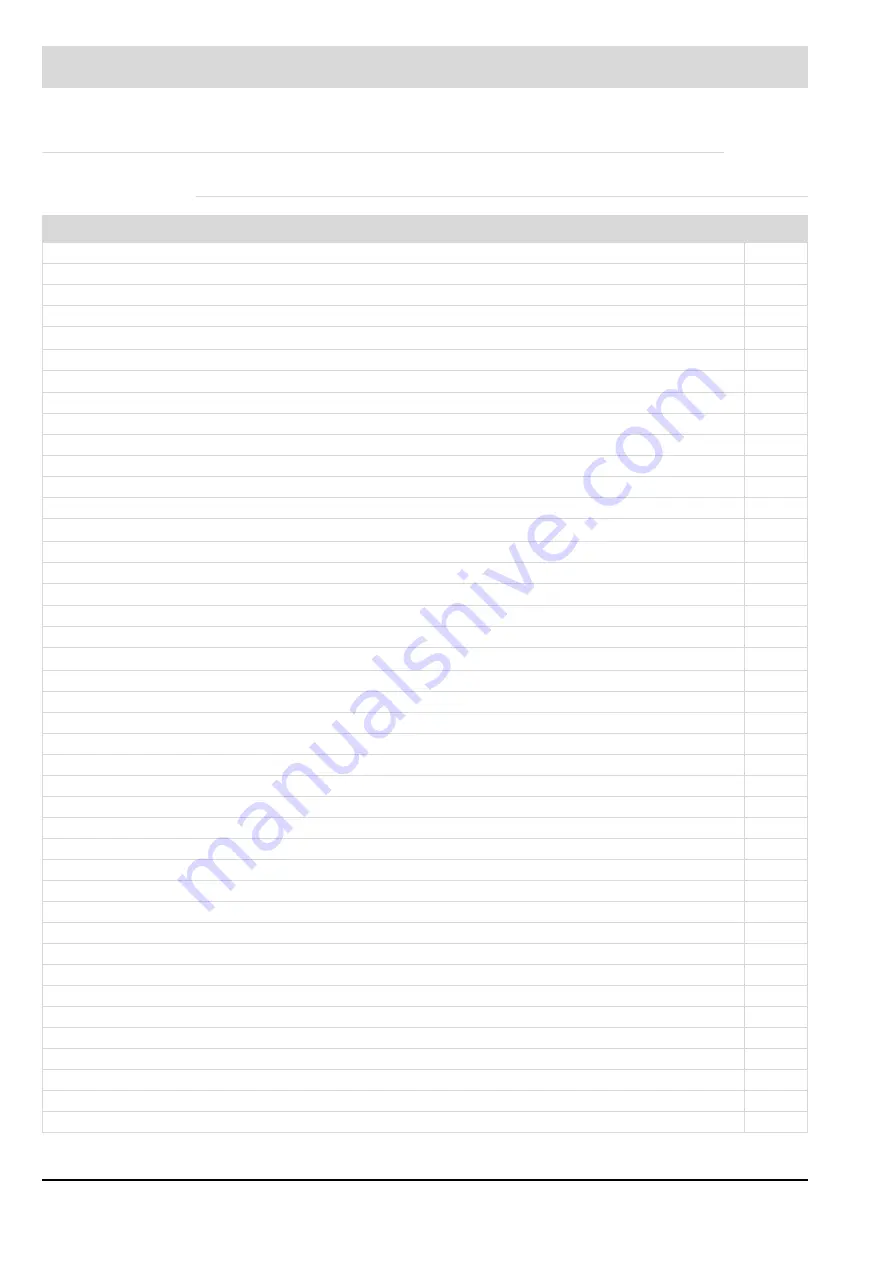
235
8
Options
8.5.4.6 Coding: O
2
Controller Operating Mode
Coding: O
2
Controller Operating Mode for BT300
Tab. 8-16 Bit encoding: O
2
trim operating mode with BT300
Description
Value
Not used
0
O
2
trim: internal error
1
Automatic deactivation: A temporary fault lasts for more than one hour.
2
Curve set change is running
3
Inactive in mode O
2
SETTING
4
Inactive in mode O
2
SETTING – external correction presetting (CO or O
2
)
5
Fault of setpoint curve in EEP (fault detection during curve set change)
6
Fault of setpoint curve in EEP (fault detection during curve set change)
7
Setpoint curve is empty (<3 points) (during curve set change)
8
O
2
trim is inactive in curve set
9
O
2
trim is inactive in BURNER OFF
10
O
2
trim is inactive in SETTING/DELETE MEMORY
11
O
2
trim is inactive because the O
2
value is too small during pre-purge
12
O
2
trim is inactive because the O
2
value is too big during pre-purge
13
O
2
trim is inactive because the O
2
value is too big after ignition
14
O
2
trim – pre-purge and ignition process
15
Fault in setpoint curve running time
16
Fault in optimisation curve running time
17
Failure in O
2
actual value input
18
Controller is deactivated by external presetting
19
Controller is inactive – indication only (P 896)
20
Waiting time after ignition is running
21
Waiting time for curve change is running
22
Permanent air deficiency
23
1
st
lower monitoring band
24
1
st
upper monitoring band
25
Permanent probe dynamics
26
Dynamic air deficiency
27
Dynamic probe dynamics
28
The half of air deficiency
29
O
2
trim is inactive because the firing rate is outside of the O
2
firing rate range
30
O
2
trim: Setting the test mode (external setpoint presetting)
31
O
2
trim is active
32
CO controller is active
33
Mode presetting: No presetting available from this source
34
The correction output exceeds the permissible value for a long time
35
Controller is deactivated by parameter
36
Controller is deactivated by LSB message
37
Switching from O
2
trim to CO control is running
38
Switching from CO control to O
2
trim is running
39
Control mode of SiCarboSen
40
CO controller fault
255
Summary of Contents for BT300 BurnerTronic
Page 2: ......
Page 25: ...24 3 Product Description Fig 3 9 Temperature derating BT300 for operation 2000 m NHN...
Page 49: ...48 4 Design and Functions Fig 4 20 Oil with pilot burner BT300...
Page 50: ...49 4 Design and Functions Fig 4 21 Oil without pilot burner BT300...
Page 51: ...50 4 Design and Functions Fig 4 22 Gas with pilot burner and leakage test BT300...
Page 52: ...51 4 Design and Functions Fig 4 23 Gas without pilot burner and leakage test BT300...
Page 53: ...52 4 Design and Functions Fig 4 24 Oil without pilot burner BT335...
Page 54: ...53 4 Design and Functions Fig 4 25 Gas without pilot burner and leakage test BT335...
Page 59: ...58 4 Design and Functions Fig 4 28 Leakage test process diagram...
Page 98: ...97 6 Operating Control and Displays...
Page 99: ...98 6 Operating Control and Displays...
Page 103: ...102 6 Operating Control and Displays...
Page 105: ...104 6 Operating Control and Displays...
Page 106: ...105 6 Operating Control and Displays...
Page 107: ...106 6 Operating Control and Displays...
Page 109: ...108 6 Operating Control and Displays...
Page 126: ...125 6 Operating Control and Displays 6 3 4 2 Curve Table Fig 6 37 Curve table window...
Page 246: ...242 10 EU Declaration of Conformity 10 EU Declaration of Conformity...
Page 247: ...243 10 EU Declaration of Conformity...