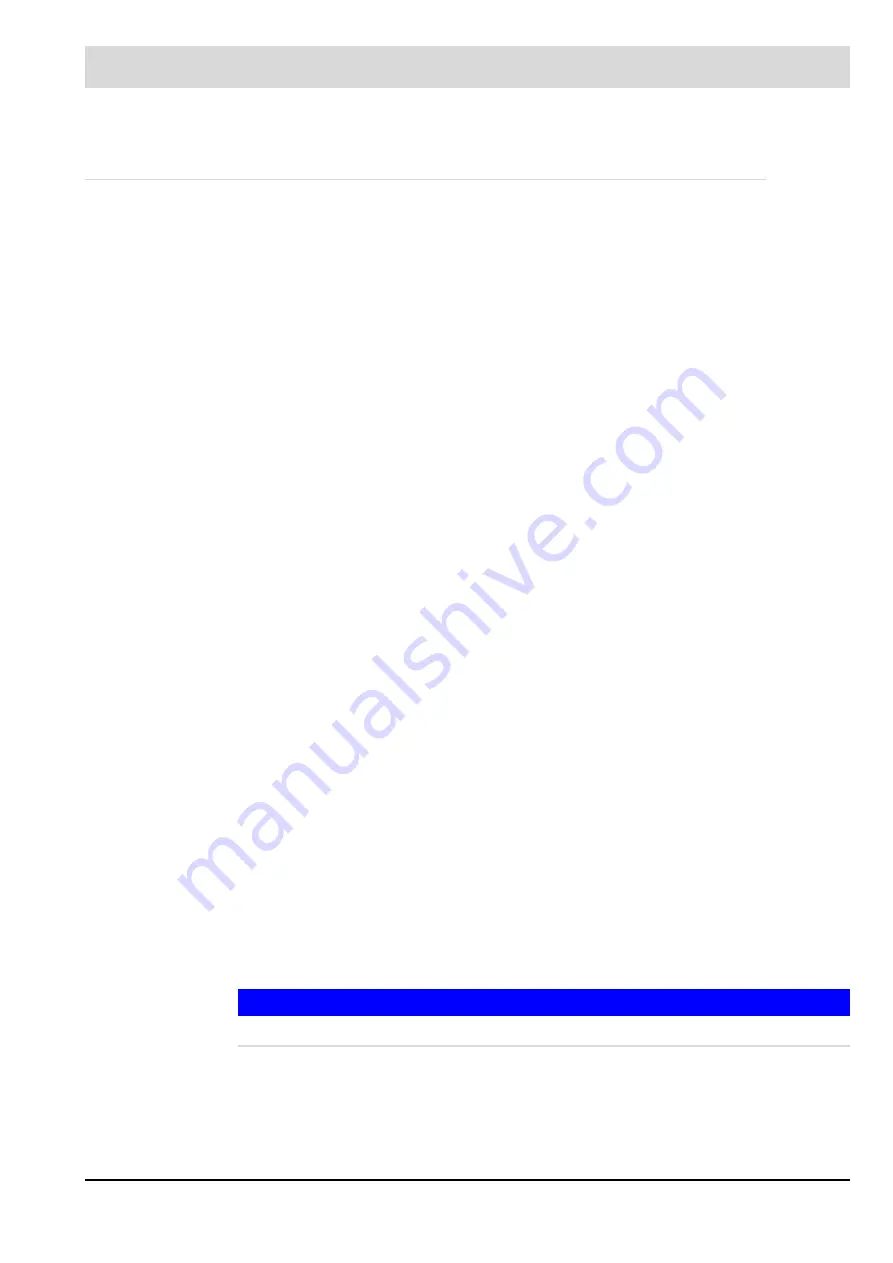
10
2
General Safety Instructions
2.2
Product-specific Dangers
Please observe the safety instructions to avoid personal injury and damage to property and
the environment!
The BT300 is a safety device! The device must not be opened, interfered with or modified.
LAMTEC assumes no liability for damages arising as a result of unauthorised interference!
•
After commissioning and after each maintenance action check the exhaust gas values
across the entire power range.
•
Qualified specialist staff are required to carry out all activities (assembly, installation, ser-
vicing, etc.).
•
The burner or boiler manufacturer will ensure that the BT300 base unit is compliant with
protection class IP40 or IP54 for outdoor use in accordance with DIN EN 60 529.
•
The hazard risk in the event of external fire, traffic, wind, tidal waves and earthquakes de-
pends on the installation situation and the location of the gas appliance. It shall be as-
sessed separately where appropriate.
•
Before working in the connection area, switch off the power supply to the plant from all
poles. Ensure that it cannot be switched back on and that the plant is voltage-free. There
is a risk of electric shock when the plant is not switched off.
•
Place and secure the protection against contact on the BT300 and on all connected elec-
trical parts. The cover must fulfil the design, stability and protection requirements of
EN 60730.
•
Plug connectors X30 - X34 have no protective separation from the mains voltage. To re-
place or disconnect the plug connectors, all poles of the plant must be disconnected from
the mains.
•
After each activity (e.g. assembly, installation, servicing, etc.) check wiring and
parameters to make sure it is in good working condition.
•
If the equipment is dropped or suffers impact, you should no longer commission it. The
safety functions may also be impaired but fail to show any obvious external damage.
•
When the ratio curves are being programmed, the adjuster will continually monitor the
quality of the plant's combustion (e.g. using an exhaust gas analysis station). In the event
that the combustion values are inadequate or the conditions are potentially harmful, the
adjuster will take suitable action, e.g. switch off the system manually.
•
These operating instructions describe many possible applications and functions and
should be used as guidelines. Carry out functional tests on the test bench and/or in the
plant application to ensure correct functioning and document the results.
Follow additional instructions to guarantee safety and reliability while operating the BT300:
•
Condensation and humidity are to be avoided. If necessary, make sure that the installation
is sufficiently dry before you switch it on.
•
Avoid static charge having a destructive effect in case of touching the device's electronic
components.
NOTICE
Use ESD equipment while working on electrics/electronics.
•
The external safety devices are not monitored during continuous fan ventilation (post-
purge) after a normal shutdown. This means the combustion air fan cannot be switched
off by actuating a hazard switch interconnected in the burner safety interlock chain. For
this reason, additional measures must be taken in the combustion system for the emer-
gency shutdown of the combustion air fan.
Summary of Contents for BT300 BurnerTronic
Page 2: ......
Page 25: ...24 3 Product Description Fig 3 9 Temperature derating BT300 for operation 2000 m NHN...
Page 49: ...48 4 Design and Functions Fig 4 20 Oil with pilot burner BT300...
Page 50: ...49 4 Design and Functions Fig 4 21 Oil without pilot burner BT300...
Page 51: ...50 4 Design and Functions Fig 4 22 Gas with pilot burner and leakage test BT300...
Page 52: ...51 4 Design and Functions Fig 4 23 Gas without pilot burner and leakage test BT300...
Page 53: ...52 4 Design and Functions Fig 4 24 Oil without pilot burner BT335...
Page 54: ...53 4 Design and Functions Fig 4 25 Gas without pilot burner and leakage test BT335...
Page 59: ...58 4 Design and Functions Fig 4 28 Leakage test process diagram...
Page 98: ...97 6 Operating Control and Displays...
Page 99: ...98 6 Operating Control and Displays...
Page 103: ...102 6 Operating Control and Displays...
Page 105: ...104 6 Operating Control and Displays...
Page 106: ...105 6 Operating Control and Displays...
Page 107: ...106 6 Operating Control and Displays...
Page 109: ...108 6 Operating Control and Displays...
Page 126: ...125 6 Operating Control and Displays 6 3 4 2 Curve Table Fig 6 37 Curve table window...
Page 246: ...242 10 EU Declaration of Conformity 10 EU Declaration of Conformity...
Page 247: ...243 10 EU Declaration of Conformity...