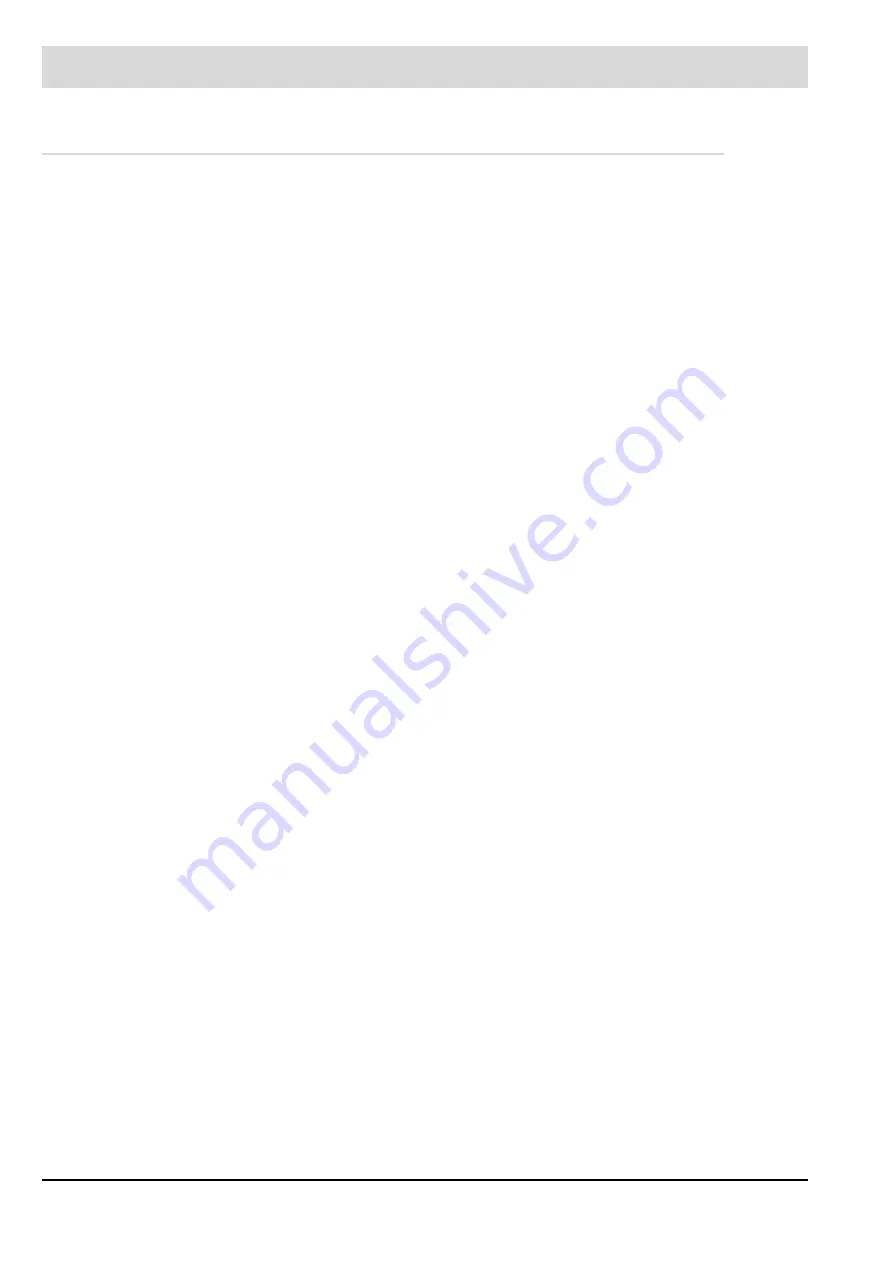
15
2
General Safety Instructions
2.4
Installation Notes
•
Lay high-voltage ignition cable always separately and in safe distance from device and
other cables.
•
Only trained, qualified personnel may open the BurnerTronic’s cover.
•
Observe local and national regulations when wiring the electric cables inside the burner.
•
Tighten the screw terminals of the BT300 using a tightening torque of > 0.5 Nm.
•
Supply the feed cable with L, N and PE only. The N neutral conductor must not have po-
tential difference to the PE protective conductor.
•
The pre-fuse for the BT300 should be max.10 A slow-blow.
•
Phase and neutral conductors must not be interchanged (this would lead to dangerous
malfunctioning, loss of protection against contact, etc.).
•
The strain relief for the connected cables must comply with standards (e.g. DIN EN 60730
and DIN EN 60335).
•
Make sure that no spliced strands can come into contact with any of the adjacent connec-
tions. Use appropriate end sleeves.
•
The burner manufacturer is obligated to supply unused connections on the BT300 with
dummy plugs.
•
To replace or disconnect the plug connectors, all poles of the plant must be disconnected
from the mains.
•
Make a form-fit connection between the actuators and actuating elements for fuel and
combustion air, as well as a form-fit connection for any additional actuator element.
•
Optional components with safety extra low voltage (SELV) must be safely separated from
the mains. Otherwise this can cause an electrical shock or damage the device due to a
short-circuit.
•
You may connect only passive devices or devices without feedback effects at the 230V
outputs of the BT300 (like relays without additional voltage connection). In case of error it
must be guaranteed that BT300 is not fed with 230 V by this terminals.
•
To avoid disruption of the UI300’s display during ignition, a damping resistor of 1 ... 5 k
must be installed in the high-voltage ignition line.
•
To avoid disturbance on the Bus, the termination must be active on the first and the last
device connected to the bus must be terminated.
Summary of Contents for BT300 BurnerTronic
Page 2: ......
Page 25: ...24 3 Product Description Fig 3 9 Temperature derating BT300 for operation 2000 m NHN...
Page 49: ...48 4 Design and Functions Fig 4 20 Oil with pilot burner BT300...
Page 50: ...49 4 Design and Functions Fig 4 21 Oil without pilot burner BT300...
Page 51: ...50 4 Design and Functions Fig 4 22 Gas with pilot burner and leakage test BT300...
Page 52: ...51 4 Design and Functions Fig 4 23 Gas without pilot burner and leakage test BT300...
Page 53: ...52 4 Design and Functions Fig 4 24 Oil without pilot burner BT335...
Page 54: ...53 4 Design and Functions Fig 4 25 Gas without pilot burner and leakage test BT335...
Page 59: ...58 4 Design and Functions Fig 4 28 Leakage test process diagram...
Page 98: ...97 6 Operating Control and Displays...
Page 99: ...98 6 Operating Control and Displays...
Page 103: ...102 6 Operating Control and Displays...
Page 105: ...104 6 Operating Control and Displays...
Page 106: ...105 6 Operating Control and Displays...
Page 107: ...106 6 Operating Control and Displays...
Page 109: ...108 6 Operating Control and Displays...
Page 126: ...125 6 Operating Control and Displays 6 3 4 2 Curve Table Fig 6 37 Curve table window...
Page 246: ...242 10 EU Declaration of Conformity 10 EU Declaration of Conformity...
Page 247: ...243 10 EU Declaration of Conformity...