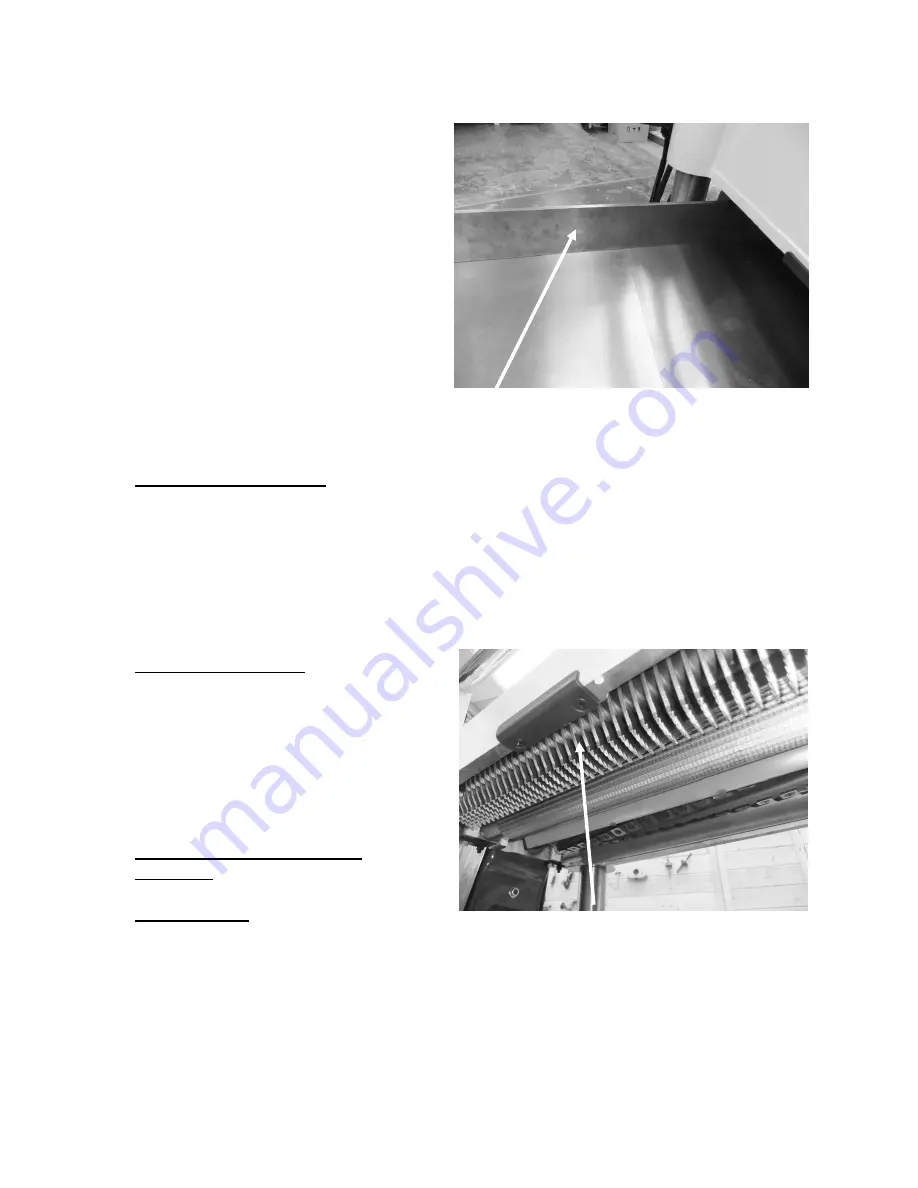
14
3.
Bring the extension table up level with the main table [check both sides of the
table].
4.
By loosening one of the fixing
bolts and tightening the jacking
screw, the table can be jacked
parallel with the main table. This
process must be done slowly jacking
a small amount each side so that no
excessive strain is put on the table
flange. Excessive jacking could crack
the cast iron table.
5.
Once the tables are parallel, check
that both tables are still level and
adjust if required.
6.
Repeat for the other extension
table.
Note.
The tables must be checked at both sides.
Cleaning the machine.
The machine is shipped with the non-painted surfaces protected from rust by a film
of grease.
The grease must be removed with WD40 or similar, as it attracts saw dust and dirt.
The surfaces should then be coated with a Teflon lubricant or similar. Teflon tends
to dry and will not attract sawdust and dirt. To reduce table friction, it is
recommended that the table is polished with a good-quality wax. This will also afford
a degree of protection from rust.
Anti-kickback teeth.
The anti-kickback teeth must be free
to move, or they will not fulfill their
function.
With the power disconnected, check
that all the teeth move freely. If they
do not, lubricate with Teflon-based
lubricant.
Running and adjusting the
machine.
Adjustments.
Note.
The machine has had all its functions calibrated at the factory, but due to
shipping conditions, some movement may have taken place. This is unavoidable,
and it is therefore recommended that the following checks are made prior to starting
Straight edge
Anti-kickback teeth
Summary of Contents for MPLAN1510-0120
Page 2: ......
Page 25: ...25 Exploded view drawings...
Page 26: ...26...
Page 27: ...27...
Page 28: ...28...
Page 36: ...36...
Page 37: ...1 Laguna Tools MPLAN1510 0130 Platinum Series 16 Planer...
Page 61: ...25 Exploded view drawings...
Page 62: ...26...
Page 63: ...27...
Page 64: ...28...