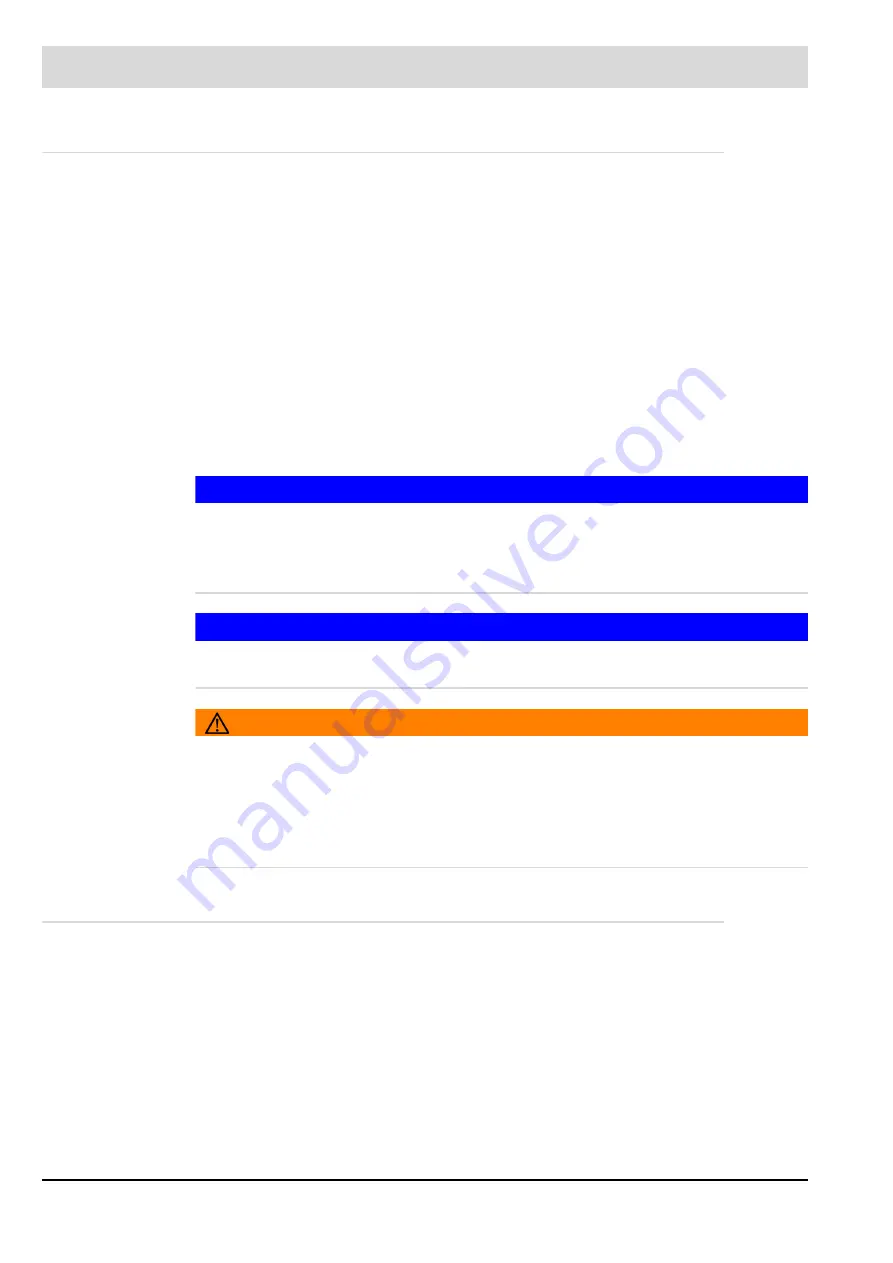
11
2
General Safety Instructions
2.2.1
Commissioning Notes
•
During commissioning it is essential to observe all safety accessory.
•
There is no way to completely rule out the connection plugs being connected incorrectly.
For this reason, check the correct assignment of the plugs before commissioning the
plant.
•
The person responsible for the plant/commissioning engineer must document the follow-
ing values after installing and commissioning a plant:
–
Settings/changes to the parameters
–
Setting values across the burner firing-rate range (e.g. curve progressions),
–
corresponding exhaust gas values where applicable
–
media pressure levels where applicable
You can partly use CMS Remote Software to print this data or alternatively keep a hand-
written note of it.
If tests are to be required by third parties in the application area of the device, these doc-
uments must be retained for presentation on request.
NOTICE
In BT300, parameter settings deviating from the application standards can be made.
The parameter settings must correspond to the relevant application standards as applica-
ble (e.g. EN 298, EN 676, EN 267, etc.) The documented evidence of conformity can be
managed via the LSB remote software.
NOTICE
Safety times can be called up via the HMIs UI400 and GUI607/GUI610/GUI615 and the CMS
Remote Software.
WARNING!
No interlocking when opening the safety interlock chains in BURNER OFF mode!
When opening the safety interlock chains in BURNER OFF mode, the BT300 does not per-
form any interlocking. The BT300 only prevents the burner from starting until the safety chains
are closed.
Measures must be taken on the system side if the application requires the plant to be
interlocked when a safety chain is opened even in BURNER OFF mode
2.2.1.1 Electronic Ratio Control
•
Guarantee proper operation by ensuring adequate excess air.
In order to do this, set the values for fuel and combustion air in such a way that
–
combustion chamber pressure
–
fuel pressure
–
temperature and pressure of the combustion air
can ensure proper, stable operation through the entire range of burner firing rate until next
periodic inspection.
•
Pay attention to wear and tear of actuators and actuator elements.
•
Measure characteristic values of combustion process to document proper operation.
•
Observe the maintenance cycle for readjustment of the electronic ratio control depending
on tolerances and operating times.
Summary of Contents for BT300 BurnerTronic
Page 2: ......
Page 25: ...24 3 Product Description Fig 3 9 Temperature derating BT300 for operation 2000 m NHN...
Page 49: ...48 4 Design and Functions Fig 4 20 Oil with pilot burner BT300...
Page 50: ...49 4 Design and Functions Fig 4 21 Oil without pilot burner BT300...
Page 51: ...50 4 Design and Functions Fig 4 22 Gas with pilot burner and leakage test BT300...
Page 52: ...51 4 Design and Functions Fig 4 23 Gas without pilot burner and leakage test BT300...
Page 53: ...52 4 Design and Functions Fig 4 24 Oil without pilot burner BT335...
Page 54: ...53 4 Design and Functions Fig 4 25 Gas without pilot burner and leakage test BT335...
Page 59: ...58 4 Design and Functions Fig 4 28 Leakage test process diagram...
Page 98: ...97 6 Operating Control and Displays...
Page 99: ...98 6 Operating Control and Displays...
Page 103: ...102 6 Operating Control and Displays...
Page 105: ...104 6 Operating Control and Displays...
Page 106: ...105 6 Operating Control and Displays...
Page 107: ...106 6 Operating Control and Displays...
Page 109: ...108 6 Operating Control and Displays...
Page 126: ...125 6 Operating Control and Displays 6 3 4 2 Curve Table Fig 6 37 Curve table window...
Page 246: ...242 10 EU Declaration of Conformity 10 EU Declaration of Conformity...
Page 247: ...243 10 EU Declaration of Conformity...