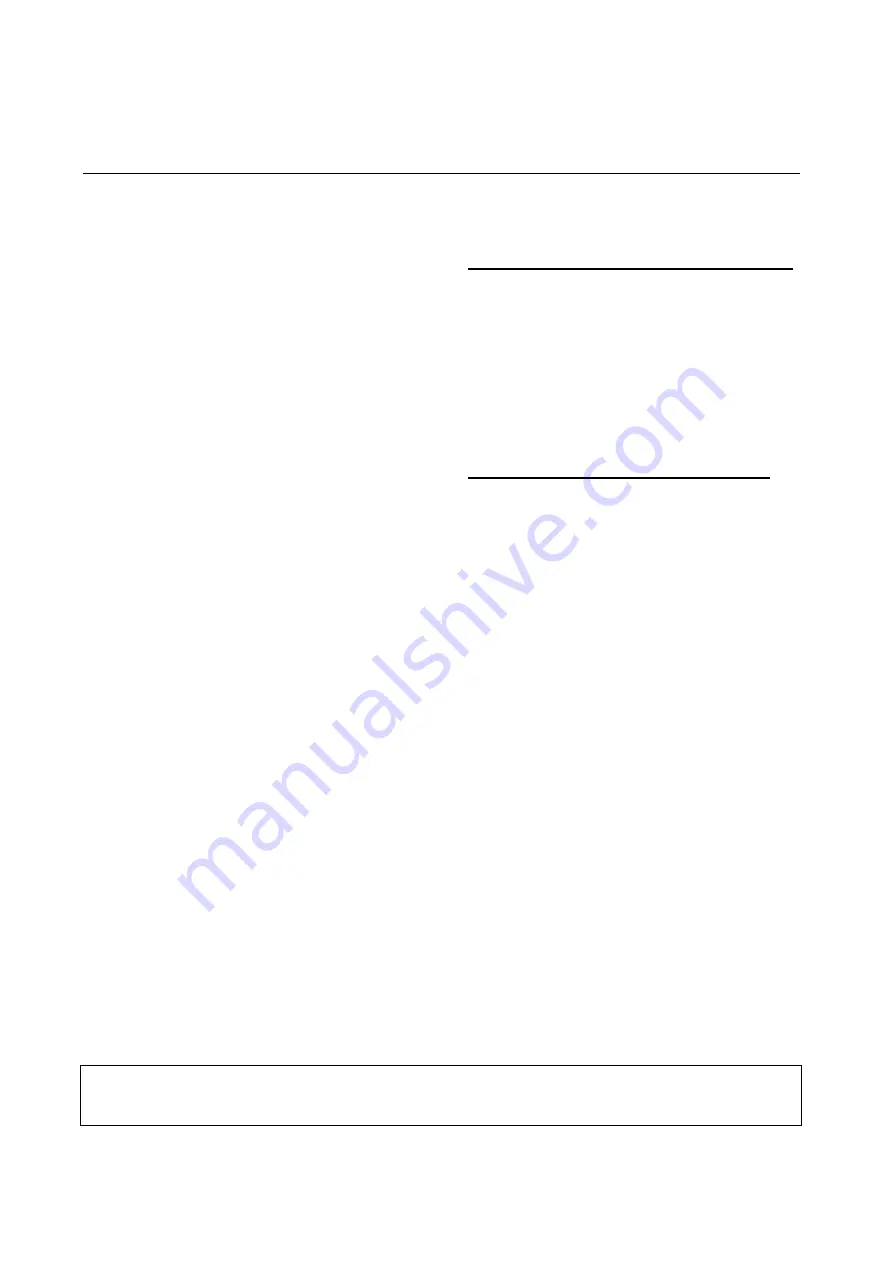
37
DRAWBACK
POSSIBLE CAUSES AND REMEDIES
If the drawback is not due to any of the
causes listed here above, proceed as follows:
In the case of electrical heating machines
1) check that the coil of remote control
switch MT3 is not broken.
2) check that the safety thermostat did
not
trigger.
3) check all elements of boiler heater.
In the case of steam heating machines
1) check that the steam inlet gate is open
and is present at a pressure not less than
0,5 bar (50 kPa).
2) check that the condensed steam
drainage filter is not clogged.
3) check that the steam solenoid valve
operates
correctly.
4) check that the inlet steam filter is not
clogged to such an extent as to prevent the
normal flow rate.
5) check that the condensed steam outlet
pipe can freely drain by drop.
6) check that the pipe coil is not scaled to
such an extent as to limit heat exchange
thereof.
The manufacturer declines any responsibility for any printing errors contained in this booklet. The
manufacturer also reserves the right to make any modifications to its products that don't affect the
basic characteristics thereof.
Summary of Contents for LP31-ek
Page 1: ...INSTRUCTIONS MANUAL POT WASHING MACHINE LP31 L ek...
Page 2: ...2...
Page 4: ...4...
Page 9: ...9 INSTRUCTIONS FOR THE USER...
Page 24: ......
Page 25: ......
Page 26: ......
Page 33: ...CONNECTIONS SCHEME Black Black Black Black Staples Black Black Staples...
Page 38: ...09 06 2017 11 45 00...
Page 39: ...09 06 2017 11 45 00...
Page 40: ...09 06 2017 11 45 01...
Page 41: ...09 06 2017 11 45 01...