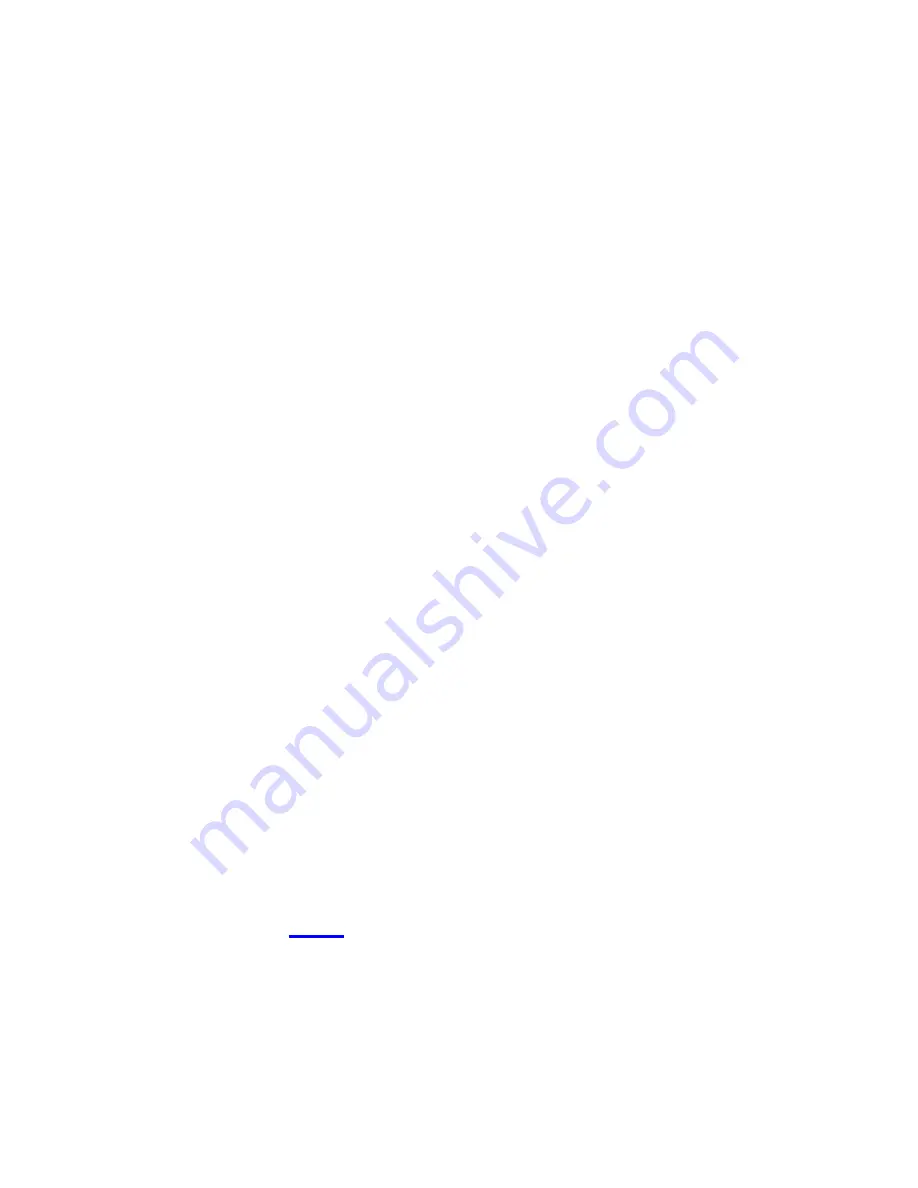
2. CLEANING AND SANITIZING INSTRUCTIONS
2.1 GENERAL INFORMATION
A. Lancer equipment (new or reconditioned) is shipped from the factory cleaned and sanitized in
accordance with NSF guidelines. This equipment must be cleaned and sanitized after
installation is complete, and the operator of the equipment must provide continuous
maintenance as required by this manual and/or state and local health department guidelines to
ensure proper operation and sanitation requirements are maintained.
NOTE:
The cleaning and sanitizing procedures provided herein pertain to the Lancer equipment
identified by this manual. If other equipment is being cleaned, follow the guidelines established
for that equipment.
B. Cleaning and sanitizing should be accomplished only by trained personnel. Sanitary gloves are
to be used during cleaning and sanitizing operations. Applicable safety precautions must be
observed. Instruction warnings on the product being used must be followed.
C. Water lines are not to be disconnected during the cleaning and sanitizing of syrup lines to avoid
contamination.
D. Do NOT use strong bleaches or detergents. They tend to discolor and/or corrode various
materials.
E. Do NOT use metal scrapers, sharp objects, steel wool, scouring pads, abrasives, solvents, etc.,
on the dispenser.
F. Do NOT use hot water above 140°F (60°C). This may damage certain materials.
2.2 REQUIRED CLEANING EQUIPMENT
A. Cleansers (for example, Ivory Liquid, Calgon, etc.) mixed with clean, potable water at a
temperature of 90 to 110 degrees Fahrenheit should be used to clean equipment. The mixture
ratio, using Ivory Liquid, is one (1) ounce of cleanser to two (2) gallons of water. A minimum of
five (5) gallons of cleaning mixture should be prepared. Any equivalent cleanser may be used
as long as it provides a caustic based, non-perfumed, easily rinsed mixture containing at least
two (2) percent sodium hydroxide (NaOH). Rinsing must be thorough and use clean, potable
water which is also at a temperature of 90° to 110°F.
NOTE:
Extended lengths of product lines may require that an additional volume of cleaning solution
be prepared.
B. Sanitizing solutions should be prepared in accordance with the manufacturer’s written
recommendations and safety guidelines. The solution must provide 200 parts per million (PPM)
available chlorine. A minimum of five (5) gallons of sanitizing solution should be prepared. Any
sanitizing solution may be used as long as it is prepared in accordance with the manufacturer’s
written recommendations and safety guidelines, and provides 200 parts per million (PPM)
available chlorine. Sanitizing solution is to be purged from line(s) and equipment by flushing
with product only until there is no after taste. Do not rinse with water.
NOTE:
Please note that a fresh water rinse cannot follow sanitization of equipment. Purge only with
the end use product until there is no after taste in the product. This is an NSF requirement.
Extended lengths of product lines may require that an additional volume of sanitizing solution
be prepared.
C. Other:
1. Clean cloth towels.
2. Bucket.
3. Small brush (PN
) - included with installation kit.
4. Extra nozzle.
5. Sanitary gloves.
2.3 DAILY CLEANING
Using a mild detergent solution, clean Top Cover and all exterior stainless steel surfaces. Clean
exterior of dispensing valves and ice chute. Remove Cup Rest. Clean Drip Tray and Cup Rest, and
replace Cup Rest. Wipe clean all splash areas using a damp cloth soaked in cleaning solution.
Clean beverage valves as specified by the valve manufacturer.
12