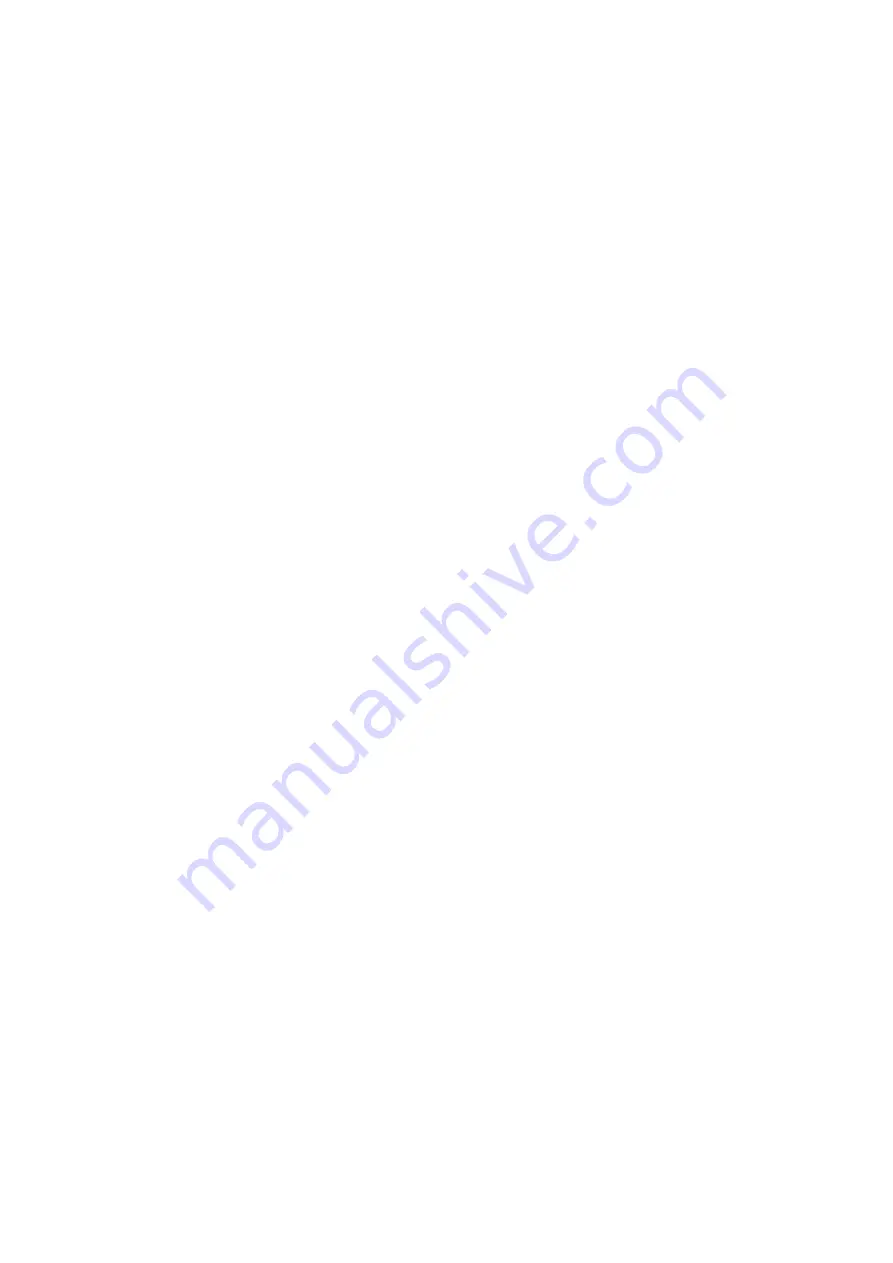
The power supply voltage must be at least 180Vac in order to allow a starting cycle to be performed.
If the network voltage falls below 156Vac, the appliance stops and signals the anomaly.
The starting cycle can only be carried out again if the power supply voltage exceeds 180Vac.
Protection in case of high power supply voltage
The power supply voltage must be at below 275Vac in order to allow a starting cycle to be performed.If the network voltage
exceeds 280Vac, the appliance stops and signals the anomaly.
The starting cycle can only be carried out again if the power supply voltage falls below 275Vac.
Functioning in manual mode for burner calibration
(delegated to authorised staff).
It the appliance is not in the block state, it is possible to force the MANUAL functioning mode by acting on the button on the
board or on the remote release button.
In fact, by pressing the button 3 times (on the board or remote reset) access the green fast flashing display; another press
causes the activation of the MANUAL functioning mode.In this phase, the appliance initiates the start-up cycle or remains
functioning independently from the status of the heat request thermostat and the functioning regulator.
It the appliance is not in the block state, it is possible to force the MANUAL functioning mode by acting on the button on the
board or on the remote release button.
In fact, by pressing the button 3 times (on the board or remote reset) access the green fast flashing display; another press
causes the activation of the MANUAL functioning mode.In this phase, the appliance initiates the start-up cycle independently
from the status of the heat request thermostat and the functioning regulator.
Once the functioning position has been reached, it is possible to pass from one functioning stage to the next by just acting on
the button.
At every press and release of the button, pass to the next intermediate stage until reaching the third stage (three-stage burner).
Press again to return to the previous until reaching the first stage position.
(If the two-stage burner passes from the first stage position to the second stage position and vice versa).
(If the modulating burner passes from the minimum modulation position to the maximum modulation position and vice versa).
During the MANUAL functioning phase, the number of yellow flashings indicate the current functioning status (1 flash = first
stage or minimum modulation, 2 flashes = second stage or maximum modulation, 3 flashes = third stage).
If the signal becomes flashing red during MANUAL functioning, check the position of the servo-motor cam (cam position ano-
maly signal); the burner will however remain in functioning mode.
The procedure must be repeated to deactivate the manual functioning mode.It is also possible to deactivate the manual fun-
ctioning mode by not acting on the button until the relative timeout has expired (see table of times).The function in question
can only be activated by accessing the INSTALLER MENU.
Servo-motor self-learning
The board can automatically acquire the times relative to the damper control servo-motor, it is therefore not necessary to
perform any calibration.
It is however necessary to use servo-motors with 0-90° run times no less than 2s and not exceeding 120s.
Feedback verification and sequence control
If there is no feedback signal relative to reaching a determined position by the air damper, the system performs a block shut-
down and signals the anomaly (block due to servo-motor anomaly).
Also present is a control of the arrival sequence of the feedback signals to the appliance.
If an incorrect arrival sequence of the appliance damper position signals occurs, the appliance will perform a block shutdown
(block due to servo-motor anomaly).
Monitoring of functioning
The board provides the continuous monitoring of the functioning status of the motor and solenoid valves.
MOTORIf there is no monitor signal or incorrect signal presence, at least 3 attempts are made to perform the start-up cycle. If
this anomaly persists, the board will carry out a block shutdown (burner control anomaly).
SOLENOID VALVESIf there is no monitor signal, at least 3 attempts are made to perform the start-up cycle. If this anomaly
persists, the board will carry out a block shutdown (burner control anomaly).If there is an incorrect monitor signal, the board
performs an immediate block shutdown (burner control anomaly).
Block shutdown and rearm
The button allows the reset of the appliance if it is in the block state.The appliance is released when the button is pressed and
then released (button on board or external release button).
The appliance can be released by the button on the board of the external release button.For the appliance to be released, the
button must be pressed for a period of time exceeding 0.2s but less than 4s.
In the case of block shutdown with manual rearm, 5 consecutive rearm operations are possible.
After which rearm is possible again:
- after 1 h ( n° 1 additional rearm is allowed every hour).
- removing the mains power supply.
The rearm operation is only possible if the appliance is supplied with mains voltage.Intermittent serviceThe board performs a
regulation shutdown with self-diagnosis at least every minimum 18h - maximum 24h.