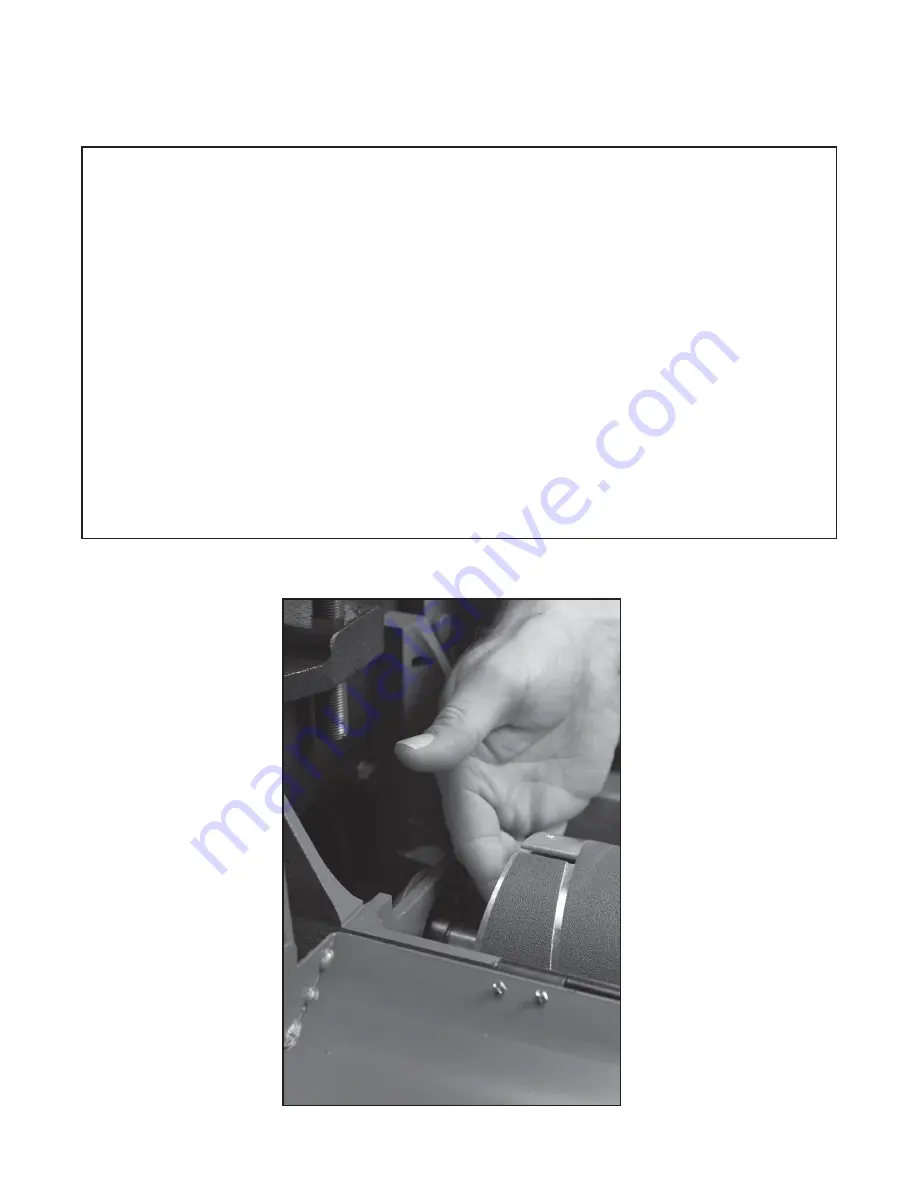
24
Fig. 15 Accessing inboard abrasive fastener
Abrasive Selection Guide
Grit Common Application
24 Grit
Abrasive planing, surfacing rough-sawn boards, maximum stock removal, glue removal.
36 Grit
Abrasive planing, surfacing rough-sawn boards, maximum stock removal, glue removal.
50 Grit
Surfacing and dimensioning boards, trueing warped boards.
60 Grit
Surfacing and dimensioning boards, trueing warped boards.
80 Grit
Light dimensioning, removal of planer ripples.
100 Grit
Light surfacing, removal of planer ripples.
120 Grit
Light surfacing, minimal stock removal.
150 Grit
Finish sanding, minimal stock removal.
180 Grit
Finish sanding only, not for stock removal.
220 Grit
Finish sanding only, not for stock removal.
Summary of Contents for SuperMax 19-38 Combo
Page 1: ...19 38 Combo Brush Drum Sander Owner s Manual Lagunatools com SKU 219383...
Page 31: ...31...
Page 34: ...34 34...
Page 36: ...36...
Page 39: ...39...