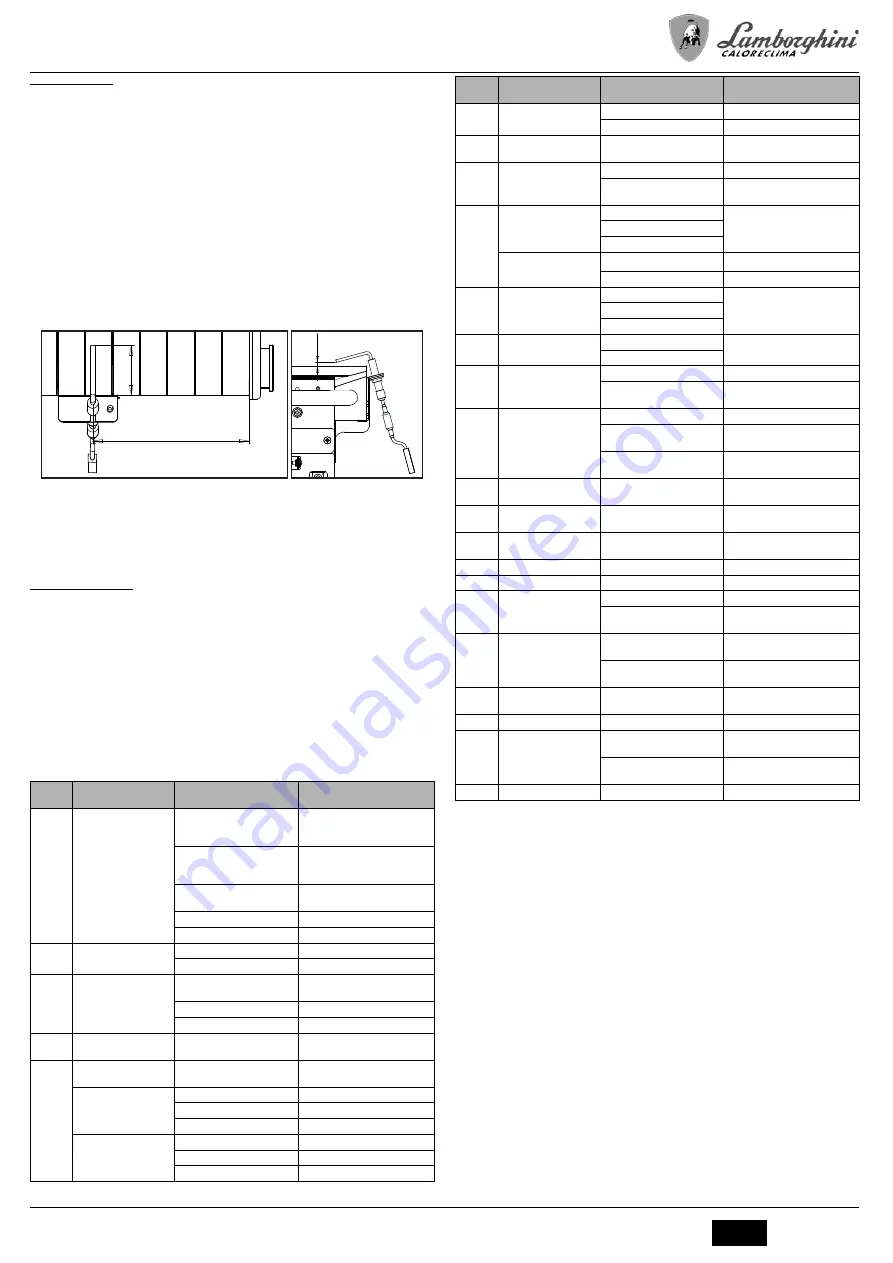
FL D CONDENS LN F24
41
EN
cod. 3541P661 - Rev. 00 - 06/2019
4.3 Maintenance
IMPORTANT
B
ALL MAINTENANCE WORK AND REPLACEMENTS MUST BE CARRIED
OUT BY SKILLED QUALIFIED PERSONNEL.
Before carrying out any operation inside the boiler, disconnect the power
and close the gas cock upstream. Otherwise there may be a danger of ex-
plosion, electric shock, suffocation or poisoning.
Periodical check
To ensure proper operation of the unit over time, have qualified personnel carry out a
yearly inspection, providing for the following checks:
•
The control and safety devices (gas valve, flow switch, thermostats, etc.) must func-
tion correctly.
•
The fume exhaust circuit must be perfectly efficient.
(Sealed chamber boiler: fan, pressure switch, etc. - The sealed chamber must be
tight: seals, cable glands, etc.)
(Open chamber boiler: anti-backflow device, fume thermostat, etc.)
•
The air-fume end piece and ducts must be free of obstructions and leaks
•
The burner and exchanger must be clean and free of deposits. For cleaning do not
use chemical products or wire brushes.
•
The electrode must be properly positioned and free of any deposits.
fig. 20- Electrode positioning
•
The gas and water systems must be tight.
•
The water pressure in the system when cold must be approx. 1 bar; otherwise bring
it to that value.
•
The circulating pump must not be blocked.
•
The expansion vessel must be filled.
•
The gas flow and pressure must match that given in the respective tables.
4.4 Troubleshooting
Diagnostics
The boiler has an advanced self-diagnosis system. In case of a boiler fault, the display
will flash together with the fault symbol (detail 11 - fig. 1) indicating the fault code.
There are faults that cause permanent shutdowns (marked with the letter "
A
"): to restore
operation, press the RESET button (detail 6 - fig. 1) for 1 second or RESET on the op-
tional remote timer control if installed. At this point the display will show
“d4”
for about
30 seconds
or
“d5”
for about
5 minutes
which indicates the waiting time after which the
boiler will resume normal operation. if the boiler fails to restart, it is necessary to eliminate
the fault.
Other faults cause temporary shutdowns (marked with the letter “
F
”) which are automat-
ically reset as soon as the value returns within the boiler's normal working range.
List of faults
Table. 8
Fault
code
Fault
Possible cause
Cure
A01
No burner ignition
No gas
Check the regular gas flow to the
boiler and that the air has been elimi-
nated from the pipes
Ignition/detection electrode fault
Check the wiring of the electrode and
that it is correctly positioned and free
of any deposits
Faulty gas valve
Check the gas valve and replace it if
necessary
Gas valve wiring disconnected
Check the wiring
Ignition power too low
Adjust the ignition power
A02
Flame present signal with
burner off
Electrode fault
Check the ionization electrode wiring
Card fault
Check the card
A03
Overtemperature protec-
tion activation
Heating sensor damaged
Check the correct positioning and
operation of the heating sensor
No water circulation in the system Check the circulating pump
Air in the system
Vent the system
F04
Card parameter fault
Wrong card parameter setting
Check the card parameter and modify
it if necessary
F05
Card parameter fault
Wrong card parameter setting
Check the card parameter and modify
it if necessary
Fan fault
Wiring interrupted / disconnected Check the wiring
Faulty fan
Replace the fan
Card fault
Replace the card
Hall sensor fault
Wiring interrupted / disconnected Check the wiring
Faulty sensor
Check / replace the sensor
Card fault
Replace the card
3
±
0,5
97
31
A06
No flame after the ignition
phase
Low pressure in the gas system
Check the gas pressure
Burner minimum pressure setting Check the pressures
F07
Card parameter fault
Wrong card parameter setting
Check the card parameter and modify
it if necessary
A09
Gas valve fault
Wiring disconnected
Check the wiring
Faulty gas valve
Check the gas valve and replace it if
necessary
F10
Delivery sensor 1 fault
Sensor damaged
Check the wiring or replace the sen-
sor
Connector disconnected
Wiring disconnected
Fume thermostat interven-
tion
No system H
2
O circulation
Check the circulating pump
Air in the system
Vent the system
F11
DHW sensor fault
Sensor damaged
Check the wiring or replace the sen-
sor
Wiring shorted
Wiring disconnected
F14
Delivery sensor 2 fault
Sensor damaged
Check the wiring or replace the sen-
sor
Wiring shorted
A16
Gas valve fault
Wiring disconnected
Check the wiring
Faulty gas valve
Check the gas valve and replace it if
necessary
F20
Combustion control fault
Fan fault
Check the fan and fan wiring
Wrong baffle
Check the baffle and replace it if nec-
essary
Flue obstructed or not correctly
sized
Check the flue
A21
Poor combustion fault
Fault F20 generated 6 times in the
last 10 minutes
See fault F20
A23
Card parameter fault
Wrong card parameter setting
Check the card parameter and modify
it if necessary
A24
Card parameter fault
Wrong card parameter setting
Check the card parameter and modify
it if necessary
F34
Supply voltage under 180V. Electric mains trouble
Check the electrical system
F35
Faulty mains frequency
Electric mains trouble
Check the electrical system
F37
Incorrect system water
pressure
Pressure too low
Fill the system
Water pressure switch damaged
or disconnected
Check the sensor
F39
External probe fault
probe damaged or wiring shorted
Check the wiring or replace the sen-
sor
probe disconnected after activat-
ing the sliding temperature
Reconnect the external probe or disa-
ble the sliding temperature
A41
Sensor positioning
Delivery sensor or DHW sensor
detached from the pipe
Check the correct positioning and
operation of the sensors
F42
Heating sensor fault
Sensor damaged
Replace the sensor
F50
Gas valve fault
Modulating Operator wiring dis-
connected
Check the wiring
Faulty gas valve
Check the gas valve and replace it if
necessary
A51
Poor combustion fault
Inlet/exhaust flue obstruction
Check the flue
Fault
code
Fault
Possible cause
Cure