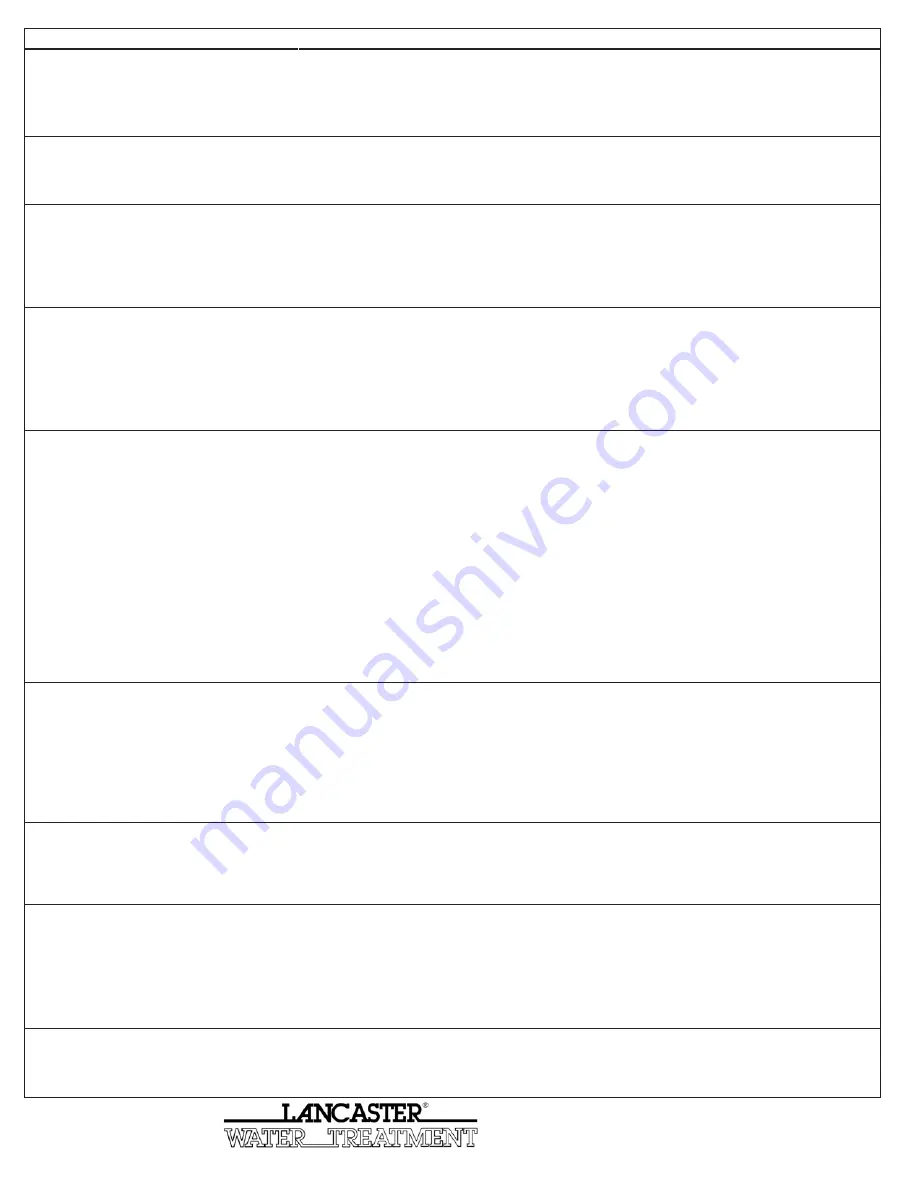
PAGE 12
7/14
A DIVISION OF C-B TOOL CO.
1340 MANHEIM PIKE ● LANCASTER PA 17601-3196 ● TEL:717-397-3521 ● FAX: 717-392-0266
www.lancasterwatertreatment.com ● E-mail: info@lancasterpump.com
TROUBLESHOOTING PROCEDURES
PROBLEM
POSSIBLE CAUSE
SOLUTION
1. Timer does not display time of
day.
a. Transformer unplugged
a. Connect power
b. No electric power at outlet
b. Repair outlet or use working outlet
c. Defective transformer
c. Replace transformer
d. Defective PC board
d. Replace PC board
2. Timer does not display correct time of
day.
a. Switched outlet
a. Use uninterrupted outlet
b. Power outage
b. Reset time of day
c. Defective PC board
c. Replace PC board
3. No Softening/filtering display when water
is flowing.
a. Bypass valve in bypass position.
a. Put bypass valve in service position
b. Meter connection disconnected.
b. Connect meter to PC board
c. Restricted/stalled meter turbine.
c. Remove meter and check for rotation or foreign material
d. Defective meter.
d. Replace meter
e. Defective PC board.
e. Replace PC board
4. Control valve regenerates at wrong time
of day.
a. Power outages
a. Reset control valve to correct time of day
b. Time of day not set correctly
b. Reset to correct time of day
c. Time of regeneration incorrect
c. Reset regeneration time
d. Control valve set at “on O” (immediate regeneration)
d. Check control valve set-up procedure regeneration time
option
e. Control valve set at O
e. Check control valve set-up procedure regeneration time
option
5. ERROR followed by Code number:
Error Code 1001
– Unable to recognize
start of regeneration.
Error Code 1002
– Unexpected stall.
Error Code 1003
– Motor ran to long, timed
out trying to reach next cycle position.
Error Code 1004
– Motor ran to long, timed
out trying to reach home position.
If other Error Codes display contact the
factory.
a. Control valve has just been serviced
a. Press NEXT and REGEN for 3 seconds or unplug power
source jack (black wire) and plug back in to reset control
valve.
b. Foreign matter is lodged in control valve
b. Check piston and spacer stack assembly for foreign matter.
c. High drive forces on piston
c. Replace piston (s) and spacer stack assembly.
d. Control valve piston not in home position
d. Press NEXT and REGEN for 3 seconds or unplug power
source jack (black wire) and plug back in to reset control valve.
e. Motor not inserted fully to engage pinion, motor wires
broken or disconnected, motor failure
e. Check motor and wiring. Replace motor if necessary.
f. Drive gear label dirty or damaged, missing or broken
gear
f. Replace or clean drive gear.
g. Drive bracket incorrectly aligned to back plate
g. Reset drive bracket properly.
h. PC board is damaged or defective
h. Replace PC board.
i. PC board incorrectly aligned to drive bracket
i. Ensure PC board is correctly snapped onto drive bracket.
6. Control valve stalled in regeneration.
a. Motor not operating
a. Replace motor
b. No electric power at outlet
b. Repair outlet or use working outlet
c. Defective transformer
c. Replace transformer
d. Defective PC board
d. Replace PC board
e. Broken drive gear or drive cap assembly
e. Replace drive gear or drive cap assembly
f. Broken piston retainer
f. Replace drive cap assembly
g. Broken main or regenerant piston
g. Replace main or regenerant piston
7. Control valve does not regenerate
automatically when REGEN button is
depressed and held.
a. Transformer unplugged
a. Connect transformer
b. No electric power at outlet
b. Repair outlet or use working outlet
c. Broken drive gear or drive cap assembly
c. Replace drive gear or drive cap assembly
d. Defective PC board
d. Replace PC board
8. Control valve does not regenerate
automatically but does when REGEN button
is depressed.
a. Bypass valve in bypass position
a. Put control valve in service piston
b. Meter connection disconnected
b. Connect meter to PC board
c. Restricted/stalled meter turbine
c. Remove meter and check for rotation or foreign matter
d. Defective meter
d. Replace meter
e. Defective PC board
e. Replace PC board
f. Set-up error
f. Check control valve set-up procedure
9. Time of day flashes on and off.
a. Power has been out more than two hours, the
transformer was unplugged and then plugged back into
the wall outlet, the transformer plug was unplugged
and then plugged back into the board or the NEXT and
REGEN buttons were pressed to reset the valve.
a. Reset the time of day