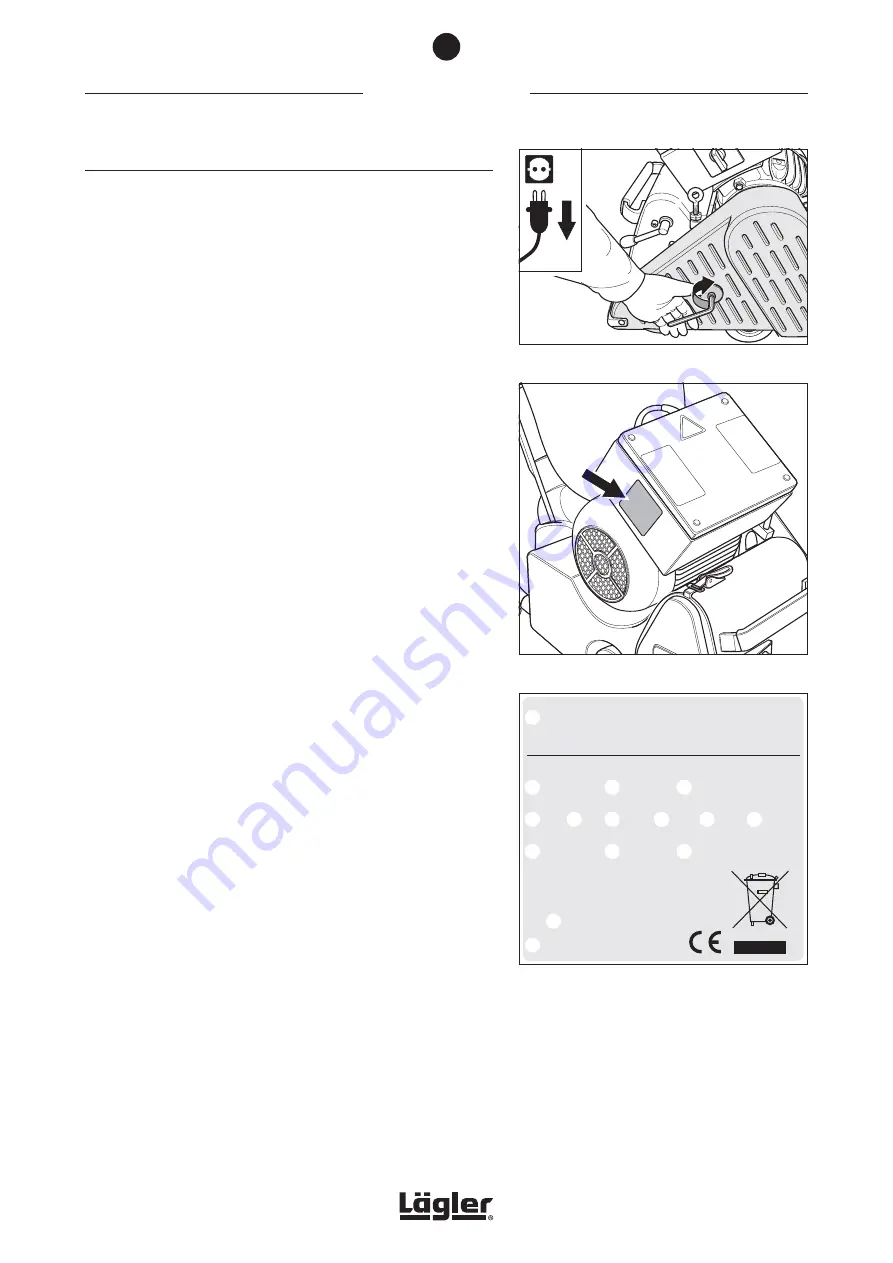
HUMMEL
®
01.01.2019
English / Englisch
3.1.2 MOTOR TYPE PLATE
The motor type plate of the HUMMEL
®
is located on the switch
box of motor (fig. 6).
The following technical data are specified on the motor type plate
(fig. 7):
1
Manufacturer
2
Serial number of machine (Mach.-No.)
3
Year of manufacture (Year)
4
Motor size (Type)
5
Required mains voltage in volt (V)
6
Current consumption in ampere (A)
7
Motor frequency in CPS (Hz)
8
Motor power in kilowatt (KW)
9
Motor speed in 1/min (Rpm)
10
Power factor cos phi (cos)
11
Insulation class (Insul. Cl.)
12
Protection class (Prot. Cl.)
13
Type of current
14
Country of manufacture
Fig. 6
Motor type plate on switch box.
Fig. 7
Data on motor type plate.
14
13
5
6
7
8
9
10
11
12
V
A
Hz
KW
Rpm
cos
XXX
XX
XX
XX
XXXX
0.XX
Insul.Cl.
Prot.Cl.
Type of Current
B
IP54
AC
Type
BG 112
Made in Germany
XXXXX-XX
12345
Mach.-No.
Year
XXXXX-XX
XXXX
Kappelrain 2
D-74363 Güglingen-Frauenzimmern
Tel. +49 7135 98900
www.laegler.com
Eugen Lägler GmbH
1
2
3
2
4
TECHNICAL DATA
3
Fig. 5
Close the belt guard.
15