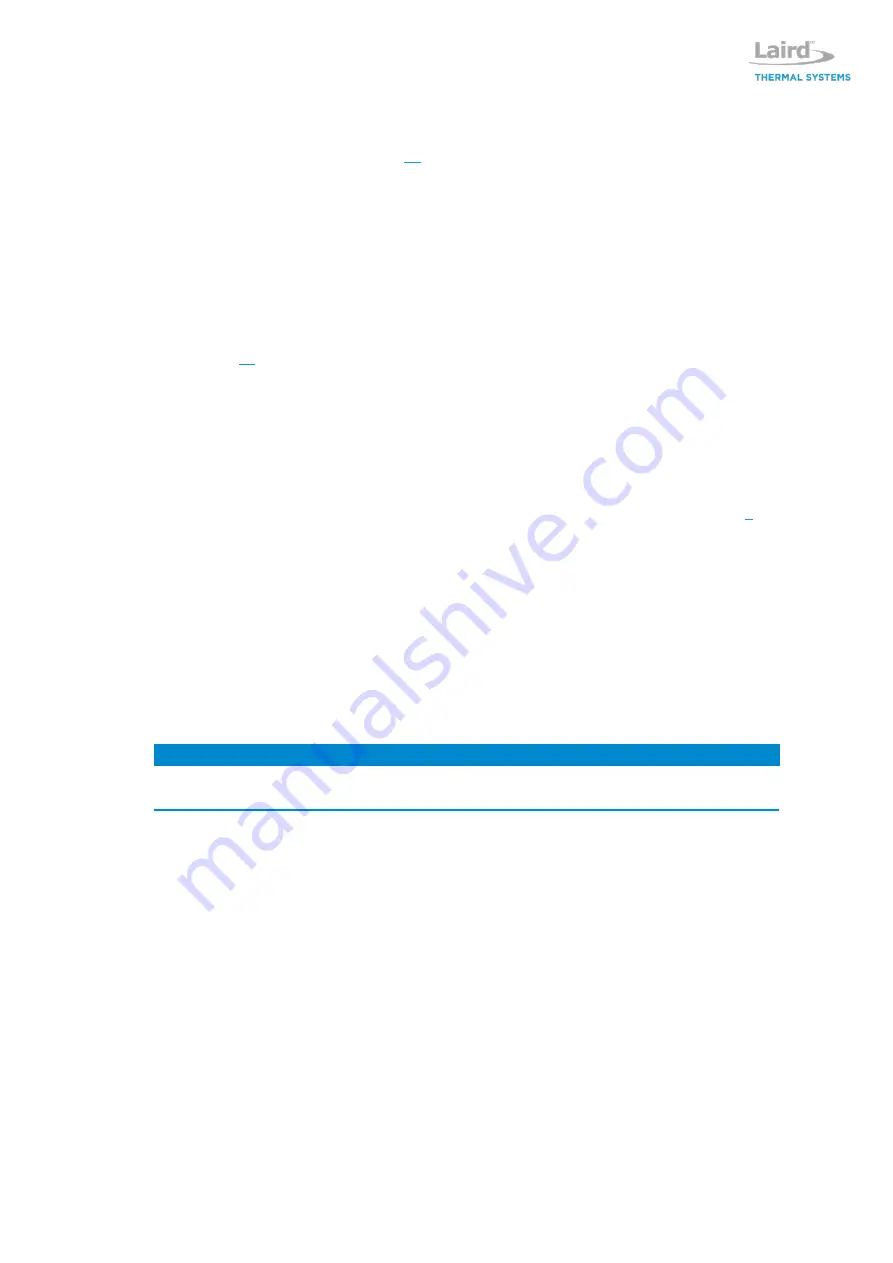
32
Re-packaging of the unit
The unit has been emptied (see chapter
6)
Lift the unit with a forklift or jack lift and place a transportable pallet under it.
7)
Enclose the unit including the transportable pallet with shrinking foil and shrink the foil tight.
The unit is ready for transportation.
Storing the Unit
The storage area must be even and the unit should not stand on an edge or other obstructive object.
The environmental conditions for storage of the unit or parts of it can be found in the specification
Disposal
The unit was manufactured mainly from recyclable material.
Make sure the components of the unit end up at a qualified company for disposal and recycling.
Contact Laird Thermal Systems for take back of end-of-life units (see company contact on page
ask a qualified company for disposal and recycling.
Disposal of Operating Materials
The operating materials of the unit can be hazardous to the environment and to health.
Make sure the operating materials are disposed of or recycled according to local regulations.
Also, the safety specifications of the coolant manufacturer must be obeyed.
Return of the unit to Laird Thermal Systems
NOTE
Declaration of decontamination
Before re-shipment of the unit a declaration of decontamination must be sent to Laird Thermal Systems.
Summary of Contents for WL3004
Page 1: ...WL3004 Liquid to Air Cooling System Specification and User Manual Version 1 2 ...
Page 35: ...35 Addendum Flow scheme ...
Page 36: ...36 Wiring diagram ...
Page 37: ...37 ...