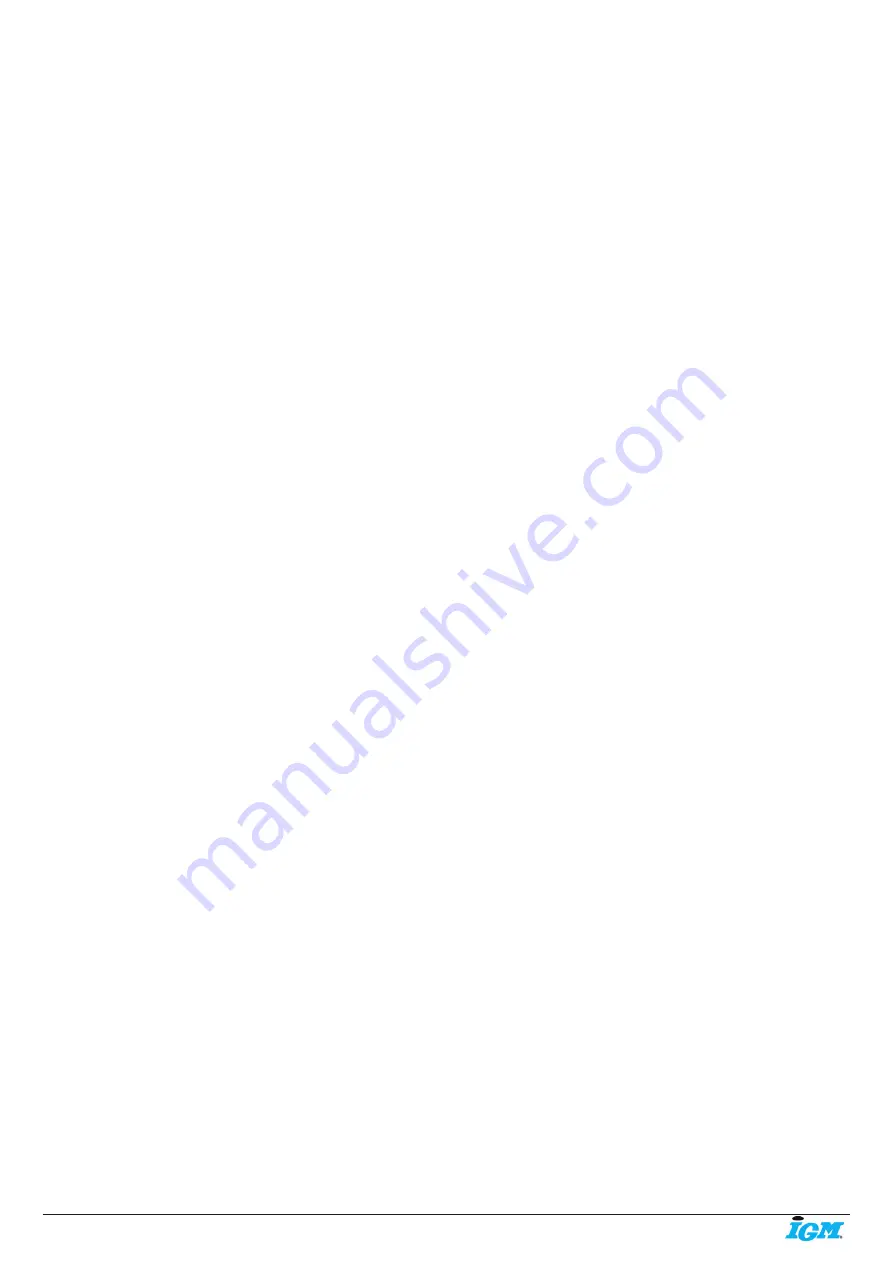
-6-
www.igm.cz
feed direction.
• Never leave tool running unattended. Do not
leave the tool until it comes to a complete stop.
When unattended, unplug the tool.
• Maintain tools with care. Keep cutting
tools sharp and clean for better and safer
performance.
• Follow instruction for lubricating and changing
accessories. Inspect tool cords periodically
and if damaged have then repaired by an
authorized service facility. Inspect extension
cords periodically and replace if damaged.
Keep hand dry, clean and free from oil and
grease.
• Illumination. Adequate general or localized
lighting shall be provided.
• Dust Collection. During use the saw benches
shall be connected to an external chip and dust
extraction system.
4.5 Guarding related warnings
• Keep guards in place. Guards must be in
working order and be properly mounted.
A guard that is loose, damaged, or is not
functioning correctly must be repaired or
replaced.
• Always use saw blade guard and riving
knife for every through–cutting operation. For
through-cutting operations where the saw blade
cuts completely through the thickness of the
workpiece, the guard and other safety devices
help reduce the risk of injury.
• Make sure the saw blade is not contacting
the guard, riving knife or the workpiece before
the switch is turned on. Inadvertent contact of
these items with the saw blade could cause a
hazardous condition.
• Adjust the riving knife as described in
this instruction manual. Incorrect spacing,
positioning and alignment can make the riving
knife ineffective in reducing the likelihood of
kickback.
• For the riving knife to work, it must be
engaged in the workpiece. The riving knife is
ineffective when cutting workpieces that are
too short to be engaged with the riving knife.
Under these conditions a kickback cannot be
prevented by the riving knife.
• Use the appropriate saw blade for the riving
knife. For the riving knife to function properly,
the saw blade diameter must match the
appropriate riving knife and the body of the saw
blade must be thinner than the thickness of
the riving knife and the cutting width of the saw
blade must be wider than the thickness of the
riving knife.
4.6 Work related warnings
• Danger: never place your fingers or hands
in the vicinity or in line with the saw blade. A
moment of inattention or a slip could direct
your hand towards the saw blade and result in
serious personal injury.
• Feed the workpiece into the saw blade or
cutter only against the direction of rotation.
Feeding the workpiece in the same direction
that the saw blade is rotating above the table
may result in the workpiece, and your hand,
being pulled into the saw blade.
• Never use the mitre gauge to feed the
workpiece when ripping and do not use the rip
fence as a length stop when cross cutting with
the mitre gauge. Guiding the workpiece with the
rip fence and the mitre gauge at the same time
increases the likelihood of saw blade binding
and kickback.
• When cutting longitudinally, move the
workpiece behind the part between the ruler
and the saw blade. If the distance between the
disc and the ruler is less than 150 mm, use the
feeder. If it is less than 50 mm, use the feed
plate. “Extended arms” and similar accessories
keep your hands at a safe distance from the
saw blade.
• Use only the push stick provided by the
manufacturer or constructed in accordance
with the instructions. This push stick provides
sufficient distance of the hand from the saw
blade.
• Never use a damaged or cut push stick. A
damaged push stick may break causing your
hand to slip into the saw blade.
• Do not perform any operation “freehand”.
Always use either the rip fence or the mitre
gauge to position and guide the workpiece.
“Freehand” means using your hands to support
or guide the workpiece, in lieu of a rip fence
or mitre gauge. Freehand sawing leads to
misalignment, binding and kickback.
• Never reach around or over a rotating saw
blade. Reaching for a workpiece may lead to
accidental contact with the moving saw blade.
• Provide auxiliary workpiece support to the
rear and/or sides of the saw table for long and/
or wide workpieces to keep them level. A long
and/or wide workpiece has a tendency to pivot
on the table’s edge, causing loss of control, saw
blade binding and kickback.
• Feed workpiece at an even pace. Do not
bend or twist the workpiece. If jamming occurs,
turn the tool off immediately, unplug the tool
then clear the jam. Jamming the saw blade by
the workpiece can cause kickback or stall the
motor.
• Do not remove pieces of cut-off material while
the saw is running. The material may become
trapped between the fence or inside the saw
blade guard and the saw blade pulling your
fingers into the saw blade. Turn the saw off and
wait until the saw blade stops before removing
material.
• Use an auxiliary fence in contact with the table
top when ripping workpieces less than 2 mm
thick. A thin workpiece may wedge under the rip
fence and create a kickback.
4.7 Kickback causes and related warnings
• Never stand directly in line with the saw blade.
Always position your body on the same side
of the saw blade as the fence. Kickback may
propel the workpiece at high velocity towards
anyone standing in front and in line with the
saw blade.
• Never reach over or in back of the saw blade
to pull or to support the workpiece. Accidental
contact with the saw blade may occur or
kickback may drag your fingers into the saw
blade.
• Never hold and press the workpiece that is
being cut off against the rotating saw blade.
Pressing the workpiece being cut off against the
saw blade will create a binding condition and
kickback.
• Align the fence to be parallel with the saw
blade. A misaligned fence will pinch the
workpiece against the saw blade and create
kickback.
• Use extra caution when making a cut into
blind areas of assembled workpieces. The
protruding saw blade may cut objects that can
cause kickback. Note, the above safety warning
only applies to tools where such cuts are
permitted by design and instruction.
• Support large panels to minimise the risk of
saw blade pinching and kickback. Large panels
tend to sag under their own weight. Support(s)
must be placed under all portions of the panel
overhanging the table top.
• Use extra caution when cutting a workpiece
that is twisted, knotted, warped or does not
have a straight edge to guide it with a mitre
gauge or along the fence. A warped, knotted,
or twisted workpiece is unstable and causes
misalignment of the kerf with the saw blade,
binding and kickback.
• Never cut more than one workpiece, stacked
vertically or horizontally. The saw blade could
pick up one or more pieces and cause kickback.
• When restarting the saw with the saw blade
in the workpiece, centre the saw blade in the
kerf so that the saw teeth are not engaged in
the material. If the saw blade binds, it may lift
up the workpiece and cause kickback when the
saw is restarted.
• Keep saw blades clean, sharp, and with
sufficient set. Never use warped saw blades or
saw blades with cracked or broken teeth. Sharp
and properly set saw blades minimise binding,
stalling and kickback.
4.8 Table saw operating procedure warnings
• Turn off the table saw and disconnect the
power cord when removing the table insert,
changing the saw blade or making adjustments
to the riving knife or saw blade guard, and when
the machine is left unattended. Precautionary
measures will avoid accidents.
• Never leave the table saw running unattended.
Turn it off and don’t leave the tool until it comes
to a complete stop. An unattended running saw
is an uncontrolled hazard.
• Locate the table saw in a well-lit and level
area where you can maintain good footing and
balance. It should be installed in an area that
provides enough room to easily handle the size
of your workpiece. Cramped, dark areas, and
uneven slippery floors invite accidents.
• Frequently clean and remove sawdust from
under the saw table and/or the dust collection
device. Accumulated sawdust is combustible
and may self-ignite.
• The table saw must be secured. A table saw
that is not properly secured may move or tip
over.
• Remove tools, wood scraps, etc. From
the table before the table saw is turned on.
Distraction or a potential jam can be dangerous.
• Always use saw blades with correct size and
shape (diamond versus round) of arbour holes.
Saw blades that do not match the mounting
hardware of the saw will run off-centre, causing
loss of control.
• Never use damaged or incorrect saw blade
mounting means such as flanges, saw blade
washers, bolts or nuts. These mounting means
were specially designed for your saw, for safe
operation and optimum performance.
• Never stand on the table saw, do not use