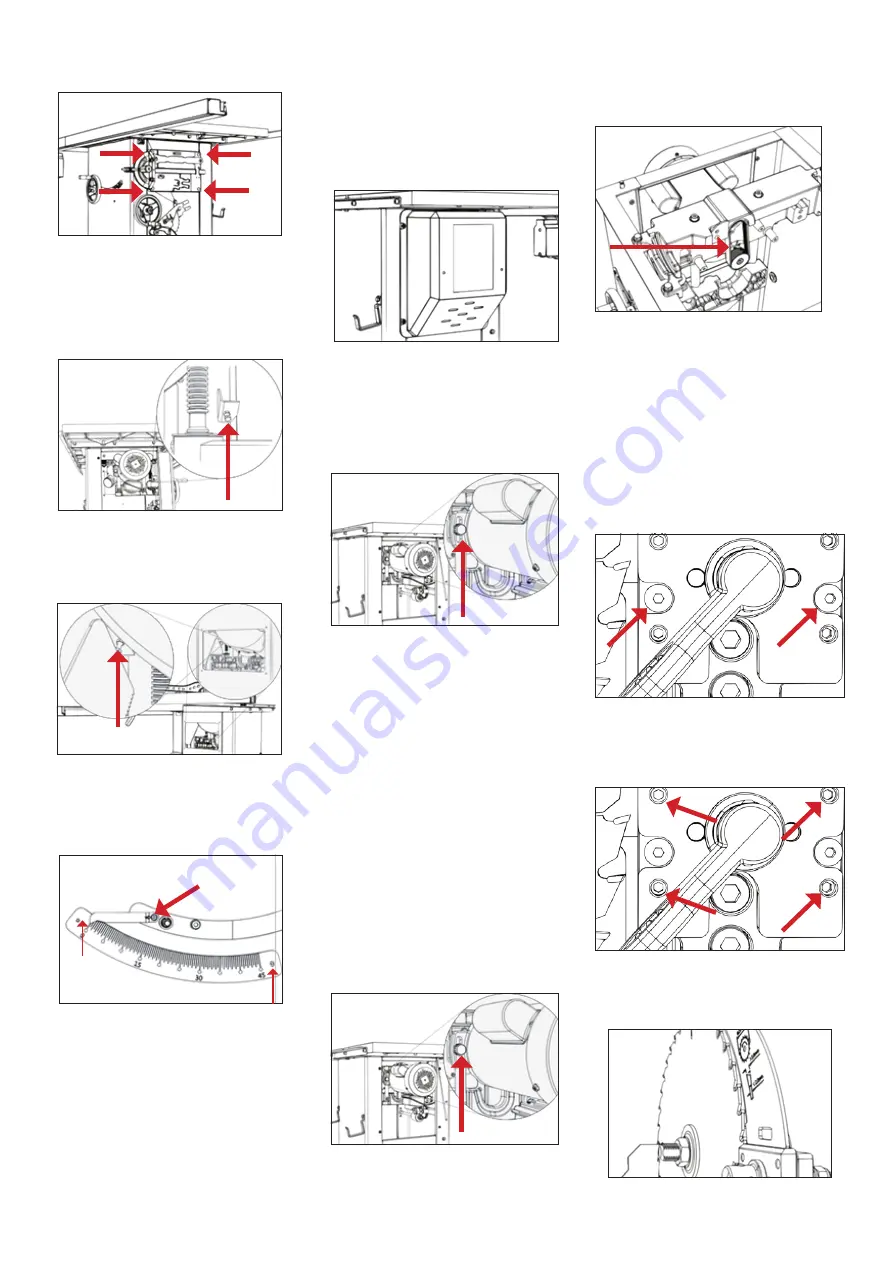
-14-
www.igmtools.com
3. Remove tool storage cover
To access the right-side tilt adjustment screw,
remove the tool storage using a #2 Philips head
driver. There are 4 screws in total holding on
the tool storage box.
4. Locate Tilt Adjustment
Locate the tilt adjustment screw. Screw it in to
expand the tilt range slightly.
5. Adjust as needed
Locate the tilt adjustment screw. Screw it in to
expand the tilt range slightly.
6. Adjust scale (if needed)
Adjust the scale and tilt indicator on the cabinet
if needed.
Adjusting the Belt:
It is good practice to check the tension of the
belt often to ensure that the saw is performing
properly. If the table saw blade is slipping or is
feeling underpowered, you may need to tighten
the belt. To do so, follow the steps below.
1. Unplug the table saw!
2. Remove the motor cover.
3. Locate belt adjustment bolt.
4. Tighten or loosen with weight of motor.
Use Caution: DO NOT OVERTIGHTEN BELT!
The weight of the motor is adequate to put
enough tension on the belt. Only tight enough
to prevent slippage.
Remove the motor cover
WARNING: MAKE SURE SAW IS
UNPLUGGED.
To access the motor, remove the motor housing
cover using a #2 Philips head driver. There are
4 screws in total holding on the motor cover.
Locating Belt Adjustment bolt
To adjust the belt, set blade to 0° on tilt scale,
then raise or lower blade to approximately 2“
above table. Loosen the belt adjustment bolt.
With the bolt loose, Raise or lower the motor so
that the belt is tight.
Changing the belt:
1. Unplug the table saw!
2. Remove all throatplates, blades, and blade
accessories.
3. Remove the motor cover.
4. Remove the dust shroud.
5. Loosen the Belt adjustment bolt and loosen
belt by raising motor.
6. Remove belt. NOTE: you may need to lower
the arbor height to access the belt.
7. Replace belt.
Use Caution: DO NOT OVERTIGHTEN BELT!
The weight of the motor is adequate to put
enough tension on the belt. Only tight enough
to prevent slippage.
Belt Adjustment bolt
WARNING: MAKE SURE SAW IS
UNPLUGGED. NOTICE: The drawing shown is
with the top of the table removed. AVOID
removing the table top. The belt can easily be
changed without removing the table top.
Accessing the Belt
7.4 Accessory Adjustments
Insert Block Adjustments (For all Safety
Accessories):
The Riving knife, blade guard, or splitter must
be aligned with the blade to be used affectively.
The riving knife should only be used with
blades specified on the riving knife. To adjust
the position of the blade safety attachments,
relative to the saw blade: NOTE: if the cam
action lever does not lock or is too hard to lock
– adjust the nut on the back side of the cam
action axil. You will need to remove the motor
cover.
Loosen the two middle setting bolts. These
two bolts fasten the assembly in-between the
set screws and the arbor block.
Adjust the set screws as needed to correct
an out of align blade attachment. Do small
adjustments and check.
Summary of Contents for Fusion2 2022
Page 2: ...2 www igmtools com...
Page 3: ...3 www igmtools com...
Page 18: ...18 www igmtools com Wiring Diagram Fusion 2 230V...
Page 19: ...19 www igmtools com Fence assembly...
Page 20: ...20 www igmtools com Mitre gauge blade guard...
Page 21: ...21 www igmtools com Motor and trunnion...
Page 22: ...22 www igmtools com Cabinet...