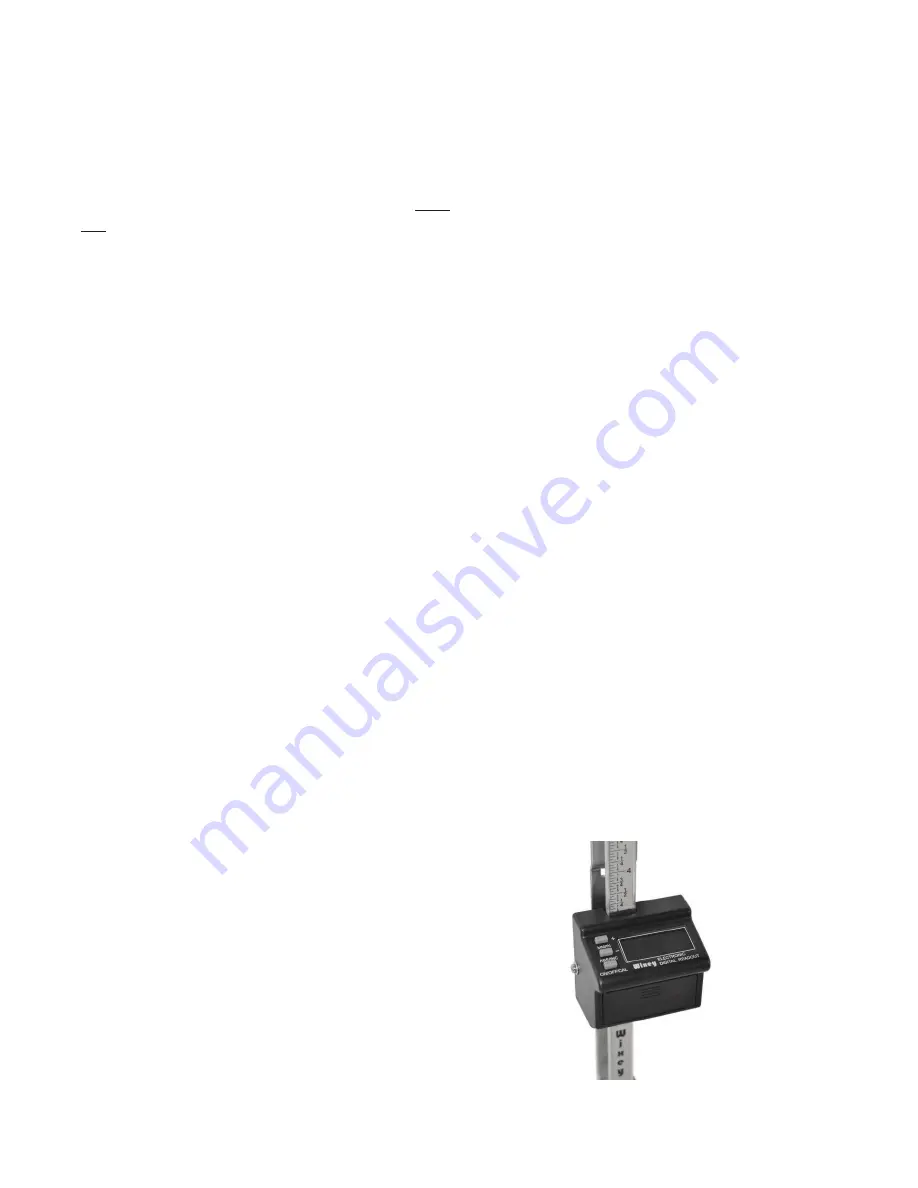
18
knob will come on when INTELLISAND is
operating. (Fig. 11 a) When the load is decreased,
INTELLISAND will automatically increase the feed
rate to the pre-selected speed. INTELLISAND
does
not
engage when brush sanding or if drum sanding at
a slower RPM than recommended.
Setting Brush Depth of Cut/Contact
When a nylon or wire brush is worn and needs
changing, the bristles will either have fractured and
the brush head looks “bald” or the bristle length
has worn and the bristles are too short for effective
brushing.
When an abrasive or cloth brush is worn, the brushing
material will become smooth, or the brush will be
considerably smaller in diameter as compared to new.
Please call SuperMax Tools if you have any questions.
Brush life can vary considerably, due to RPM, contact,
type of brush, and material being brushed.
Some types of brush heads, some flatter brushes, for
example, will allow changing of the brush material by
the operator.
When using a wire brush for “distressing” wood,
slowing brush RPM, using light contact and a
moderate feed rate generally will give the best finish
and longest brush life. When using a wire brush on
metal, it is important to use a light contact of the
bristle tips.
Nylon Brushes.
If a nylon brush
becomes uneven dressing the tips of bristle brush to
maintain uniform brush wear will be a benefit.
Dressing Instructions:
Staple or glue a wide sheet of 60 grit sandpaper to
a 1/2” thick fla
t wood surface. Strips of narrow
sandpaper can also be used. Lower the brush so the
tips of the bristles contact the sandpaper by
1/32”.
Set
the conveyor speed to approximately 50% feed rate.
Pass the abrasive loaded board through the machine
until the brush fibers are sharp and even.
Setting Drum Depth of Cut
Determining the depth of cut is the most
IMPORTANT set-up procedure before operating as
a drum sander.
It may take some experimentation to
determine the proper depth of cut, given the variables
of abrasive grit, type of wood, and conveyor feed rate.
Practicing on scrap before sanding a project can be
beneficial.
A good rule-of-thumb when sanding is to place the
workpiece under the drum and lower the sanding
head until the workpiece contacts the drum, but the
drum can still be rotated by hand. When making
successive passes, lower the sanding head no more
than the thickness of the grit abrasive, I.e., 1/8-1/16
of a turn for 80 grit and less for finer grits.
Note:
one
revolution of the height adjustment handle moves the
sanding head approximately
1/16”.
Depth Gauge Operation
The depth gauge (see Fig. 5) measures the distance
between the conveyor table and the bottom of the
sanding brush or drum. The sanding head must
be parallel to the conveyor bed surface. To calibrate
the depth gauge, loosen the two screws holding the
scale. Lower the brush or sanding head (with abrasive
installed) until the head touches the conveyor belt.
Slide the scale to align with the pointer at the “0”
mark. Tighten the two screws holding the scale. An
optional DRO (digital read out) for depth is available.
Fig. 12. This offers the most precise reading of sanded
thickness and allows for accurate repeatability of a
thickness. Great when making parts that must be an
exact thickness or when matching a thickness.
To operate, turn ON and select standard inch
“in”
or
metric millimeter
“mm”.
Lower drum, with abrasive
installed, until it touches the conveyor belt. Press
“zero” button to calibrate.
Fig. 12 Optional DRO
Summary of Contents for SuperMax 19-38 Combo
Page 1: ...19 38 Combo Brush Drum Sander Owner s Manual Lagunatools com SKU 219383...
Page 31: ...31...
Page 34: ...34 34...
Page 36: ...36...
Page 39: ...39...